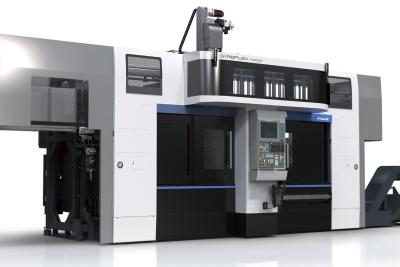
At FUJI Innovation Days 2020 in November, Fuji Machine revealed its latest innovation in automation - the GYROFLEX Ultimate Multitasking Machine. Attendees at the event got the first glimpse of this exceptionally rigid and productive machine. Featuring the latest industry-leading technology, it is designed for unprecedented flexibility, efficiency and accuracy.
The GYROFLEX offers the flexibility to meet a variety of production demands, from low production volume and parts prototyping to high-volume and high-mixed production. A single GYROFLEX requires reduced setup and changeover times and completes complex parts efficiently and accurately.
The machine’s integrated Fuji-built LX-40 3-axis gantry robot enables unattended operation and fast parts handling. The hydraulic robot chuck provides stable clamping and workpiece handling using minimum space thanks to the innovative thin-type double hand design. Easy programming for complex parts and process combination are made possible with an ESPRIT 3D CAD/CAM system. In addition, the perfect chip disposal design enables non-stop production.
The GYROFLEX’s opposed twin spindles are positioned on Z-axis slideways with 960mm of stroke. Equal in size and capability, each spindle is capable of performing the same operations (OP-10A/10B). The Z-axis slide moves at high speeds to reduce loading time to the second spindle.
A milling tool spindle, mounted on rigid X and Y axes box way slides, allows for various types of machining by accessing both Z-axis spindles and swinging up to 190 degrees. Milling tool spindle speeds reach 12,000 rpm with a 15 HP spindle motor. A 15-station live tool turret, also positioned on highly rigid X & Y axes box way slides, offers indexing times of 0.4 sec. and spindle speeds of 4,000 rpm max. with a 6 HP spindle motor.
The GYROFLEX ATC rapid tool change time is 4 sec., maximum tool diameter is 130mm, tool length is 300mm and tool weight is 8 kg. Fuji’s GYROFLEX features a 40-tool ATC and a Fanuc 31i-B Plus controller. The machine footprint is 5000 x 3000mm (16’5” x 9’10”) and height is 3530mm (11’7”).
Fuji turns the machining of a part into process perfection. When you contact Fuji, the part you will be machining is analyzed by engineers with vast experience in process and manufacturing engineering. With the largest install base at the major automotive manufacturers, Fuji engineers apply their experience with the Fuji machines that are built for automation from the ground up. These highly accurate machines employ built-in robotic automation, in-process auto gauging for quality control, and are engineered with the finest Fuji custom workholding, all from one source. This allows Fuji engineers to guarantee takt time, cycle time and CPK with turnkey and run-off solutions that are built for lean manufacturing. Using less manpower and more automation, Fuji machines produce the highest quality parts most efficiently and reliably. Fuji solutions are supported by factory-trained engineers 24/7.
Contact Details
Related Glossary Terms
- chuck
chuck
Workholding device that affixes to a mill, lathe or drill-press spindle. It holds a tool or workpiece by one end, allowing it to be rotated. May also be fitted to the machine table to hold a workpiece. Two or more adjustable jaws actually hold the tool or part. May be actuated manually, pneumatically, hydraulically or electrically. See collet.
- gang cutting ( milling)
gang cutting ( milling)
Machining with several cutters mounted on a single arbor, generally for simultaneous cutting.
- gantry robot
gantry robot
Robot positioned by means of an overhead supporting structure such as a crane or bridge-type support.
- lean manufacturing
lean manufacturing
Companywide culture of continuous improvement, waste reduction and minimal inventory as practiced by individuals in every aspect of the business.
- milling
milling
Machining operation in which metal or other material is removed by applying power to a rotating cutter. In vertical milling, the cutting tool is mounted vertically on the spindle. In horizontal milling, the cutting tool is mounted horizontally, either directly on the spindle or on an arbor. Horizontal milling is further broken down into conventional milling, where the cutter rotates opposite the direction of feed, or “up” into the workpiece; and climb milling, where the cutter rotates in the direction of feed, or “down” into the workpiece. Milling operations include plane or surface milling, endmilling, facemilling, angle milling, form milling and profiling.
- quality assurance ( quality control)
quality assurance ( quality control)
Terms denoting a formal program for monitoring product quality. The denotations are the same, but QC typically connotes a more traditional postmachining inspection system, while QA implies a more comprehensive approach, with emphasis on “total quality,” broad quality principles, statistical process control and other statistical methods.