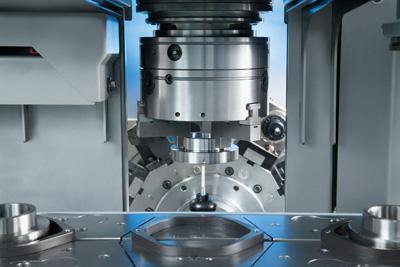
According to analysis by the international trade experts at Germany Trade and Invest (GTAI), US and Canadian industry will focus on high-tech machine tools in the coming years with flexible, largely automated and energy efficient manufacturing systems that provide a viable alternative to Asian competition in demand. EMAG's solution to these challenges is their patented pick-up technology machining concept, developed and tailor-made for the North American market. An innovative automation model, the work spindle picks-up and transports workpieces to the machining area. This guarantees highly efficient and energy-saving production of turned parts and proves itself over complex, interlinked systems.
Overall Equipment Effectiveness (OEE) is the measure used by many companies to determine how economical a machine is. Taking into account the availability rate of the machine, its efficiency level and the component quality produced, all three factors are important in determining the added value of the technology used. "This applies in particular to machine tools," states Peter Loetzner, CEO EMAG USA. "EMAG considers the OEE factors a top priority in the development of new manufacturing solutions and our pick-up technology is a result of that."
EMAG began developing this innovative idea in the early 1990s and, over the years, have expanded their range of new applications and proceeded to perfect its processes. The work spindle is used to transfer the workpieces into the machining area, representing the integrated automation. This is followed by different high-speed machining operations, carried out in a single setup and with short travel distances. This successful approach can be defined by buzzwords such as simplification and flexibility. "Although the automation technology we apply may be uncomplicated, it allows for a large number of operations to be carried out with flexibility," explains Loetzner.
The advantages the pick-up principle offers is clear through a comparison with competitive technology, using the aforementioned OEE factors of machine availability, efficiency and component quality. Multi-layer manufacturing systems, for instance, frequently use robots or complex gripper systems to link individual machines. It is not uncommon that the flow of workpieces in these systems is difficult to control and, therefore, liable to interruptions. Of course, system availability always suffers where there are stoppages. "We are doing it a different way. The whole production process is stable and error-free, since the pick-up technology ensures that these parts of the usual automation system are superfluous, even in multi-layer manufacturing systems," says Loetzner.
The workpiece is transported between machines on conveyor belts or shuttle systems located behind the machining area. Simple automation modules also pick up the workpieces from the conveyor belt and insert them into the carrier prisms of the individual machines. The rest of the work is done by the work spindle. Thus, the amount of automation can be reduced 15 to 30 percent compared to other solutions, while the tailor-made machine design ensures a safe production process. "Machine availability is very high," adds Loetzner. Efficiency is achieved through short travel distances between the compact pick-up machines. This ensures component throughput times are minimised and high output rates are achieved. Loetzner confirms, "We have had a good analysis of other concepts on the market. Complex, interlinked solutions, in particular, have a lower output rate than our manufacturing systems with pick-up machines."
The strengths of EMAG automation applies not only to multi-layer production lines, but also with stand-alone machines, on which highly flexible production processes can be implemented. In these cases, the operator inserts chucked components manually into the carrier prisms that transport them to the pick-up station. The operator also removes the finish-machined components from their carrier prisms. Production companies may think it simpler to carry out this process on a manually loaded horizontal lathe than a partially automated vertical turning machine.
"If you look closer, you will find that the opposite is true," explains Loetzner, "Especially when considering the OEE factor of component quality, loading the machine manually involves risks that can lead to clamping errors. In the automotive sector, particularly, one µm often determines component quality. In the case of the horizontal machine, too much depends on the operator's capability." Thus, the pick-up concept provides the best solution to clamp and machine workpieces with great accuracy. Measuring systems can also be incorporated and used to monitor quality, reducing the possibility of errors to an absolute minimum.
Last, but by no means least, are the important role technical developments play in the effectiveness of a machine. Many transmission and engine components, for example, have changed enormously over the years and have tended to decrease in size, while their geometry becomes more complex. Despite this, all the relevant production processes must be, and remain, highly productive. "The 'future-factor' is often underestimated. When a new machine slows down after a few years and can no longer be adapted to changing conditions, it has a negative influence on its overall effectiveness," emphasises Loetzner.
The flexibility of their machines is of great importance to EMAG, where a modular design is used to configure every single machine to suit a particular task. Every operation, as well as the extent of its automation, can be changed as required. This ensures that the system can be adjusted to increasing batch sizes or changing component specifications. In the face of rapidly accelerating technological changes in many sectors, EMAG machine builders see an encouraging market.
"Developments are meeting us halfway, so to speak," Loetzner suggests. "We are in a position to offer a pick-up solution that is tailor-made to the customer's requirements for every turned part. The effectiveness of the system is higher than other comparable automation technology solutions. This is the kind of quality that wins."
Contact Details
Related Glossary Terms
- lathe
lathe
Turning machine capable of sawing, milling, grinding, gear-cutting, drilling, reaming, boring, threading, facing, chamfering, grooving, knurling, spinning, parting, necking, taper-cutting, and cam- and eccentric-cutting, as well as step- and straight-turning. Comes in a variety of forms, ranging from manual to semiautomatic to fully automatic, with major types being engine lathes, turning and contouring lathes, turret lathes and numerical-control lathes. The engine lathe consists of a headstock and spindle, tailstock, bed, carriage (complete with apron) and cross slides. Features include gear- (speed) and feed-selector levers, toolpost, compound rest, lead screw and reversing lead screw, threading dial and rapid-traverse lever. Special lathe types include through-the-spindle, camshaft and crankshaft, brake drum and rotor, spinning and gun-barrel machines. Toolroom and bench lathes are used for precision work; the former for tool-and-die work and similar tasks, the latter for small workpieces (instruments, watches), normally without a power feed. Models are typically designated according to their “swing,” or the largest-diameter workpiece that can be rotated; bed length, or the distance between centers; and horsepower generated. See turning machine.
- modular design ( modular construction)
modular design ( modular construction)
Manufacturing of a product in subassemblies that permits fast and simple replacement of defective assemblies and tailoring of the product for different purposes. See interchangeable parts.
- turning
turning
Workpiece is held in a chuck, mounted on a face plate or secured between centers and rotated while a cutting tool, normally a single-point tool, is fed into it along its periphery or across its end or face. Takes the form of straight turning (cutting along the periphery of the workpiece); taper turning (creating a taper); step turning (turning different-size diameters on the same work); chamfering (beveling an edge or shoulder); facing (cutting on an end); turning threads (usually external but can be internal); roughing (high-volume metal removal); and finishing (final light cuts). Performed on lathes, turning centers, chucking machines, automatic screw machines and similar machines.
- turning machine
turning machine
Any machine that rotates a workpiece while feeding a cutting tool into it. See lathe.