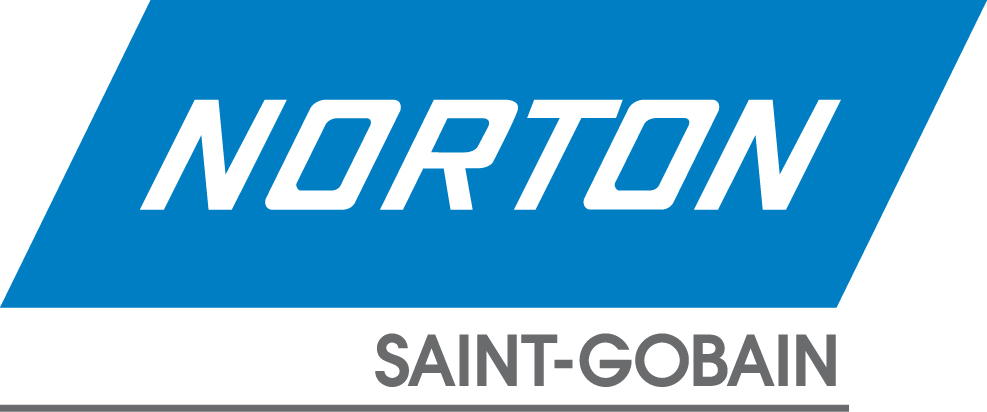
In connection with my feature article on abrasive machining for the May issue, I spoke with Steve Kendjelic, senior applications engineer for Norton/Saint-Gobain Abrasives, Worcester, Mass., about power gear honing. The process is used for ultrafinishing generated gear teeth and is generally performed on a honing machine. The hones are rubbed against the profile generated on the gear tooth.
Gear honing and gear lapping are the last finishing operations of a gear-generation process. Kendjelic pointed out that the Big Three automakers perform power gear honing, as well as automotive transmission manufacturers.
Grinding the gears after heat treatment can impart grinding lines, which causes transmission noise. As a result, he said manufacturers are hard finishing with honing tools after hobbing and heat treating gears to eliminate the grinding process and impart a crosshatch pattern for oil retention in the hardened workpiece and reduce transmission noise.
Tools with a higher concentration of ceramic grain than in the past are now applied when power gear honing to reduce cycle time by increasing the feed per revolution, Kendjelic added. Previously, there was a 30 percent ceramic content and now it’s up to 100 percent in some applications.
In addition, Kendjelic discussed generating grinding and said, “The grinding machine tool people want to have gears continued to be produced on their equipment but also take advantage of technology to go ahead and superfinish gears to compete with the power honing people.” Suitable wheels include conventional grinding wheels, and electroplated and vitrified CBN wheels.
One change to become more competitive when generating grinding is switching from a large-diameter wheel, such as a 16" one, to a smaller-diameter one to grind at a higher peripheral speed, he explained. The width of the new wheel, however, increased. Then end users added a second wheel to do polishing. The goal is to improve the surface finishing without having to reclamp the part.
Related Glossary Terms
- abrasive
abrasive
Substance used for grinding, honing, lapping, superfinishing and polishing. Examples include garnet, emery, corundum, silicon carbide, cubic boron nitride and diamond in various grit sizes.
- abrasive machining
abrasive machining
Various grinding, honing, lapping and polishing operations that utilize abrasive particles to impart new shapes, improve finishes and part stock by removing metal or other material.
- cubic boron nitride ( CBN)
cubic boron nitride ( CBN)
Crystal manufactured from boron nitride under high pressure and temperature. Used to cut hard-to-machine ferrous and nickel-base materials up to 70 HRC. Second hardest material after diamond. See superabrasive tools.
- feed
feed
Rate of change of position of the tool as a whole, relative to the workpiece while cutting.
- grinding
grinding
Machining operation in which material is removed from the workpiece by a powered abrasive wheel, stone, belt, paste, sheet, compound, slurry, etc. Takes various forms: surface grinding (creates flat and/or squared surfaces); cylindrical grinding (for external cylindrical and tapered shapes, fillets, undercuts, etc.); centerless grinding; chamfering; thread and form grinding; tool and cutter grinding; offhand grinding; lapping and polishing (grinding with extremely fine grits to create ultrasmooth surfaces); honing; and disc grinding.
- grinding machine
grinding machine
Powers a grinding wheel or other abrasive tool for the purpose of removing metal and finishing workpieces to close tolerances. Provides smooth, square, parallel and accurate workpiece surfaces. When ultrasmooth surfaces and finishes on the order of microns are required, lapping and honing machines (precision grinders that run abrasives with extremely fine, uniform grits) are used. In its “finishing” role, the grinder is perhaps the most widely used machine tool. Various styles are available: bench and pedestal grinders for sharpening lathe bits and drills; surface grinders for producing square, parallel, smooth and accurate parts; cylindrical and centerless grinders; center-hole grinders; form grinders; facemill and endmill grinders; gear-cutting grinders; jig grinders; abrasive belt (backstand, swing-frame, belt-roll) grinders; tool and cutter grinders for sharpening and resharpening cutting tools; carbide grinders; hand-held die grinders; and abrasive cutoff saws.
- lapping
lapping
Finishing operation in which a loose, fine-grain abrasive in a liquid medium abrades material. Extremely accurate process that corrects minor shape imperfections, refines surface finishes and produces a close fit between mating surfaces.
- polishing
polishing
Abrasive process that improves surface finish and blends contours. Abrasive particles attached to a flexible backing abrade the workpiece.