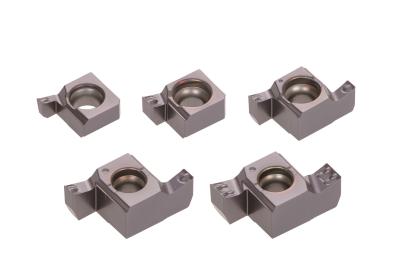
Tungaloy is expanding its SNG line of internal grooving tools to include GMR, a new insert geometry that enables effective chip control and evacuation in internal grooving applications.
Chip evacuation is a major issue with internal grooving. The GMR geometry addresses this by offering a 3D chipbreaker pressed in the cutting edge and optimized rake angle that removes the chip out of the hole and reduces cutting force. This minimizes the risk of chip re-cuts which can cause tool breakage, especially when machining small diameters. This provides improved cycle time and productivity.
Various toolholder sizes are available for internal grooving with a minimum bore diameter (DMIN) of 8 mm (0.31") up to 24 mm (0.95"). Carbide shank toolholders are also available for shank diameters of 16 mm (0.63") and smaller for added tool rigidity during long-reach applications where vibration control is vital.
At a Glance
Superior chip control and evacuation
GMR geometry ensures process security in a wide range of parameters
Available in AH7025 covering various materials, including carbon and alloy steels, stainless steel, and heat-resistant alloys
Total of five inserts to be added
Contact Details
Related Glossary Terms
- alloy steels
alloy steels
Steel containing specified quantities of alloying elements (other than carbon and the commonly accepted amounts of manganese, sulfur and phosphorus) added to cause changes in the metal’s mechanical and/or physical properties. Principal alloying elements are nickel, chromium, molybdenum and silicon. Some grades of alloy steels contain one or more of these elements: vanadium, boron, lead and copper.
- alloys
alloys
Substances having metallic properties and being composed of two or more chemical elements of which at least one is a metal.
- chipbreaker
chipbreaker
Groove or other tool geometry that breaks chips into small fragments as they come off the workpiece. Designed to prevent chips from becoming so long that they are difficult to control, catch in turning parts and cause safety problems.
- cutting force
cutting force
Engagement of a tool’s cutting edge with a workpiece generates a cutting force. Such a cutting force combines tangential, feed and radial forces, which can be measured by a dynamometer. Of the three cutting force components, tangential force is the greatest. Tangential force generates torque and accounts for more than 95 percent of the machining power. See dynamometer.
- grooving
grooving
Machining grooves and shallow channels. Example: grooving ball-bearing raceways. Typically performed by tools that are capable of light cuts at high feed rates. Imparts high-quality finish.
- rake
rake
Angle of inclination between the face of the cutting tool and the workpiece. If the face of the tool lies in a plane through the axis of the workpiece, the tool is said to have a neutral, or zero, rake. If the inclination of the tool face makes the cutting edge more acute than when the rake angle is zero, the rake is positive. If the inclination of the tool face makes the cutting edge less acute or more blunt than when the rake angle is zero, the rake is negative.
- shank
shank
Main body of a tool; the portion of a drill or similar end-held tool that fits into a collet, chuck or similar mounting device.
- toolholder
toolholder
Secures a cutting tool during a machining operation. Basic types include block, cartridge, chuck, collet, fixed, modular, quick-change and rotating.