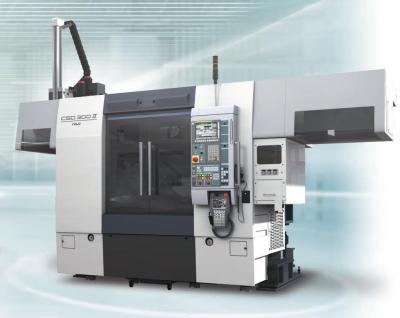
The newly designed CSD-300II Front Facing Twin Spindle Lathe will be on display in booth 339059 at IMTS 2020. The latest generation of Fuji’s CSD Series, and an upgrade to the CSD-300 Twin Spindle Lathe, the CSD-300II is more robust, with increased rigidity, and loaded with new and improved features for faster, easier and stronger operation.
Impressively productive, the CSD-300II achieves faster robot traverse and turret indexing speeds than its predecessor. For exceptionally quick and accurate turning of a variety of parts, turret index times are as low as .19 seconds, robot cycle times 17.9 seconds and loading times 4.8 seconds.
Operation and changeover are easier and more efficient than ever with the CSD-300II. The horizontal lathe is equipped with an innovative new dual gantry robot and the latest FANUC controls. In addition, the CSD-300II features an improved custom HMI and a single integrated Fanuc control panel that allows for convenient operation and setup of the machine and robot. A clamp/unclamp switch for the robot chuck and the robot’s centralized lubrication system are included as standard. What’s more, the CSD-300II comes ready to quickly connect to IoT, including Fuji’s LAPSYS desktop software. Available as an option, LAPSYS reads scanned laser etchings to trace the origin of a part, including machine and spindle, and enables part traceability, predictive maintenance and remote operation.
An optimized bed design, with a grooving width of 14mm, renders this lathe exceptionally rigid.
Providing maximum material handling from a compact 2260mm x 1980mm footprint, the CSD-300II accurately manages heavy parts Ø 200mm x 100mm and 5kg + 5kg. The CSD-300II also features a Fuji-engineered hydraulic clamping loader and 8” – 10” capacity chucks.
Fuji turns the machining of a part into process perfection. When you contact Fuji, the part you will be machining is analyzed by engineers with vast experience in process and manufacturing engineering. With the largest install base at the major automotive manufacturers, Fuji engineers apply their experience with the Fuji machines that are built for automation from the ground up. These highly accurate machines employ built-in robotic automation, in-process auto gauging for quality control, and are engineered with the finest Fuji custom workholding, all from one source. This allows Fuji engineers to guarantee takt time, cycle time and CPK with turnkey and run-off solutions that are built for lean manufacturing. Using less manpower and more automation, Fuji machines produce the highest quality parts most efficiently and reliably. Fuji solutions are supported by factory-trained engineers 24/7.
Contact Details
Related Glossary Terms
- chuck
chuck
Workholding device that affixes to a mill, lathe or drill-press spindle. It holds a tool or workpiece by one end, allowing it to be rotated. May also be fitted to the machine table to hold a workpiece. Two or more adjustable jaws actually hold the tool or part. May be actuated manually, pneumatically, hydraulically or electrically. See collet.
- gantry robot
gantry robot
Robot positioned by means of an overhead supporting structure such as a crane or bridge-type support.
- grooving
grooving
Machining grooves and shallow channels. Example: grooving ball-bearing raceways. Typically performed by tools that are capable of light cuts at high feed rates. Imparts high-quality finish.
- lathe
lathe
Turning machine capable of sawing, milling, grinding, gear-cutting, drilling, reaming, boring, threading, facing, chamfering, grooving, knurling, spinning, parting, necking, taper-cutting, and cam- and eccentric-cutting, as well as step- and straight-turning. Comes in a variety of forms, ranging from manual to semiautomatic to fully automatic, with major types being engine lathes, turning and contouring lathes, turret lathes and numerical-control lathes. The engine lathe consists of a headstock and spindle, tailstock, bed, carriage (complete with apron) and cross slides. Features include gear- (speed) and feed-selector levers, toolpost, compound rest, lead screw and reversing lead screw, threading dial and rapid-traverse lever. Special lathe types include through-the-spindle, camshaft and crankshaft, brake drum and rotor, spinning and gun-barrel machines. Toolroom and bench lathes are used for precision work; the former for tool-and-die work and similar tasks, the latter for small workpieces (instruments, watches), normally without a power feed. Models are typically designated according to their “swing,” or the largest-diameter workpiece that can be rotated; bed length, or the distance between centers; and horsepower generated. See turning machine.
- lean manufacturing
lean manufacturing
Companywide culture of continuous improvement, waste reduction and minimal inventory as practiced by individuals in every aspect of the business.
- quality assurance ( quality control)
quality assurance ( quality control)
Terms denoting a formal program for monitoring product quality. The denotations are the same, but QC typically connotes a more traditional postmachining inspection system, while QA implies a more comprehensive approach, with emphasis on “total quality,” broad quality principles, statistical process control and other statistical methods.
- turning
turning
Workpiece is held in a chuck, mounted on a face plate or secured between centers and rotated while a cutting tool, normally a single-point tool, is fed into it along its periphery or across its end or face. Takes the form of straight turning (cutting along the periphery of the workpiece); taper turning (creating a taper); step turning (turning different-size diameters on the same work); chamfering (beveling an edge or shoulder); facing (cutting on an end); turning threads (usually external but can be internal); roughing (high-volume metal removal); and finishing (final light cuts). Performed on lathes, turning centers, chucking machines, automatic screw machines and similar machines.