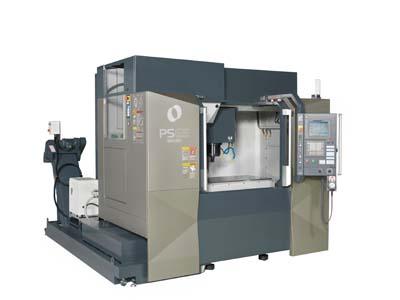
Makino's PS-Series vertical machining centers for production machining offer a reduction in cycle time, increase productivity, improve quality and minimize of capital investment, according to the company. The PS-Series features a field-proven design with key technologies from several of Makino's most reliable production machines. Its rigid construction, thermal stability and versatile spindle are ideal for a variety of applications, including automotive, aerospace, medical and other small-component manufacturing applications.
"Makino's PS-Series comes standard with a high power 33.5 HP, high speed 14,000-rpm CAT40 spindle delivering 130 ft-lbs peak torque. No other vertical comes standard with these features," says William Howard, Makino's vertical machining product manager. "The PS-Series is fully equipped and ready to run all of a manufacturer's production parts. It brings the productivity of a Makino horizontal machining center to a vertical platform at a great value."
The PS-Series is available in two models: the PS65 and PS95. The smaller PS65 features X-, Y- and Z-axis travels of 26", 20" and 18.1", respectively; a 36.2"-by-20" table; and a maximum workload of 1,323 lbs. The larger PS95 features X-, Y- and Z-axis travels of 36.2", 20" and 18.1", respectively; a 46"-by-20" table; and a maximum workload of 1,763 lbs. Both models are standardly equipped with an easy-to-access, highly reliable, 30-tool-capacity automatic tool changer (optional 50-tool capacity available).
Based upon a traditional C frame, the PS-Series design utilizes Finite Element Analysis (FEA) techniques to perfect the massive cast iron components that offer optimal rigidity and torsional stiffness. The construction ensures the quick, efficient transfer of the cutting forces through the structure of the machine, from spindle into the column and ultimately the bed of the machine. In addition, the symmetrical nature of the casting, incorporation of core-cooled ball screws and support bearings and a closed-loop temperature compensation system secure the tightest tolerance and minimal variations during long production part runs.
Designed for flexibility and high productivity, the PS-Series standard 14,000-rpm CAT40 spindle (HSK-A63 optional) offers the ideal blend of speed, torque and horsepower for today's competitive job shop environment. Duty rated at 33.5 HP (24.2 HP continuous) and 130 ft-lbs peak torque (70.5 ft-lbs continuous), these spindle characteristics offer efficient, highly productive machining over a wide range of materials. Large-diameter bearings, air-oil lubrication and jacket-spindle temperature control deliver long-term thermal stability and stiff, rigid, chatter-free cutting.
Created with the production environment in mind, the PS-Series chip and coolant systems enhance the productivity of the machine. Configured with flood, overhead shower, flush and through-spindle coolant as standard features, chips are efficiently and effectively removed from the cutting zone. Spiral chip augers located in the front and rear of the worktable quickly and efficiently evacuate chips and coolant from the machining zone and into a standard lift-up chip conveyor (LUCC).
The PS-Series also features Makino's new Professional P control software configured to support a wide variety of applications in the job-shop and production environment. With a large color LCD, menu-driven, touch-sensitive screen, information is at one's fingertips. Configured with generous program storage (4,200-foot), 400 registerable programs, 400 tool-offset pairs and 48 pairs of work coordinate systems, the Professional P provides ample standard capabilities for production shops of all sizes.
Contact Details
Related Glossary Terms
- centers
centers
Cone-shaped pins that support a workpiece by one or two ends during machining. The centers fit into holes drilled in the workpiece ends. Centers that turn with the workpiece are called “live” centers; those that do not are called “dead” centers.
- coolant
coolant
Fluid that reduces temperature buildup at the tool/workpiece interface during machining. Normally takes the form of a liquid such as soluble or chemical mixtures (semisynthetic, synthetic) but can be pressurized air or other gas. Because of water’s ability to absorb great quantities of heat, it is widely used as a coolant and vehicle for various cutting compounds, with the water-to-compound ratio varying with the machining task. See cutting fluid; semisynthetic cutting fluid; soluble-oil cutting fluid; synthetic cutting fluid.
- machining center
machining center
CNC machine tool capable of drilling, reaming, tapping, milling and boring. Normally comes with an automatic toolchanger. See automatic toolchanger.
- payload ( workload)
payload ( workload)
Maximum load that the robot can handle safely.
- stiffness
stiffness
1. Ability of a material or part to resist elastic deflection. 2. The rate of stress with respect to strain; the greater the stress required to produce a given strain, the stiffer the material is said to be. See dynamic stiffness; static stiffness.
- tolerance
tolerance
Minimum and maximum amount a workpiece dimension is allowed to vary from a set standard and still be acceptable.