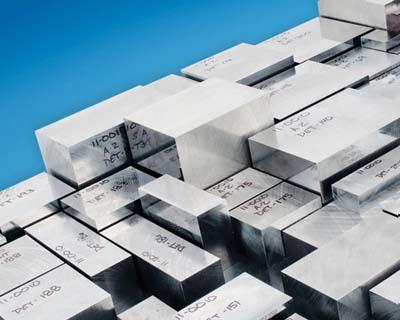
Diehl Steel A-2 air hardening tool steel offers good wear resistance and machinability, high compressive strength and very good non-deforming properties. The company typically ships in-stock items within 24-48 hours.
Available in flats, hollowbar, rounds, squares, metric and standard forms, A-2 tool steel from Diehl also features deep hardening and high dimensional stability after hardening and tempering. By taking advantage of the company's Accu-Square service, orders can be machined to tool maker tolerances prior to shipping.
Contact Details
Related Glossary Terms
- hardening
hardening
Process of increasing the surface hardness of a part. It is accomplished by heating a piece of steel to a temperature within or above its critical range and then cooling (or quenching) it rapidly. In any heat-treatment operation, the rate of heating is important. Heat flows from the exterior to the interior of steel at a definite rate. If the steel is heated too quickly, the outside becomes hotter than the inside and the desired uniform structure cannot be obtained. If a piece is irregular in shape, a slow heating rate is essential to prevent warping and cracking. The heavier the section, the longer the heating time must be to achieve uniform results. Even after the correct temperature has been reached, the piece should be held at the temperature for a sufficient period of time to permit its thickest section to attain a uniform temperature. See workhardening.
- machinability
machinability
The relative ease of machining metals and alloys.
- tempering
tempering
1. In heat-treatment, reheating hardened steel or hardened cast iron to a given temperature below the eutectoid temperature to decrease hardness and increase toughness. The process also is sometimes applied to normalized steel. 2. In nonferrous alloys and in some ferrous alloys (steels that cannot be hardened by heat-treatment), the hardness and strength produced by mechanical or thermal treatment, or both, and characterized by a certain structure, mechanical properties or reduction in area during cold working.
- wear resistance
wear resistance
Ability of the tool to withstand stresses that cause it to wear during cutting; an attribute linked to alloy composition, base material, thermal conditions, type of tooling and operation and other variables.