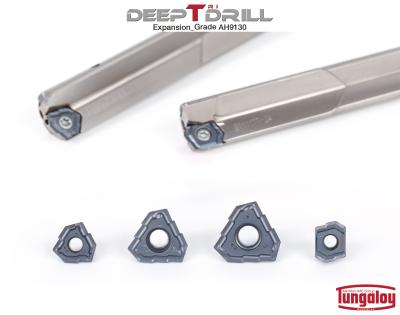
Tungaloy has added wear-resistant AH9130 insert grade to its DeepTri-Drill indexable insert gun drills.
DeepTri-Drill is a successful line of indexable gun drills that uses inserts with unique features. The drill allows increased penetration rate over conventional brazed gun drills, boosting productivity and application security during deep hole drilling applications.
DeepTri-Drill now offers wear-resistant AH9130 insert grade for its LOGT and TOHT inserts. AH9130 is the latest PVD technology specifically engineered for hole making applications. The grade consists of the latest PVD coating layer optimized for hole making applications combined with a dedicated carbide substrate and demonstrates superior wear resistance during deep drilling of steel, stainless steel, and cast iron, providing long and stable tool life.
LOGT inserts have two cutting edges, covering drill diameters ranging from 12.0 mm to 13.9 mm (.472″ to .547″). While TOHT inserts with three cutting edges come in six sizes and cover the tool diameter range from 14.0 mm to 28.0 mm (.551″ to 1.102″). Both insert styles have chip splitters on the cutting edge that break chips in small pieces for smooth and secure evacuation, eliminating drill breakage during deep hole machining.
The DeepTri-Drill series
Having pressed-to-form 3D chipbreakers on their rake face, the DeepTri-Drill inserts demonstrate effective chip control during deep hole drilling in a broad range of materials.
Unique chip splitters on the cutting edge securely break the chips into small pieces, which are smoothly evacuated with the help of the chipbreaker from the cutting point and out of the hole.
Thanks to indexable technology, DeepTri-Drill eliminates the need for reconditioning worn drills and also provides reduced downtime through its ability to change inserts while remaining in the machine spindle. In addition, the tool requires a minimal storage space, compared with traditional gun drills with brazed cutting edge, and streamlined inventory management.
The guide pads are allocated strategically on the drill body so that the drill can provide a maximum tool life and close hole tolerances. The guide pads are replaceable, allowing easy and secure replacements of worn guide pads.
Contact Details
Related Glossary Terms
- chipbreaker
chipbreaker
Groove or other tool geometry that breaks chips into small fragments as they come off the workpiece. Designed to prevent chips from becoming so long that they are difficult to control, catch in turning parts and cause safety problems.
- indexable insert
indexable insert
Replaceable tool that clamps into a tool body, drill, mill or other cutter body designed to accommodate inserts. Most inserts are made of cemented carbide. Often they are coated with a hard material. Other insert materials are ceramic, cermet, polycrystalline cubic boron nitride and polycrystalline diamond. The insert is used until dull, then indexed, or turned, to expose a fresh cutting edge. When the entire insert is dull, it is usually discarded. Some inserts can be resharpened.
- physical vapor deposition ( PVD)
physical vapor deposition ( PVD)
Tool-coating process performed at low temperature (500° C), compared to chemical vapor deposition (1,000° C). Employs electric field to generate necessary heat for depositing coating on a tool’s surface. See CVD, chemical vapor deposition.
- rake
rake
Angle of inclination between the face of the cutting tool and the workpiece. If the face of the tool lies in a plane through the axis of the workpiece, the tool is said to have a neutral, or zero, rake. If the inclination of the tool face makes the cutting edge more acute than when the rake angle is zero, the rake is positive. If the inclination of the tool face makes the cutting edge less acute or more blunt than when the rake angle is zero, the rake is negative.
- wear resistance
wear resistance
Ability of the tool to withstand stresses that cause it to wear during cutting; an attribute linked to alloy composition, base material, thermal conditions, type of tooling and operation and other variables.