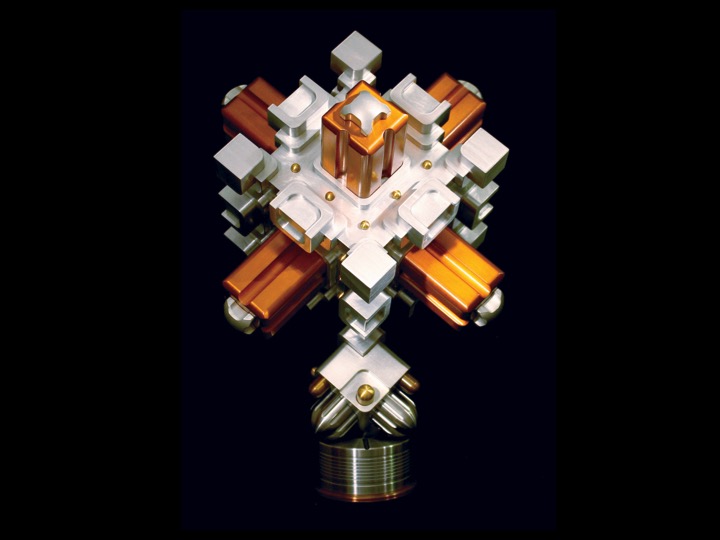
A metal blisk or heat exchanger component can certainly be aesthetically pleasing, but those and the vast majority of other machined metal parts serve a practical function first and foremost. The metal parts Chris Bathgate machines don’t.
That’s because Bathgate is a metal sculptor. “My approach to sculptures is most purely about the engineering involved, using machine work as the creative medium,” he said.
Bathgate explained that he started to learn welding while in high school and studied sculpture at art school but became disillusioned and dropped out. He continued to weld sculptures but soon tried another approach. That was 18 years ago.
“I started dabbling with machining and quickly found it infinitely more fascinating than welding and shaping steel with the torch,” Bathgate said. “That led me down the road to learning machining.”
Being a struggling artist and with a dearth of low-cost machine tool options, with the possible exception of micromachining centers, Bathgate decided to build his own equipment “using cheaper Chinese iron and off-the-shelf electronics.” Even without a mechanical engineering background, he built two milling machines and two lathes over the years, as well as a 3D printer for making fixtures and models.
“As those machines have worn out and broken down, I’ve substituted them with lower-cost entries,” he added.
In addition to a limited budget, Bathgate’s shop/studio in the basement of his house in Baltimore has a ceiling height of only 6'6". “Some machine heads go up between the ceiling joints. I’m working in special circumstances for sure,” he said, adding that he’s looking to move to a ground-level studio.
The full article is available in the Shop Operations column of the March 2019 issue.
Editor's Note: A video about Bathgate's path to becoming a machinist sculptor is available by clicking here.
Related Glossary Terms
- centers
centers
Cone-shaped pins that support a workpiece by one or two ends during machining. The centers fit into holes drilled in the workpiece ends. Centers that turn with the workpiece are called “live” centers; those that do not are called “dead” centers.
- gang cutting ( milling)
gang cutting ( milling)
Machining with several cutters mounted on a single arbor, generally for simultaneous cutting.
- milling
milling
Machining operation in which metal or other material is removed by applying power to a rotating cutter. In vertical milling, the cutting tool is mounted vertically on the spindle. In horizontal milling, the cutting tool is mounted horizontally, either directly on the spindle or on an arbor. Horizontal milling is further broken down into conventional milling, where the cutter rotates opposite the direction of feed, or “up” into the workpiece; and climb milling, where the cutter rotates in the direction of feed, or “down” into the workpiece. Milling operations include plane or surface milling, endmilling, facemilling, angle milling, form milling and profiling.
- shaping
shaping
Using a shaper primarily to produce flat surfaces in horizontal, vertical or angular planes. It can also include the machining of curved surfaces, helixes, serrations and special work involving odd and irregular shapes. Often used for prototype or short-run manufacturing to eliminate the need for expensive special tooling or processes.