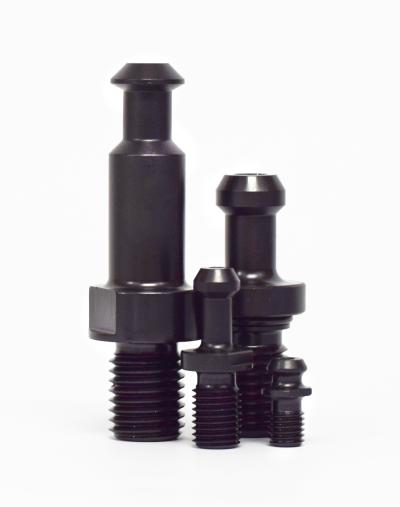
T.J. Davies Co., Inc., an industry leading manufacturer of retention knobs, can make custom retention knobs, pull bolts, and other workholding components and accessories to fit older, or obsolete machinery. All dimensions of knobs can be customized, including length, diameter, thickness of collars, dimensions between collar and knob end, thread size, and more. Additionally, customers can specify a coolant hole, taper style, and whether O-rings are required. Custom made retention knobs are sized to fit the machine tool and spindle or toolholder to maximize the toolholders performance and cutting tool life and extend the life of existing machine tool assets. A fill-in-the-blanks form is provided at https://tjdavies.com/quote-
All TJ Davies custom retention knobs are manufactured from American-made 8620 alloy steel which has a high tensile strength to withstand strong centrifugal force, high load force, high feed rate, and difficult to machine material. All knobs are machined in-house with single point threading to Imperial (Class 2A UNC) or Metric (Class G6) standards. After threading is completed, each component is heat treated to 58-62 HRC then treated with hot black oxide to military specifications for protection against corrosion. Each retention knob is magnetic particle tested and then pull tested to 2.5 times the pulling force of the drawbar it is designed for.
The use of 8620 ensures that the components will work harden over time, rather than becoming brittle as is the case with the use 9310 alloy steel. Single point threading ensures that the threads are balanced (lead-in/lead-out at 180 degrees) which is very difficult to achieve when rolling threads. Full depth is also attained for each thread. Because all machining is done with a single set-up, concentricity is achieved.
Each component is heat treated to a case depth of .020 to .030. No carb is applied to coolant through hole to ensure there is no shrinkage. Core hardness of 40HRC is standard. All retention knob surfaces (not just mating surfaces) have a precision finish of 32 RMA micro or better, ISO grade 6N. Certifications are maintained for each step and each batch to ensure traceability and quality control.
Overtightening can overly stress the retention knob, leading to premature failure, and can cause toolholder swelling and expansion. TJ Davies provides recommended torque guidelines with each retention knob shipped. Machine builder recommendations should always be used when available.
Sockets for the proper installation of retention knobs are available, individually or as a complete set of 4. All sockets and retention knobs are manufactured to exact specifications that exceed industry standards and are available through distributors nationwide.
Contact Details
Related Glossary Terms
- black oxide
black oxide
Black finish on a metal produced by immersing it in hot oxidizing salts or salt solutions.
- coolant
coolant
Fluid that reduces temperature buildup at the tool/workpiece interface during machining. Normally takes the form of a liquid such as soluble or chemical mixtures (semisynthetic, synthetic) but can be pressurized air or other gas. Because of water’s ability to absorb great quantities of heat, it is widely used as a coolant and vehicle for various cutting compounds, with the water-to-compound ratio varying with the machining task. See cutting fluid; semisynthetic cutting fluid; soluble-oil cutting fluid; synthetic cutting fluid.
- feed
feed
Rate of change of position of the tool as a whole, relative to the workpiece while cutting.
- hardness
hardness
Hardness is a measure of the resistance of a material to surface indentation or abrasion. There is no absolute scale for hardness. In order to express hardness quantitatively, each type of test has its own scale, which defines hardness. Indentation hardness obtained through static methods is measured by Brinell, Rockwell, Vickers and Knoop tests. Hardness without indentation is measured by a dynamic method, known as the Scleroscope test.
- quality assurance ( quality control)
quality assurance ( quality control)
Terms denoting a formal program for monitoring product quality. The denotations are the same, but QC typically connotes a more traditional postmachining inspection system, while QA implies a more comprehensive approach, with emphasis on “total quality,” broad quality principles, statistical process control and other statistical methods.
- tensile strength
tensile strength
In tensile testing, the ratio of maximum load to original cross-sectional area. Also called ultimate strength. Compare with yield strength.
- threading
threading
Process of both external (e.g., thread milling) and internal (e.g., tapping, thread milling) cutting, turning and rolling of threads into particular material. Standardized specifications are available to determine the desired results of the threading process. Numerous thread-series designations are written for specific applications. Threading often is performed on a lathe. Specifications such as thread height are critical in determining the strength of the threads. The material used is taken into consideration in determining the expected results of any particular application for that threaded piece. In external threading, a calculated depth is required as well as a particular angle to the cut. To perform internal threading, the exact diameter to bore the hole is critical before threading. The threads are distinguished from one another by the amount of tolerance and/or allowance that is specified. See turning.
- toolholder
toolholder
Secures a cutting tool during a machining operation. Basic types include block, cartridge, chuck, collet, fixed, modular, quick-change and rotating.