Grooving most any material creates friction, generating heat that directly and negatively impacts tool life. The benefits of properly applying water- or oil-based coolants that reduce friction are easy to comprehend.
Coolant manufacturers engineer their fluids to reduce friction through lubrication and heat dissipation. Less heat when grooving extends tool life, improves surface finishes and increases the potential material-removal rate. Metalworking fluids also help transport chips from the cutting zone and can prevent corrosion in the machine.
Fluid Basics
The selection of a suitable fluid requires a basic understanding of the coolant formulation and the application in which it will be applied.
Oil-based lubricants, with or without additives, are utilized to achieve a fine surface quality on the final component. These petroleum or mineral oil products offer excellent lubricity, help prevent rust and are fairly easy to maintain.
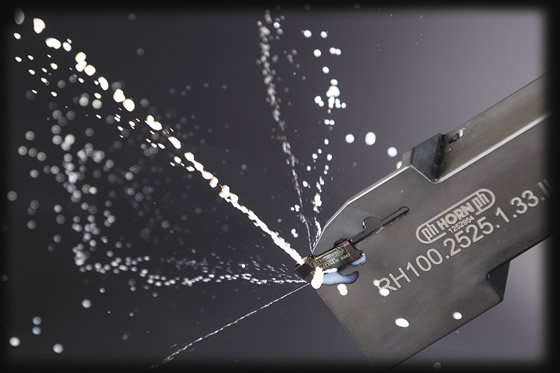
All images courtesy Horn USA
Water-soluble coolants or emulsions, free of mineral oil, are commonly used when cooling takes priority over surface finish. These oil-in-water, “soapy” solutions lubricate and can contain special additives for protection against rust.
Synthetic coolants contain no petroleum or mineral oils and are engineered to efficiently transfer heat. These fluids are considered nonflammable, microbial resistant and contain rust inhibitors.
Going Dry
Cooling methods that do not have lubricating effects include cryogenic gases, compressed air and dry machining. Cryogenic cooling involves the use of liquid gases, such as nitrogen, at temperatures as low as -321° F (-196° C). Special delivery systems, such as insulated tanks, vacuum-insulated hoses and tools specially designed to cope with such harsh temperatures, are needed. Compared to liquid nitrogen, CO2 compressed into liquid form requires fewer resources to maintain and cope with temperatures as low as -108° F (-78° C). Both techniques provide unique advantages when grooving titanium and nickel-based alloys. These materials are heat resistant and the machining process creates high thermal loads at the cutting edge. Without proper coatings or cooling methods for heat transfer, the excessive heat leads to rapid edge wear.
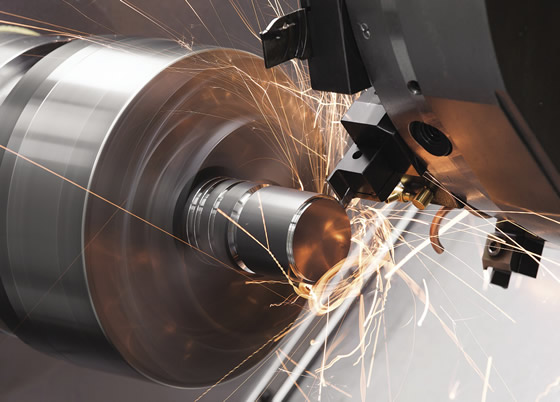
Hard turning with PCBN tools is possible under dry conditions.
Efforts to reduce the cost of machining processes have led to innovations in dry machining methods. Several years ago, the European automotive industry calculated that 14 to 16 percent of machining costs could be attributed to using, maintaining and disposing of cutting fluids. New advances in tool coatings enable manufacturers to utilize the dry cutting of investment castings, as well as other materials. When machining fiber-reinforced plastics, ceramics, graphite and carbide in the green (unsintered) state, compressed air is used to blow dust particles from the cutting area. The dust is then collected by a vacuum system for recycling or disposal.
In contrast, flood cooling directs large volumes of coolant toward the working area. Providing such large volumes of fluid is effective at cooling, lubricating and removing large chips. This is generally sufficient provided there are few obstructions between the workpiece and cutting tool.
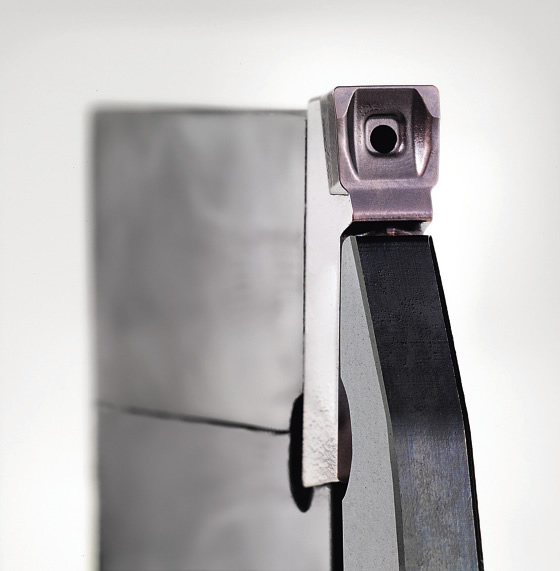
Horn says its new S100 insert for grooving and parting-off precisely delivers lubricating and cooling fluids. The “.3V” chipbreaker geometry and wear-resistant TiAlN coating for machining stainless steels is an expansion of the existing S100 system. The coolant port works directly at the cutting zone and creates a focused coolant jet, reducing the chance of built-up edge and assisting in chip formation.
However, using high-pressure coolant provides significant advantages over flooding the workpiece with large volumes of coolant. With as little as 73 psi (5 bar) of pressure, tool wear begins to decrease compared to using flood cooling alone, which increases productive machining time. Built-up edge begins to decrease when the pressure exceeds 290 psi (20 bar), decreasing machine downtime. In addition, breaking chips in long-chipping materials, such as high-strength nickel-base alloys, is possible above 2,175 psi (150 bar).
Cooling the cutting zone and removing chips are the primary goals whether the choice is flood coolant, minimum-quantity lubrication (MQL) or cooling with compressed gases. Machine capabilities, tool limitations, component configuration and fixtures can complicate a delivery method. This has led most grooving tool manufacturers to develop tooling with through-coolant capabilities.
In the Zone
In each of the conventional fluid cooling processes, oil- or water-based coolants are directed toward the cutting edge of the grooving tool but may not reach the cutting zone. Steam is generated as heat builds at the tool/workpiece interface with fluid in close proximity. As a result, microscopic steam bubbles form at temperatures exceeding 1,832° F (1,000° C) and prevent fluids from contacting the working area.
Pressurized jets of coolant in excess of 725 psi (50 bar) can overcome or penetrate these steam bubbles. This requires coolant to be forced between the cutting edge and the workpiece material.
Pressurized streams can be difficult to maintain with external tubes and nozzles, especially in grooves or deep holes where flanking material becomes an obstruction. This necessitates constant monitoring.
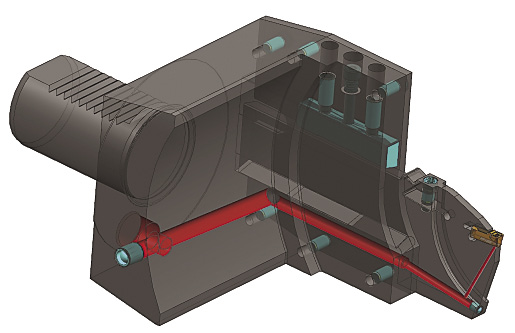
A VDI holder with coolant channel (shown in red) supplies coolant directly through an indexable insert.
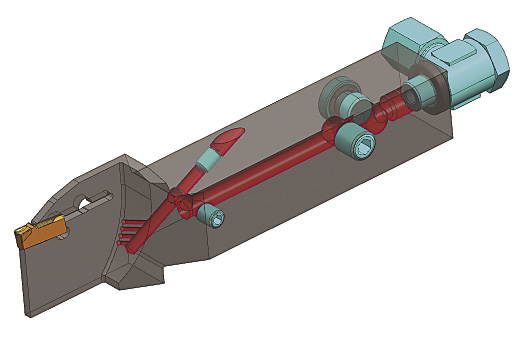
A square shank part-off holder with coolant jets provides pressurized fluid below the cutting zone.
The growing demand for efficiency when grooving modern steels with their increased levels of strength and toughness have led to improvements in cutting tools. Innovative tool manufacturers are addressing these trends and have developed new cooling processes involving high-pressure streams of coolants and lubricants. These developments include a variety of methods to transport fluids through a toolholder and aim a focused coolant jet directly toward the workpiece via coolant nozzles, clamping mechanisms or other suitable surface. Grooving tools that feature internal plumbing enable fluids to reach their intended destination and reliably evacuate chips. As a result, coolant delivered through tooling has considerably increased tool life and increased productivity by improving process reliability.
Managing Chips
Effectively cooling the working area requires the supply of coolant to contact the cutting zone between the tool and machined surface, which is particularly important when parting-off and grooving because chip management is a concern. The cutting zone can be difficult to efficiently cool as the ribbon of material being removed curls back onto itself.
This ribbon continues to build and begins to resemble a watch spring, blocking coolant from reaching the tool’s cutting edge. Complex chip-forming geometries assist in forcing the material to fold and fracture into smaller pieces, but these chips continue to obstruct the working area.
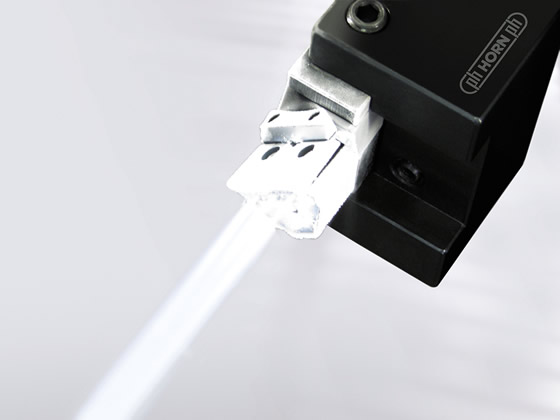
Cryogenic cooling with liquid nitrogen requires a tool that can cope with temperatures as low as -321° F.
Advancements in carbide substrates have made it possible to place a coolant port just behind the cutting edge of an insert. While solid tools with through-coolant capability have been on the market for many years, high-pressure coolant streams and cryogenic liquids are now forced through toolholders and the indexable cutting inserts they support.
Cutting fluids delivered through an insert that are accurately directed into the cutting zone aid in chip formation, chip removal and effective cooling of the cutting zone. Pinpoint coolant placement further reduces tool wear, increases process reliability and allows higher cutting parameters.
When it comes to cooling, the requirements of the application itself are just as important as choosing the correct grooving tool. It is also crucial to look at the possibilities offered by the machines in question, coolants on the market and available delivery methods. CTE
Related Glossary Terms
- alloys
alloys
Substances having metallic properties and being composed of two or more chemical elements of which at least one is a metal.
- built-up edge ( BUE)
built-up edge ( BUE)
1. Permanently damaging a metal by heating to cause either incipient melting or intergranular oxidation. 2. In grinding, getting the workpiece hot enough to cause discoloration or to change the microstructure by tempering or hardening.
- ceramics
ceramics
Cutting tool materials based on aluminum oxide and silicon nitride. Ceramic tools can withstand higher cutting speeds than cemented carbide tools when machining hardened steels, cast irons and high-temperature alloys.
- chipbreaker
chipbreaker
Groove or other tool geometry that breaks chips into small fragments as they come off the workpiece. Designed to prevent chips from becoming so long that they are difficult to control, catch in turning parts and cause safety problems.
- coolant
coolant
Fluid that reduces temperature buildup at the tool/workpiece interface during machining. Normally takes the form of a liquid such as soluble or chemical mixtures (semisynthetic, synthetic) but can be pressurized air or other gas. Because of water’s ability to absorb great quantities of heat, it is widely used as a coolant and vehicle for various cutting compounds, with the water-to-compound ratio varying with the machining task. See cutting fluid; semisynthetic cutting fluid; soluble-oil cutting fluid; synthetic cutting fluid.
- grooving
grooving
Machining grooves and shallow channels. Example: grooving ball-bearing raceways. Typically performed by tools that are capable of light cuts at high feed rates. Imparts high-quality finish.
- hard turning
hard turning
Single-point cutting of a workpiece that has a hardness value higher than 45 HRC.
- indexable insert
indexable insert
Replaceable tool that clamps into a tool body, drill, mill or other cutter body designed to accommodate inserts. Most inserts are made of cemented carbide. Often they are coated with a hard material. Other insert materials are ceramic, cermet, polycrystalline cubic boron nitride and polycrystalline diamond. The insert is used until dull, then indexed, or turned, to expose a fresh cutting edge. When the entire insert is dull, it is usually discarded. Some inserts can be resharpened.
- lubricity
lubricity
Measure of the relative efficiency with which a cutting fluid or lubricant reduces friction between surfaces.
- metalworking
metalworking
Any manufacturing process in which metal is processed or machined such that the workpiece is given a new shape. Broadly defined, the term includes processes such as design and layout, heat-treating, material handling and inspection.
- minimum-quantity lubrication
minimum-quantity lubrication
Use of cutting fluids of only a minute amount—typically at a flow rate of 50 to 500 ml/hr.—which is about three to four orders of magnitude lower than the amount commonly used in flood cooling. The concept addresses the issues of environmental intrusiveness and occupational hazards associated with the airborne cutting fluid particles on factory shop floors. The minimization of cutting fluid also saves lubricant costs and the cleaning cycle time for workpieces, tooling and machines. Sometimes referred to as “near-dry lubrication” or “microlubrication.”
- polycrystalline cubic boron nitride ( PCBN)
polycrystalline cubic boron nitride ( PCBN)
Cutting tool material consisting of polycrystalline cubic boron nitride with a metallic or ceramic binder. PCBN is available either as a tip brazed to a carbide insert carrier or as a solid insert. Primarily used for cutting hardened ferrous alloys.
- shank
shank
Main body of a tool; the portion of a drill or similar end-held tool that fits into a collet, chuck or similar mounting device.
- stainless steels
stainless steels
Stainless steels possess high strength, heat resistance, excellent workability and erosion resistance. Four general classes have been developed to cover a range of mechanical and physical properties for particular applications. The four classes are: the austenitic types of the chromium-nickel-manganese 200 series and the chromium-nickel 300 series; the martensitic types of the chromium, hardenable 400 series; the chromium, nonhardenable 400-series ferritic types; and the precipitation-hardening type of chromium-nickel alloys with additional elements that are hardenable by solution treating and aging.
- titanium aluminum nitride ( TiAlN)
titanium aluminum nitride ( TiAlN)
Often used as a tool coating. AlTiN indicates the aluminum content is greater than the titanium. See coated tools.
- toolholder
toolholder
Secures a cutting tool during a machining operation. Basic types include block, cartridge, chuck, collet, fixed, modular, quick-change and rotating.
- turning
turning
Workpiece is held in a chuck, mounted on a face plate or secured between centers and rotated while a cutting tool, normally a single-point tool, is fed into it along its periphery or across its end or face. Takes the form of straight turning (cutting along the periphery of the workpiece); taper turning (creating a taper); step turning (turning different-size diameters on the same work); chamfering (beveling an edge or shoulder); facing (cutting on an end); turning threads (usually external but can be internal); roughing (high-volume metal removal); and finishing (final light cuts). Performed on lathes, turning centers, chucking machines, automatic screw machines and similar machines.