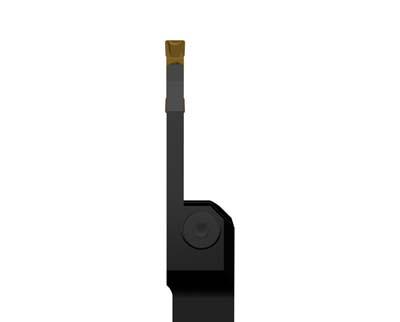
Seco Tools Inc. has expanded its versatile MDT (Multi-Directional Turning) system with hundreds of new holders to accommodate a broader range of standard and special machining applications. These new offerings include long-reach holders able to handle up to 8 times the insert width, face machining holders available in Seco's unique Jetstream tooling system in up to 6 times insert width, an expanded internal operations product line, and an array of modular systems including 45-degree holders and long reach machining blades that can achieve up to 5 times the insert width. The MDT system uses a single toolholder and insert for turning, profiling and grooving in both axial and radial directions. The clamping action of the MDT toolholder provides a rigid and stable contact surface. MDT's versatility offers improved productivity through fewer tool changes and machine stops, according to the company. It also simplifies tool handling and stocking requirements by replacing the need for several conventional tools. The MDT system can be used for turning, profiling, grooving and parting off. Suitable applications include turning of parts with many different diameters, complicated profiles and grooves. For complex parts of this type, several standard and special tools can be replaced by one Seco MDT tool. Savings can be achieved through fewer tool changes and reduced stock.
Contact Details
Related Glossary Terms
- grooving
grooving
Machining grooves and shallow channels. Example: grooving ball-bearing raceways. Typically performed by tools that are capable of light cuts at high feed rates. Imparts high-quality finish.
- parting
parting
When used in lathe or screw-machine operations, this process separates a completed part from chuck-held or collet-fed stock by means of a very narrow, flat-end cutting, or parting, tool.
- profiling
profiling
Machining vertical edges of workpieces having irregular contours; normally performed with an endmill in a vertical spindle on a milling machine or with a profiler, following a pattern. See mill, milling machine.
- toolholder
toolholder
Secures a cutting tool during a machining operation. Basic types include block, cartridge, chuck, collet, fixed, modular, quick-change and rotating.
- turning
turning
Workpiece is held in a chuck, mounted on a face plate or secured between centers and rotated while a cutting tool, normally a single-point tool, is fed into it along its periphery or across its end or face. Takes the form of straight turning (cutting along the periphery of the workpiece); taper turning (creating a taper); step turning (turning different-size diameters on the same work); chamfering (beveling an edge or shoulder); facing (cutting on an end); turning threads (usually external but can be internal); roughing (high-volume metal removal); and finishing (final light cuts). Performed on lathes, turning centers, chucking machines, automatic screw machines and similar machines.