Dear Doc: I grind gears and am thinking of building a thermal model to predict grinding temperatures. Are models accurate? Is it worth doing?
The Doc replies: A good thermal model can help you choose grinding parameters that minimize both cycle time and burn risk. However, you must keep in mind the words of mathematician George E.P. Box (1919-2013): “All models are wrong, but some are useful.” The trick is to make your model less wrong and then know how to make it useful. It’s not easy.
Most models use the Jaeger equation of an infinite moving heat source (see the figure) to predict the maximum temperature on the surface of a workpiece. It’s then a matter of figuring out less wrong input parameters: What is the grinding power? How much of it comes from chip formation, and how much comes from rubbing? What fraction of chip formation heat goes into the workpiece? What fraction of the rubbing heat goes into the workpiece? How much heat goes into the coolant? (There is a lot in creep feed and very little in cylindrical outside diameter.) How much heat goes into the grit? (Aluminum oxide grits suck up very little heat while diamond and CBN grits suck up a lot.) How much is the wheel deflecting at the point of contact? (Resin-bonded wheels deflect a lot while vitrified-bonded wheels deflect only a little.) Under what conditions is the model accurate? (It is more accurate in cylindrical OD and less accurate in creep feed.)
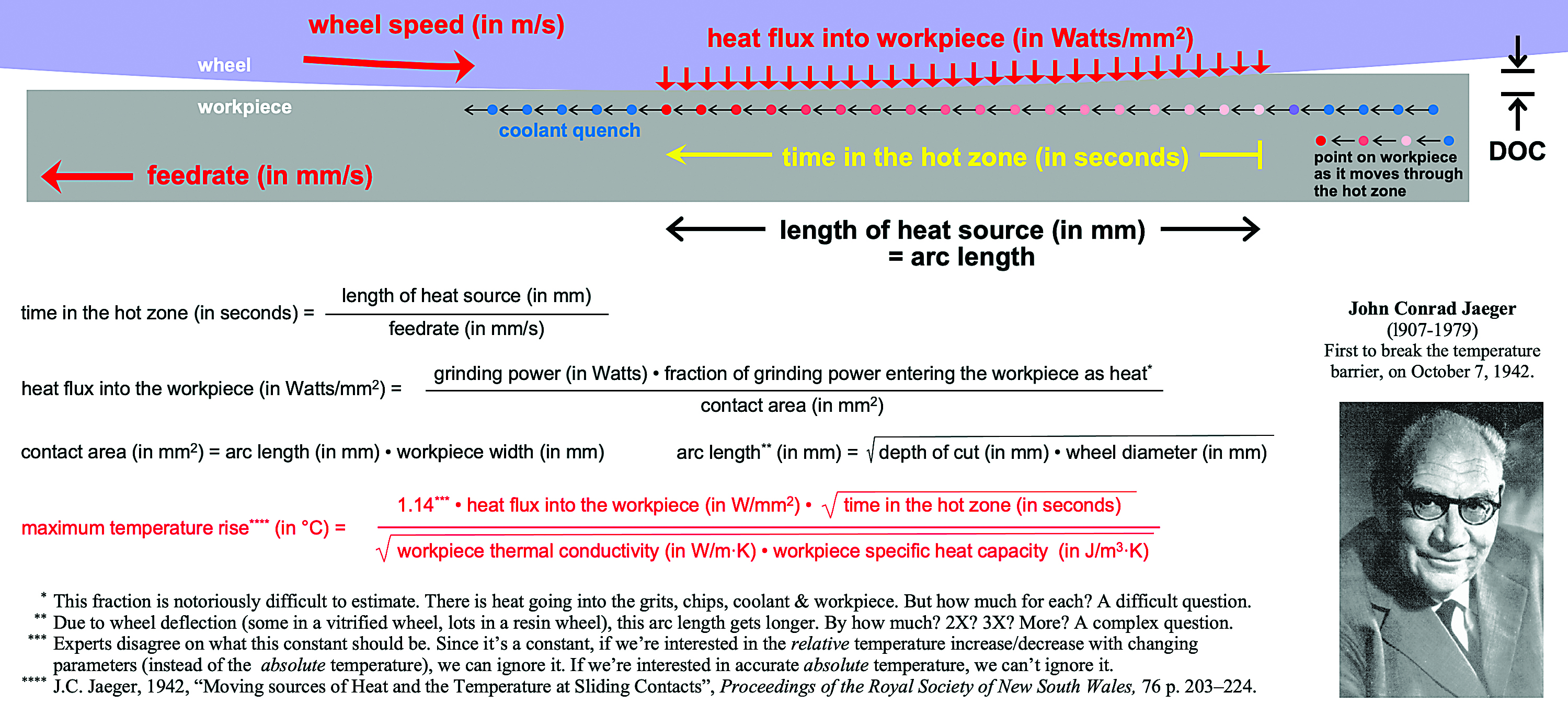
Grinding experts disagree vehemently on how to deal with each of these inputs. At grinding conferences, heated debates develop about thermal models. Pride runs rampant, tempers flare, harsh words are spoken, fights break out, and lifelong enemies are made. The result is better thermal models.
Building a less wrong thermal model is not easy. And the people whose thermal models I respect are super-humble about them. These experts know the limitations. Beware of people who tell you they have a very accurate model. If somebody tells you that his or her grinding thermal model is very accurate, the grinding thermal model is not accurate.
I have a model. I’ve invested probably a year of my life into developing it. Do I trust it? The answer is the always popular “It depends.” For numerous reasons related to the basic Jaeger equation and the reliability of predicting its inputs, I trust my model more for cylindrical grinding and less for creep feed grinding; more when grinding with flat wheels and less when grinding with wheels with forms; much more when I’ve actually measured grinding power and much less when I’m estimating that power based on dressing conditions. This is true for pretty much all temperature models, not just mine.
Most importantly, I trust my model far more when predicting relative temperature (how different parameters increase or decrease temperature) than when predicting absolute temperature. For example, if my model gives a temperature of 480 degrees Celsius (896 Fahrenheit) for parameter Set A and 320 C (608 F) for parameter Set B, can I be confident that the temperatures will indeed be 480 C and 320 C? No. Can I be confident that parameter Set B will give significantly lower temperatures than Set A? Yes.
My colleagues and I at the International Grinding Institute built two rather sophisticated thermal models of camshaft grinding and crankshaft grinding for a large Scandinavian diesel truck manufacturer. We measured grinding power under different aggressiveness values, which is always required for a decent prediction. We then tested it by purposely burning parts to various degrees to induce thermal damage and then comparing our predicted temperatures with the level of thermal damage given in the manufacturer’s in-process Barkhausen thermal damage QC system.
Did it work? Yes, beautifully. We used the model to reduce the manufacturer’s cycle time by 25% and reduce workpiece temperature to a safe, no-burn level. Five years later, the company still uses these parameters. The whole project probably took a total of 2,000 man-hours. That’s no small investment. But for a company grinding with numerous machines on numerous shifts — and spending millions of dollars a year on labor — a 25% reduction in cycle time is no small return on investment.
Whatever you do, be prepared to put time into it. And then know its limitations. If you’re willing to do that, send me an email, and I’ll tell you which books and papers are useful for getting started.
Related Glossary Terms
- burning
burning
Rotary tool that removes hard or soft materials similar to a rotary file. A bur’s teeth, or flutes, have a negative rake.
- cubic boron nitride ( CBN)
cubic boron nitride ( CBN)
Crystal manufactured from boron nitride under high pressure and temperature. Used to cut hard-to-machine ferrous and nickel-base materials up to 70 HRC. Second hardest material after diamond. See superabrasive tools.
- cylindrical grinding
cylindrical grinding
Grinding operation in which the workpiece is rotated around a fixed axis while the grinding wheel is fed into the outside surface in controlled relation to the axis of rotation. The workpiece is usually cylindrical, but it may be tapered or curvilinear in profile. See centerless grinding; grinding.
- dressing
dressing
Removal of undesirable materials from “loaded” grinding wheels using a single- or multi-point diamond or other tool. The process also exposes unused, sharp abrasive points. See loading; truing.
- feed
feed
Rate of change of position of the tool as a whole, relative to the workpiece while cutting.
- flat ( screw flat)
flat ( screw flat)
Flat surface machined into the shank of a cutting tool for enhanced holding of the tool.
- grinding
grinding
Machining operation in which material is removed from the workpiece by a powered abrasive wheel, stone, belt, paste, sheet, compound, slurry, etc. Takes various forms: surface grinding (creates flat and/or squared surfaces); cylindrical grinding (for external cylindrical and tapered shapes, fillets, undercuts, etc.); centerless grinding; chamfering; thread and form grinding; tool and cutter grinding; offhand grinding; lapping and polishing (grinding with extremely fine grits to create ultrasmooth surfaces); honing; and disc grinding.
- outer diameter ( OD)
outer diameter ( OD)
Dimension that defines the exterior diameter of a cylindrical or round part. See ID, inner diameter.