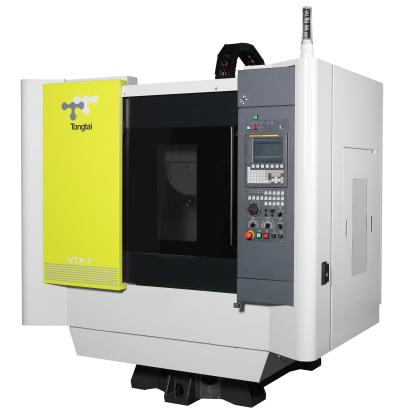
With rapid traverse speeds up to 2,362 ipm (60 m/min.) in all axes and acceleration of 1.2 g, the Tongtai VTX series of drilling and tapping centers are fast, affordable machines for high-precision, high-volume applications. The machines’ compact 87" x 63" (2,210 mm x 1,600 mm) footprint conserves shop floor space, and a fixed column/moving table type design with Meehanite cast-iron frames and roller-type linear slideways provides rigidity and fast, precise movement.
Two types of high-speed ATC systems are available. The 21-tool turret-type ATC on VTX-5 and VTX-7 models offers tool change time of 1.4 seconds tool-to-tool and 1.9 seconds chip-to-chip. VTX-5A and 7A versions have a 20-tool arm-type ATC system that reduces tool change time to 0.8 seconds tool-to-tool and 1.3 seconds chip-to-chip.
The standard 7.5-hp, 12,000-rpm direct-drive spindle provides rigid tap speeds up to 6,000 rpm. An optional 24,000-rpm direct-drive spindle delivers high speeds for machining aluminum and magnesium parts and is an excellent choice for processing graphite. A BBT-30 (Big Plus dual contact) taper is standard for rigid milling. Coolant-through the spindle preparation also is standard, as is a spindle chiller.
A Mitsubishi M80A control is standard and is suitable for applications ranging from production to high-speed machining. It features a 10.4" (264 mm) touch screen with intuitive smartphone type operation. A dedicated CNC CPU provides outstanding processing speeds. State-of-the-art speed and accuracy results from an all-new high-response servo system with 1,000,000 pulse encoders. The Mitsubishi M80A control comes with a three-year parts and labor warranty. A FANUC OiM-F control with 8.4" (203 mm) LCD with a two-year warranty is also available.
Contact Details
Related Glossary Terms
- centers
centers
Cone-shaped pins that support a workpiece by one or two ends during machining. The centers fit into holes drilled in the workpiece ends. Centers that turn with the workpiece are called “live” centers; those that do not are called “dead” centers.
- computer numerical control ( CNC)
computer numerical control ( CNC)
Microprocessor-based controller dedicated to a machine tool that permits the creation or modification of parts. Programmed numerical control activates the machine’s servos and spindle drives and controls the various machining operations. See DNC, direct numerical control; NC, numerical control.
- gang cutting ( milling)
gang cutting ( milling)
Machining with several cutters mounted on a single arbor, generally for simultaneous cutting.
- inches per minute ( ipm)
inches per minute ( ipm)
Value that refers to how far the workpiece or cutter advances linearly in 1 minute, defined as: ipm = ipt 5 number of effective teeth 5 rpm. Also known as the table feed or machine feed.
- milling
milling
Machining operation in which metal or other material is removed by applying power to a rotating cutter. In vertical milling, the cutting tool is mounted vertically on the spindle. In horizontal milling, the cutting tool is mounted horizontally, either directly on the spindle or on an arbor. Horizontal milling is further broken down into conventional milling, where the cutter rotates opposite the direction of feed, or “up” into the workpiece; and climb milling, where the cutter rotates in the direction of feed, or “down” into the workpiece. Milling operations include plane or surface milling, endmilling, facemilling, angle milling, form milling and profiling.
- rapid traverse
rapid traverse
Movement on a CNC mill or lathe that is from point to point at full speed but, usually, without linear interpolation.
- tap
tap
Cylindrical tool that cuts internal threads and has flutes to remove chips and carry tapping fluid to the point of cut. Normally used on a drill press or tapping machine but also may be operated manually. See tapping.
- tapping
tapping
Machining operation in which a tap, with teeth on its periphery, cuts internal threads in a predrilled hole having a smaller diameter than the tap diameter. Threads are formed by a combined rotary and axial-relative motion between tap and workpiece. See tap.