Imagine building a ship in a bottle, but instead of using a preexisting bottle, you build the ship along with the bottle while machining the ship’s and bottle’s surfaces as you go.
That’s an analogy Gregory Hyatt uses to describe hybrid machining, the combination of additive and subtractive manufacturing. “Of course, an additive machine could build the ship in the bottle but then you couldn’t take it to a machining center or lathe afterward to machine those features because the features are now trapped inside the container,” said the senior vice president and chief technology officer for DMG Mori USA, Hoffman Estates, Ill.
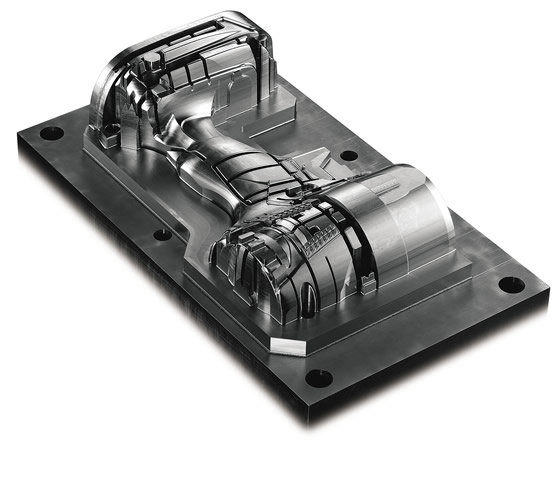
Courtesy of MC Machinery Systems
An example of a mold produced on Matsuura’s Lumex Avance-25 hybrid machine.
To perform hybrid machining, DMG Mori offers the Lasertec 65 3D, which integrates laser-deposition welding into a 5-axis milling machine and has a work envelope that’s 500mm (19.685 ") in diameter by 360mm (14.173 ") long. In addition, the company plans to start shipping the Lasertec 4300 3D this year, which integrates the same additive technology into a mill/turn machine that can accept a workpiece up to 660mm (25.984 ") in diameter by 1,500mm (59.055 ") long.
Hyatt explained that rather than laser sintering a portion of the metal powder on a base plate, the company’s laser deposition process fully melts the powder metal alloy as it is sprayed into the focal point of the laser, which is focused on the workpiece, or substrate, surface. “The focal point of the powder and the laser are concentric, and the laser melts the powder,” he added. “The substrate is also melted to a shallow depth, so you have full bonding of the powder with the substrate.”
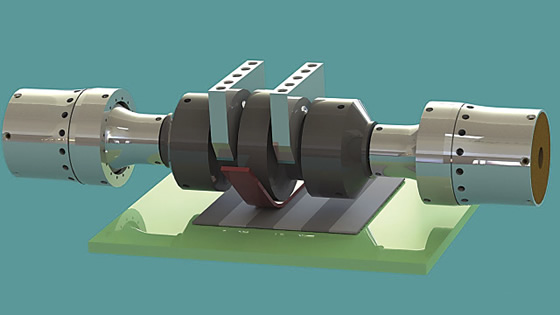
Courtesy of Fabrisonic
Fabrisonic’s ultrasonic additive manufacturing technology bonds layers of metal foil using a welding head.
Although the Lasertec can print a part from scratch on a base plate and machine the required features during the build process, Hyatt said it can also start with a preexisting component, forging, casting or bar stock, and then build features. In some cases, the amount of metal powder deposited is 5 percent of what would be required to make the entire part from scratch.
More than One Way to Build a Ship
MC Machinery Systems Inc. also offers a hybrid machine tool: the Lumex Avance-25 from Japan-based Matsuura. Although the additive portion is called direct metal laser sintering, Greg Langenhorst, technical marketing manager for the Wood Dale, Ill., distributor, said that description is a misnomer. “We’re actually laser-melting material together.”
An example of sintering, on the other hand, is the production of tungsten carbide, where the various elements are mixed, heated and put under pressure to bond together. “That’s an honest-to-God, true sintering process,” Langenhorst emphasized.
Semantics aside, the DMLS process starts with a base plate, or ground-flat piece of hot-rolled steel, bolted to the machine table, Langenhorst explained. A squeezing bar deposits and squeezes the metal powder on the base plate to a thickness of 50µm (0.0019 "), the laser melts the powder based on the part’s NC program, after which the table drops 50µm and another layer is squeezed and melted on top of the previous layer.
Typically, after 10 layers the machine performs rough and semifinish milling at up to 45,000 rpm, Langenhorst said, noting the number of layers sometimes varies. The semifinishing tool leaves about 0.0015 " (0.038mm) per side oversize. After the next 10 layers are deposited and melted, they are roughed and semifinished, and the previous 10 layers are then finished with a shank-relieved tool. “The reasoning for that is every time you start a new set of layers, it has a tendency to shrink the edge a little bit,” he said, “so we eliminate the witness line for every set of 10 layers. Finish milling is always one step below what you just created.”
Similar to other hybrid machining processes, DMLS enables creating conformal internal cooling channels and deep ribs as thin as 0.028 " (0.711mm) without having to design electrodes and apply them via sinker EDMing. It also eliminates mold die splitting, which means that a multiple-piece assembly can be built as one piece, saving a significant amount of assembly time and reducing part weight and the complexity of building multiple pieces, according to Langenhorst. EDMing can still come into play with hybrid machining, but in the form of wire EDMing to remove the completed part from the base plate.
A Sound Solution
A hot melt works well when building P/M parts, but that approach isn’t suitable for some applications. Fabrisonic LLC offers an alternative method of 3D printing that doesn’t melt the metal and incorporates it into a milling machine. The company scaled up ultrasonic welding technology, which the electronics industry has long used to weld dissimilar metals on a microscale level, to produce parts in a machine with a work envelope up to 6 '×6 ' (1.829m × 1.828m), said Mark Norfolk, president of the 3-year-old, Columbus, Ohio, company (see photos on pages 54 and 60).
Fabrisonic’s ultrasonic additive manufacturing (UAM) technology bonds layers of metal foil measuring 0.006 " (0.152mm) thick at a rate of 15 to 20 cu. in. (381mm to 508mm) per hour using a welding head, Norfolk explained. Oxide layers prevent metals from sticking outside of a vacuum, so UAM rubs off the oxide layer by vibrating the foil with sound at 20 kHz, mating virgin metal with virgin metal—even dissimilar ones—to achieve specific engineering properties.
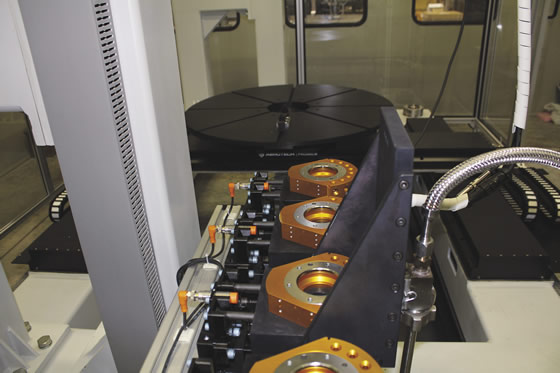
Courtesy of Flexible Robotic Environment
The toolchanger on FRE’s 6-axis VDK6000 robotic work center has four stations for additive manufacturing tools. The cell also provides subtractive capabilities, including milling, drilling, grinding and polishing.
“If you were to take titanium and aluminum and melt and resolidify them, what you would end up with is a brittle intermetallic, almost like glass,” he said. “With our process, because we’re not melting, we can make a solid-state metallurgical bond at that interface without getting that intermetallic.”
The process isn’t a completely cold one, with temperatures from 200° to 250° F (93.3° to 121.1° C), as well as a down force of about 1,000 lbs. (454 kg) required to create a bond, but it’s cool enough to avoid changing the material’s metallurgy or grain structure and to enable embedding electronics in a part, Norfolk noted. However, the force exerted by the welding head creates problems with overhang features where there’s no support. “Typically, we overcome those with special endmills that have an undercut to them, playing tricks like that using the CNC machining side to get undercuts as opposed to printing the undercuts.”
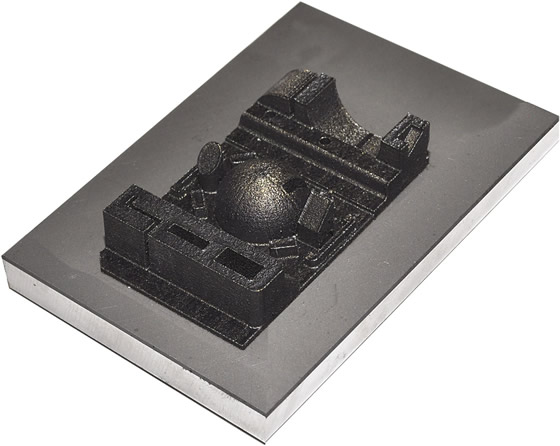
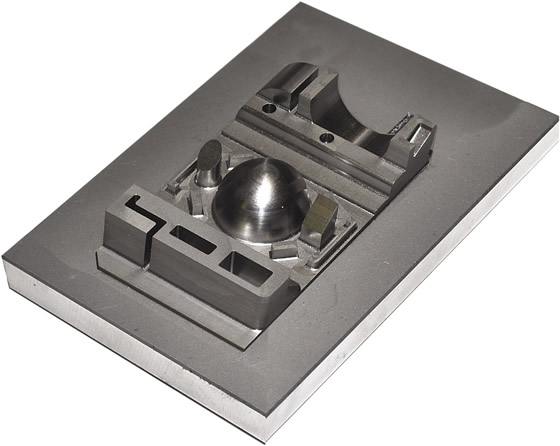
Courtesy of MC Machinery Systems
An example of a laser-sintered part produced on the Lumex Avance-25 hybrid machine and one that was sintered and machined.
Norfolk pointed out that the technology is also targeted at producing thermal-management components, such as a heat exchanger for a server farm. “For heat exchangers, we can make it partially copper for right where the heat sources are and part of the structure could be aluminum for weight savings or steel for mounting,” he said. “Most of the time the parts we are building are parts that you couldn’t make any other way.”
In addition to selling hybrid machines, the company makes parts for customers. “We’ve been growing by double digits every year,” Norfolk said.
Flexible Motion
“Like Lego blocks for real,” is how Dr. Vojislav Kalanovic, president of Flexible Robotic Environment and a professor of mechanical engineering at South Dakota School of Mines and Technology, describes how FRE’s VDK6000 hybrid robotic work center distributes its degrees of freedom and space to suit a specific application.
The standard system comes with six degrees of freedom to build complex parts and synchronously manipulates an end effector in 3D space to achieve full orientation and positioning of the head with respect to the workpiece, according to the Rapid City, S.D., company (See photo on pages 56-57).
Kalanovic added that the robotic work cell is scalable up or down, and users on a budget can start with only three degrees of freedom, for example, and add additional degrees as needed at a later date. In addition, a cell with six degrees of freedom can be configured with an additional redundant axis. “Our specialty is motion,” he emphasized.
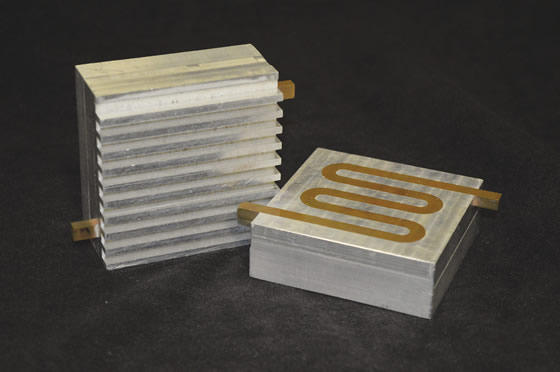
Courtesy of Fabrisonic
Because it doesn’t melt metal, Fabrisonic’s ultrasonic additive manufacturing enables users to embed electronics in a part.
The work cell has a toolchanger with four stations for additive manufacturing processes, such as plasma welding, cold spraying or direct metal laser deposition, and can be expanded to eight, Kalanovic noted. “You might not be able to use certain technologies in sequence for process-related reasons.”
On the subtractive manufacturing side, the VDK6000 can perform milling, drilling, grinding and polishing, as well as ultrasonic inspection part verification after processing. “You can combine processes and mimic a mini factory that will help you save a great deal of time,” he said. “Out of one fixturing you can perform a series of operations that normally take various kinds of machines to complete.”
Kalanovic estimates payback for the work cell, which can cost from $600,000 to $1.3 million, is 12 to 14 months. The overall workspace is 1.2m × 1.2m × 0.9m (3.94 '×3.94 '×2.95 ') and, in addition to building parts, can accept parts weighing up to 80 kg (176.4 lbs.) for repair. The cell’s footprint is about 4m × 5m × 4.5m (13.12 '×16.40 '×14.76 ').
Material Matters
In addition to understanding the build process, knowledge of the materials required for additive manufacturing is also critical to control costs, ensure parts function as designed and possibly protect life and limb.
MC Machinery’s Langenhorst explained that with the Matsuura hybrid process, only the material for making the part is consumed and the unused powder from the build chamber, which measures 10 "×10 "×7 " (254mm × 254mm × 177.8mm), is recycled. The savings from recycling quickly add up because a typical steel powder equivalent to H-13 costs about $430 per kilogram, in part because the particles are small—20µm to 45µm—to optimize surface finish.
The high cost generally makes it impractical for the machine to produce parts comprised of multiple materials because one powder would mix with another in the build chamber. This contamination prevents powder from being reused.
But without a grain structure like a piece of solid steel, the powder won’t warp when heat treated and evenly and predictably shrinks 0.08 to 0.1 percent, Langenhorst noted. “So you add that much extra material into your build program.”
Different powder types, however, require different production parameters. “If you don’t use a hot-enough laser beam or if you try and run it too fast, you don’t get the right melt density,” Langenhorst said. “These are things you have to work up for each powder type.”
Some metal powders require more than just melting at the proper parameters. Flammable powders, such as titanium and aluminum, require a facility to be ventilated and certified to even bring the powder inside, according to Langenhorst. “You basically must have a Class H structure, which is equivalent to what a company that builds fireworks would have.”
In addition, titanium powder, for example, can never be exposed to oxygen, requiring the entire handling process—from packaging until part completion in the Lumex Avance-25 machine—to take place in a 100 percent argon environment, Langenhorst explained. This is because as soon as titanium powder contacts air or water, the powder starts sucking the oxygen out of the air or water, leaving highly explosive hydrogen gas.
Even the vacuum cleaner to clean the machine has to be a specific type of wet-based system. “We just bought one for our machine here at a cost of about $8,000,” he said, noting MC Machinery has yet to produce any titanium sample parts, but Matsuura has.
Melting a powder with a larger particle size changes handling and recycling characteristics. DMG Mori’s Hyatt noted the LaserTec technology uses powders with particles from 50µm to 200µm, which reduces the cost compared to powders with smaller particles and makes the more-flammable ones less likely to ignite and explode. “There are still special precautions required for magnesium, titanium, aluminum and any of the more reactive metals,” he said, “but those concerns are not as severe as with the smaller particles.”
Because the cost per pound for the powder version of an exotic alloy is only slightly more than bars or plates, LaserTec machines can economically produce multimaterial parts, according to Hyatt, who added that the price penalty for less-exotic alloys is greater. Typically, only 15 to 20 percent of the powder is lost during a build cycle, and recycling is not an option. “There is just no economic justification for the cost and effort to filter and clean the powder,” he said.
Being able to build on an existing casting or forging also reduces the amount of powder consumed and, therefore, the cost. According to Hyatt, this allows the technology to be suitable for at least moderate-volume production. It also adds value for rapid prototyping, where the objective is not production volume but getting new products to market more quickly by accelerating the iterative process of refining prototypes. “With the hybrid machine, we can reduce that time from art to part dramatically.” CTE
![]() |
About the Author |
Contributors
Carr Lane Manufacturing Co.
(314) 647-6200
www.carrlane.com
DMG Mori USA
(847) 593-5400
www.us.dmgmori.com
Fabrisonic LLC
(614) 688-5197
www.fabrisonic.com
Flexible Robotic Environment
(605) 791-2202
www.fresystems.com
MC Machinery Systems Inc.
(630) 616-5920
www.mcmachinery.com
Related Glossary Terms
- alloys
alloys
Substances having metallic properties and being composed of two or more chemical elements of which at least one is a metal.
- computer numerical control ( CNC)
computer numerical control ( CNC)
Microprocessor-based controller dedicated to a machine tool that permits the creation or modification of parts. Programmed numerical control activates the machine’s servos and spindle drives and controls the various machining operations. See DNC, direct numerical control; NC, numerical control.
- degrees of freedom
degrees of freedom
Number of axes along which a robot, and thus the object it is holding, can be manipulated. Most robots are capable of maneuvering along the three basic Cartesian axes (X, Y, Z). More sophisticated models may move in six or more axes. See axis.
- gang cutting ( milling)
gang cutting ( milling)
Machining with several cutters mounted on a single arbor, generally for simultaneous cutting.
- grinding
grinding
Machining operation in which material is removed from the workpiece by a powered abrasive wheel, stone, belt, paste, sheet, compound, slurry, etc. Takes various forms: surface grinding (creates flat and/or squared surfaces); cylindrical grinding (for external cylindrical and tapered shapes, fillets, undercuts, etc.); centerless grinding; chamfering; thread and form grinding; tool and cutter grinding; offhand grinding; lapping and polishing (grinding with extremely fine grits to create ultrasmooth surfaces); honing; and disc grinding.
- lapping compound( powder)
lapping compound( powder)
Light, abrasive material used for finishing a surface.
- lathe
lathe
Turning machine capable of sawing, milling, grinding, gear-cutting, drilling, reaming, boring, threading, facing, chamfering, grooving, knurling, spinning, parting, necking, taper-cutting, and cam- and eccentric-cutting, as well as step- and straight-turning. Comes in a variety of forms, ranging from manual to semiautomatic to fully automatic, with major types being engine lathes, turning and contouring lathes, turret lathes and numerical-control lathes. The engine lathe consists of a headstock and spindle, tailstock, bed, carriage (complete with apron) and cross slides. Features include gear- (speed) and feed-selector levers, toolpost, compound rest, lead screw and reversing lead screw, threading dial and rapid-traverse lever. Special lathe types include through-the-spindle, camshaft and crankshaft, brake drum and rotor, spinning and gun-barrel machines. Toolroom and bench lathes are used for precision work; the former for tool-and-die work and similar tasks, the latter for small workpieces (instruments, watches), normally without a power feed. Models are typically designated according to their “swing,” or the largest-diameter workpiece that can be rotated; bed length, or the distance between centers; and horsepower generated. See turning machine.
- machining center
machining center
CNC machine tool capable of drilling, reaming, tapping, milling and boring. Normally comes with an automatic toolchanger. See automatic toolchanger.
- milling
milling
Machining operation in which metal or other material is removed by applying power to a rotating cutter. In vertical milling, the cutting tool is mounted vertically on the spindle. In horizontal milling, the cutting tool is mounted horizontally, either directly on the spindle or on an arbor. Horizontal milling is further broken down into conventional milling, where the cutter rotates opposite the direction of feed, or “up” into the workpiece; and climb milling, where the cutter rotates in the direction of feed, or “down” into the workpiece. Milling operations include plane or surface milling, endmilling, facemilling, angle milling, form milling and profiling.
- milling machine ( mill)
milling machine ( mill)
Runs endmills and arbor-mounted milling cutters. Features include a head with a spindle that drives the cutters; a column, knee and table that provide motion in the three Cartesian axes; and a base that supports the components and houses the cutting-fluid pump and reservoir. The work is mounted on the table and fed into the rotating cutter or endmill to accomplish the milling steps; vertical milling machines also feed endmills into the work by means of a spindle-mounted quill. Models range from small manual machines to big bed-type and duplex mills. All take one of three basic forms: vertical, horizontal or convertible horizontal/vertical. Vertical machines may be knee-type (the table is mounted on a knee that can be elevated) or bed-type (the table is securely supported and only moves horizontally). In general, horizontal machines are bigger and more powerful, while vertical machines are lighter but more versatile and easier to set up and operate.
- numerical control ( NC)
numerical control ( NC)
Any controlled equipment that allows an operator to program its movement by entering a series of coded numbers and symbols. See CNC, computer numerical control; DNC, direct numerical control.
- polishing
polishing
Abrasive process that improves surface finish and blends contours. Abrasive particles attached to a flexible backing abrade the workpiece.
- sintering
sintering
Bonding of adjacent surfaces in a mass of particles by molecular or atomic attraction on heating at high temperatures below the melting temperature of any constituent in the material. Sintering strengthens and increases the density of a powder mass and recrystallizes powder metals.
- toolchanger
toolchanger
Carriage or drum attached to a machining center that holds tools until needed; when a tool is needed, the toolchanger inserts the tool into the machine spindle. See automatic toolchanger.
- tungsten carbide ( WC)
tungsten carbide ( WC)
Intermetallic compound consisting of equal parts, by atomic weight, of tungsten and carbon. Sometimes tungsten carbide is used in reference to the cemented tungsten carbide material with cobalt added and/or with titanium carbide or tantalum carbide added. Thus, the tungsten carbide may be used to refer to pure tungsten carbide as well as co-bonded tungsten carbide, which may or may not contain added titanium carbide and/or tantalum carbide.
- undercut
undercut
In numerical-control applications, a cut shorter than the programmed cut resulting after a command change in direction. Also a condition in generated gear teeth when any part of the fillet curve lies inside of a line drawn tangent to the working profile at its point of juncture with the fillet. Undercut may be deliberately introduced to facilitate finishing operations, as in preshaving.
- work envelope
work envelope
Cube, sphere, cylinder or other physical space within which the cutting tool is capable of reaching.