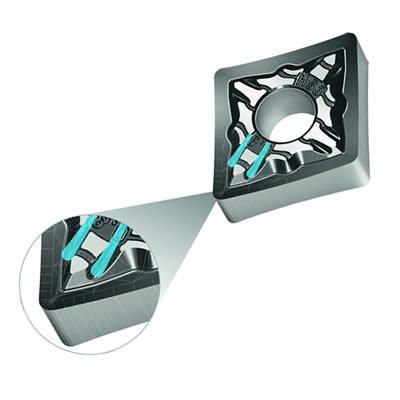
Walter says it has introduced a new and innovative cutting geometry, the MS3, teamed with a new high tech grade, WSM01. The new WSM01 grade, manufactured using the HiPIMS (high-power impulse magnetron sputtering) method, provides extremely smooth surfaces that are characterized by excellent layer thickness, outstanding layer bonding and high-level wear resistance, according to the company.
The combination of the HiPIMS PVD coating and the new MS3 geometry is ideal for machining ISO S materials with difficult cutting properties, such as high-temperature alloys, titanium, cobalt-based and nickel-based alloys. Secondary applications for this new grade/geometry combination are steel, stainless steel and nonferrous material groups (ISO P, M and N).
Negative inserts with MS3 geometry are available with both sintered and fully ground circumference. Their smooth surface and extremely sharp cutting edges keep build up to a minimum and ensure a high quality surface finish. This makes it significantly easier to reliably manufacture burr-free components. The new insert is particularly suitable for machining unstable or thin-walled components and setups with long overhangs, since its highly positive geometry provides low cutting pressure and prevents vibration. The MS3 insert – much like Walter's RM5 – is equipped with coolant jet guiding geometry to ensure optimal cooling directly on the cutting edge. It is well-suited to turning applications and to medium machining applications in the aerospace industry, medical components manufacturing, general mechanical engineering and the automotive industry.
Contact Details
Related Glossary Terms
- alloys
alloys
Substances having metallic properties and being composed of two or more chemical elements of which at least one is a metal.
- coolant
coolant
Fluid that reduces temperature buildup at the tool/workpiece interface during machining. Normally takes the form of a liquid such as soluble or chemical mixtures (semisynthetic, synthetic) but can be pressurized air or other gas. Because of water’s ability to absorb great quantities of heat, it is widely used as a coolant and vehicle for various cutting compounds, with the water-to-compound ratio varying with the machining task. See cutting fluid; semisynthetic cutting fluid; soluble-oil cutting fluid; synthetic cutting fluid.
- physical vapor deposition ( PVD)
physical vapor deposition ( PVD)
Tool-coating process performed at low temperature (500° C), compared to chemical vapor deposition (1,000° C). Employs electric field to generate necessary heat for depositing coating on a tool’s surface. See CVD, chemical vapor deposition.
- turning
turning
Workpiece is held in a chuck, mounted on a face plate or secured between centers and rotated while a cutting tool, normally a single-point tool, is fed into it along its periphery or across its end or face. Takes the form of straight turning (cutting along the periphery of the workpiece); taper turning (creating a taper); step turning (turning different-size diameters on the same work); chamfering (beveling an edge or shoulder); facing (cutting on an end); turning threads (usually external but can be internal); roughing (high-volume metal removal); and finishing (final light cuts). Performed on lathes, turning centers, chucking machines, automatic screw machines and similar machines.
- wear resistance
wear resistance
Ability of the tool to withstand stresses that cause it to wear during cutting; an attribute linked to alloy composition, base material, thermal conditions, type of tooling and operation and other variables.