Many options are available for removing stock and shaping workpieces. Broaching is one of the most productive, underutilized—and least understood.
Broaching is similar to shaping in that neither the tool nor the workpiece rotate relative to each other. In most cases, broaching is accomplished by holding the workpiece stationary and moving the broach tool past—and through—the workpiece to initiate the chip-forming process. The most familiar broaching operation is likely for the creation of square keyways in bored holes, where the keyway is produced by pushing a broach through a hole using an alignment bushing.
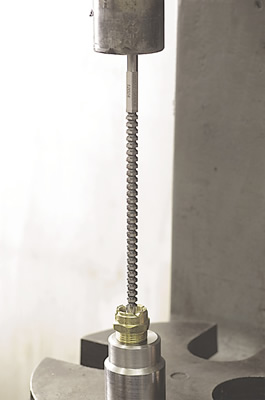
This hexagon-shaped broach it pushed through a drilled hole to produce a hexagon-shaped hole. Each tooth is slightly larger than the previous tooth, and the change in size from tooth to tooth is equal to the DOC per tooth. Image courtesy Hassay Savage.
Broach construction is similar regardless of the application. Broaches can be constructed of various materials, including HSS and carbide, and some even accept carbide inserts. HSS broaches are by far the most common because HSS provides adequate wear resistance and toughness.
No matter what material they are made from, all broaches function according to the same principle. The broach form is a mirror image of the desired form in the part. Broaches are constructed so each tooth is slightly larger than the previous tooth. This staggered effect allows each tooth to remove an incremental amount of material as the broach moves past the workpiece. Typically, each tooth will remove 0.001 " to 0.003 " of material, depending on the application and capability of the broaching machine.
Broaching is often used for geometric forms that cannot be produced by other means or economically by other processes, such as internal splines found on the input shaft of a transmission.
Broaching also can be used in place of milling, because it can quickly and accurately remove large amounts of material. This is often called surface or slab broaching.
Because of the relatively light DOC, broaching can create intricate and close-tolerance forms. Maintaining a dimensional tolerance of 0.0005 " on complex forms is possible with a rigid machine and well-made broaches.
One of the most significant broaching advantages is cost. Broaches and broaching machines can have high acquisition costs, but, because broaching is so efficient, the cost per part is typically low.
When I worked in the automotive industry and made power steering gears, a set of broach tools for the gear rack (rack and pinion steering) cost about $25,000 per set, and a new horizontal broaching machine cost $750,000. However, a set of properly maintained tools could produce 100,000 parts. Good tools paired with a good machine yielded a robust process that produced a gear rack every 40 seconds while maintaining a 0.0005 " dimensional tolerance on the gear teeth.
Broaching machines are available is many sizes; some are no bigger than a Bridgeport-type knee mill while others are the size of a small house. The size is determined by the power necessary to drive the broach, as well as the length of the broach and workpiece.
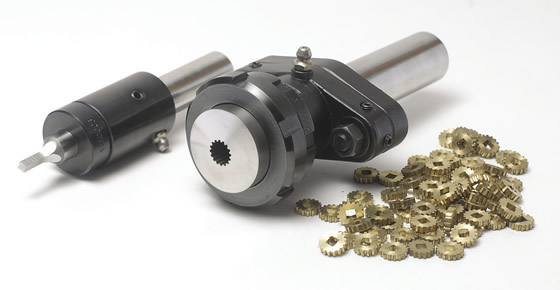
Internal squares and external splines are rotary-broached into small brass parts. Image courtesy Slater Tools.
Broaching machines have a stroke length, or maximum distance they can travel, so the broach must be manufactured accordingly. The necessary stroke for a given job is determined by the length of the broach, which, in turn, is determined by the amount of material to be removed. Each broach tooth removes a fixed amount of stock, which means it is necessary to increase the number of teeth on the broach as the amount of stock increases. As the number of teeth increases, so does the broach’s length.
The power of a broaching machine is given in tons. Therefore, a 40-ton machine is capable of doing more work than a 5-ton machine. Tonnage requirements, like stroke requirements, are determined by the tool and material. Obviously, more power is required to broach high-carbon steel like 4140 than materials like brass or aluminum. The power requirement is determined by the number of teeth engaged in the cut. So a broach that has a single row of teeth requires less power than one that has multiple rows.
Along with the tonnage and the stroke, a specification is provided for cutting speed. Knowing the cutting speed helps to determine if the machine is correct for the application. If the cutting speed is too fast, premature damage to the broach can occur. Cutting speeds that are too slow are less efficient. Like other machining operations, cutting speed will be based on the workpiece material, part geometry, coolant and tool coatings.
Broaching is applicable in high-volume machining where dedicated equipment is justified, including automotive and gun parts. It is also applicable when alternatives are expensive or not capable of supporting the required production rates. It is common for some shops to outsource EDM work on parts that could be broached more efficiently.
Broaching does not have to be performed on a broaching machine. It can be done on milling machines, lathes and other types of equipment. This flexibility would eliminate the secondary operation needed for a part that must be broached and milled, for example. It can also replace milling to reduce cycle times, improve surface finishes and create intricate forms.
A little research—and creativity—may uncover broaching opportunities in your shop. CTE
About the Author: Christopher Tate is engineering manager, combustion shop, for Mitsubishi Hitachi Power Systems Americas, Savannah (Ga.) Machinery Works. Email: chris23tate@gmail.com.
Related Glossary Terms
- broach
broach
Tapered tool, with a series of teeth of increasing length, that is pushed or pulled into a workpiece, successively removing small amounts of metal to enlarge a hole, slot or other opening to final size.
- broaching
broaching
Operation in which a cutter progressively enlarges a slot or hole or shapes a workpiece exterior. Low teeth start the cut, intermediate teeth remove the majority of the material and high teeth finish the task. Broaching can be a one-step operation, as opposed to milling and slotting, which require repeated passes. Typically, however, broaching also involves multiple passes.
- broaching machine
broaching machine
Machine designed specifically to run broaching tools. It is typically designated by operating characteristics (pull, push, rotary, continuous, blind-spline), type of power used (hydraulic, mechanical) and tonnage ratings. Broaching is also performed on arbor presses (manual and powered).
- bushing
bushing
Cylindrical sleeve, typically made from high-grade tool steel, inserted into a jig fixture to guide cutting tools. There are three main types: renewable, used in liners that in turn are installed in the jig; press-fit, installed directly in the jig for short production runs; and liner (or master), installed permanently in a jig to receive renewable bushing.
- coolant
coolant
Fluid that reduces temperature buildup at the tool/workpiece interface during machining. Normally takes the form of a liquid such as soluble or chemical mixtures (semisynthetic, synthetic) but can be pressurized air or other gas. Because of water’s ability to absorb great quantities of heat, it is widely used as a coolant and vehicle for various cutting compounds, with the water-to-compound ratio varying with the machining task. See cutting fluid; semisynthetic cutting fluid; soluble-oil cutting fluid; synthetic cutting fluid.
- cutting speed
cutting speed
Tangential velocity on the surface of the tool or workpiece at the cutting interface. The formula for cutting speed (sfm) is tool diameter 5 0.26 5 spindle speed (rpm). The formula for feed per tooth (fpt) is table feed (ipm)/number of flutes/spindle speed (rpm). The formula for spindle speed (rpm) is cutting speed (sfm) 5 3.82/tool diameter. The formula for table feed (ipm) is feed per tooth (ftp) 5 number of tool flutes 5 spindle speed (rpm).
- electrical-discharge machining ( EDM)
electrical-discharge machining ( EDM)
Process that vaporizes conductive materials by controlled application of pulsed electrical current that flows between a workpiece and electrode (tool) in a dielectric fluid. Permits machining shapes to tight accuracies without the internal stresses conventional machining often generates. Useful in diemaking.
- gang cutting ( milling)
gang cutting ( milling)
Machining with several cutters mounted on a single arbor, generally for simultaneous cutting.
- high-speed steels ( HSS)
high-speed steels ( HSS)
Available in two major types: tungsten high-speed steels (designated by letter T having tungsten as the principal alloying element) and molybdenum high-speed steels (designated by letter M having molybdenum as the principal alloying element). The type T high-speed steels containing cobalt have higher wear resistance and greater red (hot) hardness, withstanding cutting temperature up to 1,100º F (590º C). The type T steels are used to fabricate metalcutting tools (milling cutters, drills, reamers and taps), woodworking tools, various types of punches and dies, ball and roller bearings. The type M steels are used for cutting tools and various types of dies.
- milling
milling
Machining operation in which metal or other material is removed by applying power to a rotating cutter. In vertical milling, the cutting tool is mounted vertically on the spindle. In horizontal milling, the cutting tool is mounted horizontally, either directly on the spindle or on an arbor. Horizontal milling is further broken down into conventional milling, where the cutter rotates opposite the direction of feed, or “up” into the workpiece; and climb milling, where the cutter rotates in the direction of feed, or “down” into the workpiece. Milling operations include plane or surface milling, endmilling, facemilling, angle milling, form milling and profiling.
- milling machine ( mill)
milling machine ( mill)
Runs endmills and arbor-mounted milling cutters. Features include a head with a spindle that drives the cutters; a column, knee and table that provide motion in the three Cartesian axes; and a base that supports the components and houses the cutting-fluid pump and reservoir. The work is mounted on the table and fed into the rotating cutter or endmill to accomplish the milling steps; vertical milling machines also feed endmills into the work by means of a spindle-mounted quill. Models range from small manual machines to big bed-type and duplex mills. All take one of three basic forms: vertical, horizontal or convertible horizontal/vertical. Vertical machines may be knee-type (the table is mounted on a knee that can be elevated) or bed-type (the table is securely supported and only moves horizontally). In general, horizontal machines are bigger and more powerful, while vertical machines are lighter but more versatile and easier to set up and operate.
- shaping
shaping
Using a shaper primarily to produce flat surfaces in horizontal, vertical or angular planes. It can also include the machining of curved surfaces, helixes, serrations and special work involving odd and irregular shapes. Often used for prototype or short-run manufacturing to eliminate the need for expensive special tooling or processes.
- tolerance
tolerance
Minimum and maximum amount a workpiece dimension is allowed to vary from a set standard and still be acceptable.
- wear resistance
wear resistance
Ability of the tool to withstand stresses that cause it to wear during cutting; an attribute linked to alloy composition, base material, thermal conditions, type of tooling and operation and other variables.