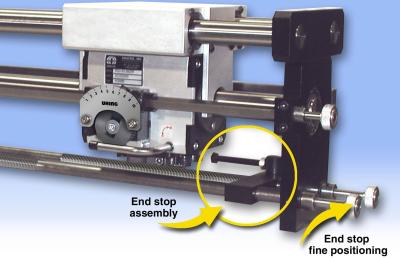
Amacoil-Uhing Model RG linear drives now feature an option for fine adjustment of maximum travel distance. On the standard Amacoil-Uhing drive assembly, the end stops limiting travel distance are set by hand. With the new option, the end stops ride on threaded rods with control knobs on both ends. Turning the rods moves the end stops in extremely small increments permitting very fine adjustments to the maximum stroke length. This facilitates accurate placement of the end stops for precisely establishing the linear drive reversal points.
The fine stroke option is useful in linear motion applications where accuracy in setting the reversal points enhances process accuracy and integrity. Example applications include spray coating, scanning, level winding, scoring and other reciprocating linear motion processes where the travel limits of the linear drive significantly affect the application results. An additional benefit of the fine control option is that operators may adjust the travel distance while the system is running, without placing hands near moving parts and risking injury.
The Model RG drive is used in various types of production equipment including converting/packaging machinery, wire/cable spooling equipment and other automated machinery with a linear motion component. Uhing Model RG drives are available in nineteen sizes with axial thrust from 7 to 800 pounds. The drives do not require a complex electronic control system because travel speed and direction are mechanically controlled independent of the drive motor. This helps reduce design costs and simplifies operation and maintenance. Periodic light lubrication of the shaft is the only maintenance required. Amacoil representatives can help with correct size selection for almost any application.
Related Glossary Terms
- turning
turning
Workpiece is held in a chuck, mounted on a face plate or secured between centers and rotated while a cutting tool, normally a single-point tool, is fed into it along its periphery or across its end or face. Takes the form of straight turning (cutting along the periphery of the workpiece); taper turning (creating a taper); step turning (turning different-size diameters on the same work); chamfering (beveling an edge or shoulder); facing (cutting on an end); turning threads (usually external but can be internal); roughing (high-volume metal removal); and finishing (final light cuts). Performed on lathes, turning centers, chucking machines, automatic screw machines and similar machines.