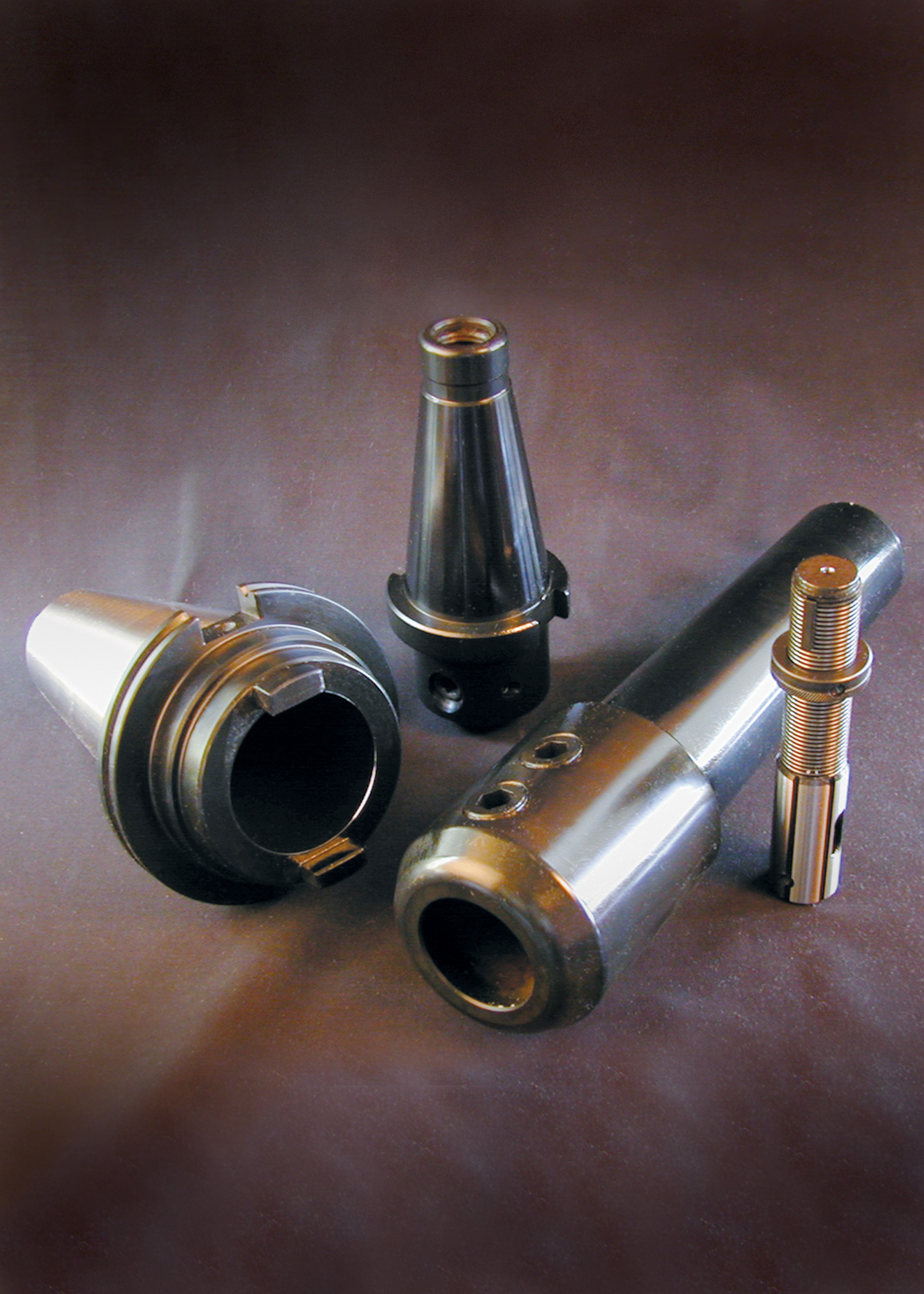
Article from Collis Toolholder Corp., Clinton, Iowa
For many machinists, the conversation begins, “If I could have this size tool with this attachment on it, we'd be able to …” With the variety of machine taper types, sizes, differences in the flanges, draw-in thread sizes and pull studs, finding the ideal toolholder for the job can be a difficult task.
Yet in many cases, machinists want to make adjustments in dimensions, quick-change tooling or other options to reduce set-up times and speed production of machined components. This can be as simple as extending the tool length so the path of travel to the workpiece is minimized to setting up all tools for quick changeouts.
Inevitably this leads to long, exhaustive searches of catalogs or online forums. Failing to find what they need, some machinists purchase “blanks” and grind them down to meet the precise requirements of their operation.
However, some manufacturers, particularly smaller, more nimble U.S.-based operations, are willing to create specialty toolholders.
“Many of the larger manufacturers don’t want to spend time setting up a machine just to create five pieces,” explains Paul Gassman of Collis Toolholder, a company that manufactures and distributes more than 4,500 SKUs of toolholders. “And it is not just one machine – it might take 14 setups to make one part.”
For Stephee Thee of Vallen Industrial Distribution, when companies call or email her for “specials” there are very few options available. “A lot of vendors come back with a ‘no-quote’ or an astronomical price.”
She says she has turned to Collis, who quotes at a reasonable price, for variations that include varying lengths and conversions, for example, a Morse taper either stepped or up reduced in size, a V-flange shank with a quick-change nose or an extended projection for deep-hole drilling and tapping.
According to Gassman, just about any toolholder can be produced based on special requirements or proprietary dimensions, in just about any combination of shank, collar and collet.
Furthermore, just about any system can be converted into a quick-tool-change format. Adjustable adapter and tap extensions are also available.
This can be a simple matter of mixing and matching options already in a catalogue. If an appropriate toolholder cannot be located, a replacement can be machined by those with the in-house capability utilizing CAD software that adjusts for varying projection lengths.
“You can basically combine any shank and holder together and extend the dimensions in any direction and our software program will recover all the dimensions on the tool so it isn't like drawing everything from scratch,” says Gassman.
Quality U.S.-based manufacturers also have more expertise achieving the precise tolerances for optimal fit and concentricity. By utilizing options with superior fit and better balance, more accurate work and finer surface finishes can be achieved while extending the life of the equipment itself.
For all its tapered toolholders, Collis is known for exceeding the industry “AT” standards for precise fit in the spindle. These standards are a specification of ANSI/ASME standard (ASME B5.50-2009) and indicate the tolerances that must be met in relation to the taper angle. Collis uses one-half the allowable tolerance of this standard.
For high-speed machining above 10,000 rpm, the toolholder must also be balanced more precisely or vibration can occur, leading to out-of-tolerance parts. For these reasons, machine tool spindles and machine tool parts from Collis are usually are specified with vibration levels of G2.5, whereas others might offer only G6.3.
Although the toolholders are custom manufactured, Gassman says this doesn’t have to mean long lead times.
“Machine operators don’t order a toolholder far in advance for a project. They are basically getting ready to run some parts and need the toolholder sooner, rather than later, so lead time is a factor,” adds Gassman, adding that Collis can deliver a custom machined toolholder in as little as 2 weeks.
A variety of adjustments can also be made that do not require a custom manufactured toolholder. This can include quick-tool-change tools, adjustable adapters and tap extenders for all taper types.
“With 4,500 options, there is a vast amount of tooling options without ever making it a special just by combining some of the standard options with existing holders,” says Gassman.
Modular, quick-change tooling systems provide a single interface for multiple types of machines. Collis offer a Rapid Switch line that is interchangeable with Universal’s Kwik Switch taper types.
Adjustable adapters and tap extensions can also increase the projection dimensions of a tool up to several inches, and are adjustable 1" to 2” depending on the diameter of the shank. These tools are extremely precise, with a shank tolerance of 0.0003”. With the industry standard bushing tolerance of 0.0005” on the inside bore and outside surface, for 0.001” total clearance. This minimizes any possible vibration or fretting.
In some cases, a tool for an older piece of equipment might exist but is just difficult to find.
Collis is still providing tools for machining operations that have been around for a long time and still utilize drill presses, manual milling machines, and automotive transfer line equipment along with newer CNC machines.
When this is the case, the toolholder may be available from a provider that offers a broad catalogue of options. Collis, for example, continues to offer hard-to-find toolholders for automotive transfer lines and Rapid Switch milling machines.
Unique options for drill presses are also available, including “Magic Chucks” that provide a way to turn a single spindle machine into a multiple-operation machine.
Related Glossary Terms
- bushing
bushing
Cylindrical sleeve, typically made from high-grade tool steel, inserted into a jig fixture to guide cutting tools. There are three main types: renewable, used in liners that in turn are installed in the jig; press-fit, installed directly in the jig for short production runs; and liner (or master), installed permanently in a jig to receive renewable bushing.
- clearance
clearance
Space provided behind a tool’s land or relief to prevent rubbing and subsequent premature deterioration of the tool. See land; relief.
- collet
collet
Flexible-sided device that secures a tool or workpiece. Similar in function to a chuck, but can accommodate only a narrow size range. Typically provides greater gripping force and precision than a chuck. See chuck.
- computer numerical control ( CNC)
computer numerical control ( CNC)
Microprocessor-based controller dedicated to a machine tool that permits the creation or modification of parts. Programmed numerical control activates the machine’s servos and spindle drives and controls the various machining operations. See DNC, direct numerical control; NC, numerical control.
- computer-aided design ( CAD)
computer-aided design ( CAD)
Product-design functions performed with the help of computers and special software.
- gang cutting ( milling)
gang cutting ( milling)
Machining with several cutters mounted on a single arbor, generally for simultaneous cutting.
- milling
milling
Machining operation in which metal or other material is removed by applying power to a rotating cutter. In vertical milling, the cutting tool is mounted vertically on the spindle. In horizontal milling, the cutting tool is mounted horizontally, either directly on the spindle or on an arbor. Horizontal milling is further broken down into conventional milling, where the cutter rotates opposite the direction of feed, or “up” into the workpiece; and climb milling, where the cutter rotates in the direction of feed, or “down” into the workpiece. Milling operations include plane or surface milling, endmilling, facemilling, angle milling, form milling and profiling.
- shank
shank
Main body of a tool; the portion of a drill or similar end-held tool that fits into a collet, chuck or similar mounting device.
- tap
tap
Cylindrical tool that cuts internal threads and has flutes to remove chips and carry tapping fluid to the point of cut. Normally used on a drill press or tapping machine but also may be operated manually. See tapping.
- tapping
tapping
Machining operation in which a tap, with teeth on its periphery, cuts internal threads in a predrilled hole having a smaller diameter than the tap diameter. Threads are formed by a combined rotary and axial-relative motion between tap and workpiece. See tap.
- tolerance
tolerance
Minimum and maximum amount a workpiece dimension is allowed to vary from a set standard and still be acceptable.
- toolholder
toolholder
Secures a cutting tool during a machining operation. Basic types include block, cartridge, chuck, collet, fixed, modular, quick-change and rotating.