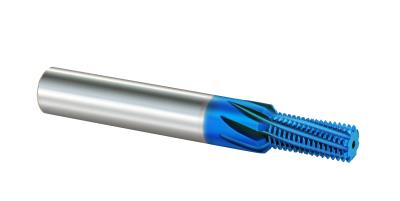
Constructed of rugged MT8 carbide with Carmex’s exclusive BLU coating, the new FMT thread mill delivers accurate thread geometry and fine surface quality in short cycle times. Unlike conventional taps, the FMT can thread up to the bottom of a blind-hole while delivering the high reliability necessary for complex parts.
FMT’s high-speed performance results from the increased number of flutes, which require an extremely heavy-duty carbide grade, as well as advanced coating technology in order to ensure a high degree of performance and
longer tool life.
In a recent test, an FMT thread mill with a 6-flute cutter and internal coolant created a 10mm internal right-hand thread to the bottom of a blind hole in SAE 4340 steel. The cycle time was 1.5 seconds and the tool life was 2,170 threads. In that test, and in any number of other applications, the FMT is emerging as the suitable thread mill for high-production/high-demand applications.
Contact Details
Related Glossary Terms
- blind-hole
blind-hole
Hole or cavity cut in a solid shape that does not connect with other holes or exit through the workpiece.
- coolant
coolant
Fluid that reduces temperature buildup at the tool/workpiece interface during machining. Normally takes the form of a liquid such as soluble or chemical mixtures (semisynthetic, synthetic) but can be pressurized air or other gas. Because of water’s ability to absorb great quantities of heat, it is widely used as a coolant and vehicle for various cutting compounds, with the water-to-compound ratio varying with the machining task. See cutting fluid; semisynthetic cutting fluid; soluble-oil cutting fluid; synthetic cutting fluid.
- flutes
flutes
Grooves and spaces in the body of a tool that permit chip removal from, and cutting-fluid application to, the point of cut.
- milling machine ( mill)
milling machine ( mill)
Runs endmills and arbor-mounted milling cutters. Features include a head with a spindle that drives the cutters; a column, knee and table that provide motion in the three Cartesian axes; and a base that supports the components and houses the cutting-fluid pump and reservoir. The work is mounted on the table and fed into the rotating cutter or endmill to accomplish the milling steps; vertical milling machines also feed endmills into the work by means of a spindle-mounted quill. Models range from small manual machines to big bed-type and duplex mills. All take one of three basic forms: vertical, horizontal or convertible horizontal/vertical. Vertical machines may be knee-type (the table is mounted on a knee that can be elevated) or bed-type (the table is securely supported and only moves horizontally). In general, horizontal machines are bigger and more powerful, while vertical machines are lighter but more versatile and easier to set up and operate.