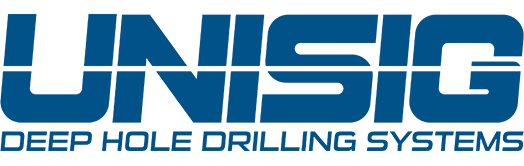
Books have been written on how to produce deep holes using milling machines or lathes, but trying to drill deep holes with depth-to-diameter ratios greater than 15-1 (D-d) using standard machining centers often leads to frustration, costly scrap and poor use of shop resources. And when it comes to those jobs with D:d ratios of 20:1, 100:1, or even 200:1, that frustration is magnified because the operation requires specialized equipment and knowledge that even the most seasoned mill or lathe operators often lack. With deep holes becoming a prerequisite for parts in multiple industries, job shops and suppliers need to supplement their existing experience and capabilities with the expertise of deep hole drilling specialists.
The starting point for these demanding hole-making applications is preparation and consultation with a deep hole drilling equipment supplier. This supplier must have a thorough understanding of the engineering that’s necessary to efficiently produce the tolerances, hole depth, concentricity and surface finish required. In addition, the supplier must be a willing partner, one that can guide a shop’s operators as they develop their own deep hole drilling expertise.
At UNISIG, we begin all deep hole drilling projects by asking the difficult questions that allow us to truly understand what the customer is looking for. The answers enable us to determine the proper deep hole drilling solution and also identify its degree of difficulty. This, in turn, dictates how to manage project expectations.
We first determine whether BTA, standard gundrill or newer, indexable gundrill tooling is required. This can be based on a number of factors, such as the project’s D:d ratio, whether the holes are on- or off-center, the desired hole tolerance, and the priority of cycle time versus accuracy. This decision will indicate the appropriate machine for the job. Additionally, workholding and fixturing must be factored into the decision, along with required production levels.
If accuracy is paramount – which is often the case for medical and oil tool applications – counter-rotating the workpiece in one direction and the tool in the other provides the most accurate hole and highest level of concentricity. Rotating only the workpiece with a stationary tool offers the next best accuracy for round parts with on-center holes. Rotating only the tool as it enters a stationary part is typically used for non-symmetrical components or round parts with off-center holes. As a byproduct, this method will have more drift than the other options. For some applications, however, this makes sense, as drilling speed may be more important than accuracy.
Some deep hole drilling projects require equipment modifications that increase a machine’s capabilities to meet specific application needs. These system changes could include the addition of a drop bed that allows for workpiece swing, which is required to rotate a part for sufficient drill access. Alternately, multiple spindles may be incorporated to increase through put. And automatic loading and/or unloading systems – like robotics, servo-driven gantries, magazine loaders or internal walking beams – may be added to improve production and relieve operator time to add value to other processes.
Answers to questions about a deep hole drilling application may also be used to select and modify a system to incorporate state-of-the-art technologies. A properly chosen gundrill, for example, can transform a challenging job with an extreme D:d ratio into an easily handled, profitable venture for veteran manufacturers or job shops embarking on their first deep hole drilling endeavor.
No successful deep hole drilling project is complete without on-site and ongoing training. To achieve success, mill and/or lathe operators must quickly learn and understand deep hole drilling processes. This education, together with the knowledge and experience of deep hole drilling system providers such as UNISIG, ensures a shop’s future projects are successful and profitable.
Contact Details
Related Glossary Terms
- centers
centers
Cone-shaped pins that support a workpiece by one or two ends during machining. The centers fit into holes drilled in the workpiece ends. Centers that turn with the workpiece are called “live” centers; those that do not are called “dead” centers.
- gang cutting ( milling)
gang cutting ( milling)
Machining with several cutters mounted on a single arbor, generally for simultaneous cutting.
- gundrill
gundrill
Self-guided drill for producing deep holes with good accuracy and fine surface finish. Has coolant passages that deliver coolant to the tool/workpiece interface at high pressure.
- lathe
lathe
Turning machine capable of sawing, milling, grinding, gear-cutting, drilling, reaming, boring, threading, facing, chamfering, grooving, knurling, spinning, parting, necking, taper-cutting, and cam- and eccentric-cutting, as well as step- and straight-turning. Comes in a variety of forms, ranging from manual to semiautomatic to fully automatic, with major types being engine lathes, turning and contouring lathes, turret lathes and numerical-control lathes. The engine lathe consists of a headstock and spindle, tailstock, bed, carriage (complete with apron) and cross slides. Features include gear- (speed) and feed-selector levers, toolpost, compound rest, lead screw and reversing lead screw, threading dial and rapid-traverse lever. Special lathe types include through-the-spindle, camshaft and crankshaft, brake drum and rotor, spinning and gun-barrel machines. Toolroom and bench lathes are used for precision work; the former for tool-and-die work and similar tasks, the latter for small workpieces (instruments, watches), normally without a power feed. Models are typically designated according to their “swing,” or the largest-diameter workpiece that can be rotated; bed length, or the distance between centers; and horsepower generated. See turning machine.
- milling
milling
Machining operation in which metal or other material is removed by applying power to a rotating cutter. In vertical milling, the cutting tool is mounted vertically on the spindle. In horizontal milling, the cutting tool is mounted horizontally, either directly on the spindle or on an arbor. Horizontal milling is further broken down into conventional milling, where the cutter rotates opposite the direction of feed, or “up” into the workpiece; and climb milling, where the cutter rotates in the direction of feed, or “down” into the workpiece. Milling operations include plane or surface milling, endmilling, facemilling, angle milling, form milling and profiling.
- milling machine ( mill)
milling machine ( mill)
Runs endmills and arbor-mounted milling cutters. Features include a head with a spindle that drives the cutters; a column, knee and table that provide motion in the three Cartesian axes; and a base that supports the components and houses the cutting-fluid pump and reservoir. The work is mounted on the table and fed into the rotating cutter or endmill to accomplish the milling steps; vertical milling machines also feed endmills into the work by means of a spindle-mounted quill. Models range from small manual machines to big bed-type and duplex mills. All take one of three basic forms: vertical, horizontal or convertible horizontal/vertical. Vertical machines may be knee-type (the table is mounted on a knee that can be elevated) or bed-type (the table is securely supported and only moves horizontally). In general, horizontal machines are bigger and more powerful, while vertical machines are lighter but more versatile and easier to set up and operate.
- robotics
robotics
Discipline involving self-actuating and self-operating devices. Robots frequently imitate human capabilities, including the ability to manipulate physical objects while evaluating and reacting appropriately to various stimuli. See industrial robot; robot.
- tolerance
tolerance
Minimum and maximum amount a workpiece dimension is allowed to vary from a set standard and still be acceptable.