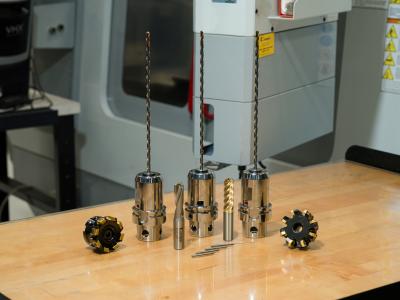
Kennametal Inc. is expanding its metal cutting tools and solutions portfolio with eight new products that offer improved performance, wear resistance and productivity for a wide range of applications across end markets including aerospace, medical, energy and transportation as well as general engineering.
“Our latest product expansion includes best-in-class features and advanced technology for metal cutting applications. We’re focused on designing and delivering solutions that combine industry-leading innovation and shop floor perspective to bring new levels of efficiency, productivity and performance to our customers,” said Vice President of Global Product Management Scott Etling.
The launch includes eight products that expand on and support existing platforms in delivering superior performance across multiple applications as well as address common machining challenges:
- Drill Fix PRO™ is an upgrade to Drill Fix—an existing indexable drilling platform in the Kennametal product line. Designed for extended tool life and smooth drilling at high metal removal rates, Drill Fix PRO delivers highvolume coolant flow with a wiper included in every outboard insert.
KenDrill™ Deep HPR is a material specific, deep-hole drill with broad diameter ranges and length variations. Made specifically for drilling steel and cast iron, KenDrill Deep HPR boosts performance, productivity and tool life.
- KenDrill™ Micro is Kennametal’s first comprehensive micro drilling portfolio for short and deep-hole applications. This versatile tooling set offers the best process reliability and longevity in small part machining applications.
- Face milling operations are enhanced with the expansion of Kennametal’s Dodeka™ series, featuring super high positive inserts with 12 true cutting edges per insert.
- Combining proprietary coating technology with next generation wear and oxidation resistance, Kennametal’s new solid end milling grade KCSM15A offers new levels of reliability and output. The new grade launches with the HARVI™ III, HARVI III Aero, HARVI II Long and RSM II platforms—proven performers in multiple industries and applications.
- Kennametal’s new stainless steel and hightemp alloy indexable drilling grades KCMS40 and KCMS35 are compatible with the new Drill Fix PRO™ platform and feature higher adhesion wear resistance.
- Complementing another existing platform, Kennametal’s Mill 4™12KT, are new HD geometry inserts and fine pitch cutters that serve as performance boosters for highly interrupted cuts.
- KenShape™ MaPACS (brazed) and MaxPACS (Indexable) counte
rsinks deliver maximum performance for manual CFRP countersinking applications and are the perfect fit for aerospace industry customers focusing on rivet hole drilling in composite and stacked materials.
Contact Details
Related Glossary Terms
- coolant
coolant
Fluid that reduces temperature buildup at the tool/workpiece interface during machining. Normally takes the form of a liquid such as soluble or chemical mixtures (semisynthetic, synthetic) but can be pressurized air or other gas. Because of water’s ability to absorb great quantities of heat, it is widely used as a coolant and vehicle for various cutting compounds, with the water-to-compound ratio varying with the machining task. See cutting fluid; semisynthetic cutting fluid; soluble-oil cutting fluid; synthetic cutting fluid.
- countersinking
countersinking
Cutting a beveled edge at the entrance of a hole so a screw head sits flush with the workpiece surface.
- gang cutting ( milling)
gang cutting ( milling)
Machining with several cutters mounted on a single arbor, generally for simultaneous cutting.
- milling
milling
Machining operation in which metal or other material is removed by applying power to a rotating cutter. In vertical milling, the cutting tool is mounted vertically on the spindle. In horizontal milling, the cutting tool is mounted horizontally, either directly on the spindle or on an arbor. Horizontal milling is further broken down into conventional milling, where the cutter rotates opposite the direction of feed, or “up” into the workpiece; and climb milling, where the cutter rotates in the direction of feed, or “down” into the workpiece. Milling operations include plane or surface milling, endmilling, facemilling, angle milling, form milling and profiling.
- milling machine ( mill)
milling machine ( mill)
Runs endmills and arbor-mounted milling cutters. Features include a head with a spindle that drives the cutters; a column, knee and table that provide motion in the three Cartesian axes; and a base that supports the components and houses the cutting-fluid pump and reservoir. The work is mounted on the table and fed into the rotating cutter or endmill to accomplish the milling steps; vertical milling machines also feed endmills into the work by means of a spindle-mounted quill. Models range from small manual machines to big bed-type and duplex mills. All take one of three basic forms: vertical, horizontal or convertible horizontal/vertical. Vertical machines may be knee-type (the table is mounted on a knee that can be elevated) or bed-type (the table is securely supported and only moves horizontally). In general, horizontal machines are bigger and more powerful, while vertical machines are lighter but more versatile and easier to set up and operate.
- pitch
pitch
1. On a saw blade, the number of teeth per inch. 2. In threading, the number of threads per inch.
- wear resistance
wear resistance
Ability of the tool to withstand stresses that cause it to wear during cutting; an attribute linked to alloy composition, base material, thermal conditions, type of tooling and operation and other variables.
- wiper
wiper
Metal-removing edge on the face of a cutter that travels in a plane perpendicular to the axis. It is the edge that sweeps the machined surface. The flat should be as wide as the feed per revolution of the cutter. This allows any given insert to wipe the entire workpiece surface and impart a fine surface finish at a high feed rate.