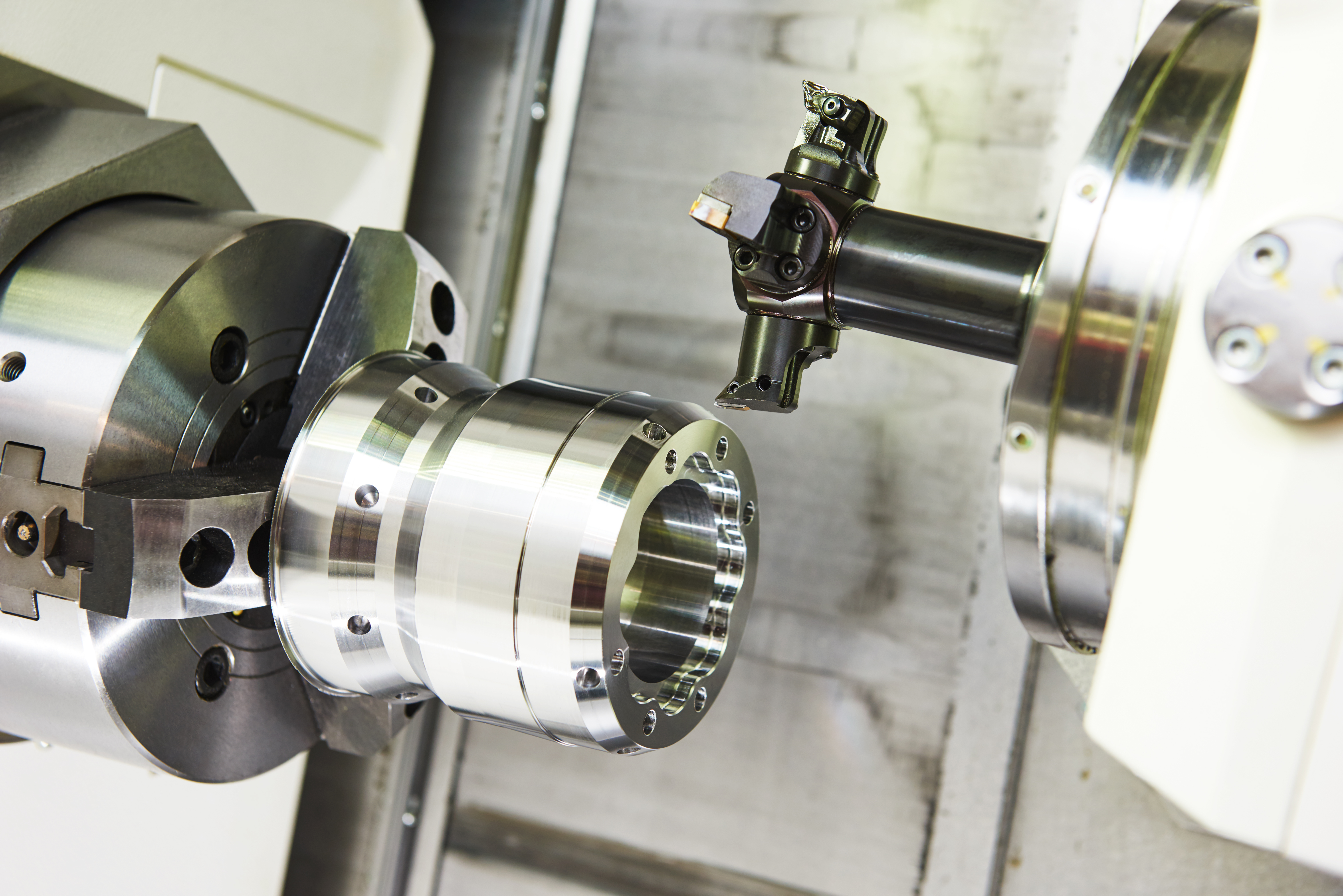
Multiple-axis machining offers many benefits to parts manufacturers that can correctly harness and implement the capabilities of this technology. Ultimately, it is an effective step towards factory automation, offering the opportunity to condense multiple machine operations into one, saving takt time, total production time, production cost and improving tolerances.
The efficiencies and benefits offered by multiaxis machining are largely thanks to the reduced setup time required. This decreases the burden rate on operators because they don’t have to refixture as many parts. Decreasing the number of setups also enables machining complex shapes in a single fixturing, reducing the potential for operator error and helping to ensure the accuracy of the final product because it avoids stacking up tolerances.
While traditional 3-axis machining may require three or four different machines to produce a final part, this entire process could be replaced by a single 5-axis machine. Machines with seven or more axes go even further, allowing manufacturers to combine milling, drilling, grinding and turning on a single machine.
Despite high initial capital costs, the potential for substantial production efficiencies and improved final product quality offer significant return on investment, through reduced process cost and scrap rates.
Currently, adoption of multiaxis machining has been slower than might have been anticipated. Small and medium-sized manufacturers tend to have settled with 3-axis machines until they can see the ROI that can be achieved, whereas larger OEMs are moving into 5-, 7-, and 11-axis machines, potentially with multiple spindles.
Small and medium-sized manufacturers also have a tendency to hold on to and try to obtain the maximum value from legacy equipment before investing in new systems, which may be contributing to the slow adoption of more-efficient machines. This goes hand in hand with a behavioral issue around reluctance to change. If operators are used to a certain style, and they know how to program and design for it, any change can cause disruption and upheaval.
Of course, adoption is highly dependent on the production needs and orientation of individual manufacturers, and varies between business size and sector. There’s a recognition of the benefits that multiaxis machining offers, and certainly an increased interest in acquiring and using them, but because of perceived challenges in setup, the speed of implementation is not high.
Adoption is dependent on the value of the machine to the manufacturer. This means assessing how quickly ROI will be achieved. ROI must be assessed based on individual manufacturers’ revenue streams and market demand for more robust manufacturing processes. It’s important not to be oversold.
Implementing a new machine implies much more than just cost and skill issues. It can necessitate a change in the manufacturing philosophy of a plant. It carries implications beyond the machine itself, such as reducing the number of operations and integration of the new technology with the entire value stream to optimize ROI.
The impact on personnel in terms of training and development can also be significant. Once a multiaxis machine is implemented, the workforce requires the necessary skills to operate it. It’s also critical that the requisite CAD/CAM programs are in place to manage complex multi-axis operations.
One of the key issues OPTIS, which is a joint venture between manufacturing consultancy TechSolve and lubricant manufacturer Castrol, sees with the implementation of multiaxis machining is that machine tool builders often sell manufacturers more complex machines than are really necessary. A lot of companies may have bought 5-axis machines, for example, but operate them as they would a 3-axis, wasting capacity and reducing the ROI.
Despite perceived complexities in its set up, the benefits of a well-implemented multiaxis machine far outweigh any pitfalls along the route to implementation. For many manufacturers looking to harness the efficiency gains of automation, multiaxis machining can provide a sensible, efficient step in that journey. It is a proven technology that can reduce human error and achieve tight tolerances by increasing automation, simplifying operations and improving product quality.
—Jon Iverson, CEO at OPTIS, Cincinnati
Related Glossary Terms
- gang cutting ( milling)
gang cutting ( milling)
Machining with several cutters mounted on a single arbor, generally for simultaneous cutting.
- grinding
grinding
Machining operation in which material is removed from the workpiece by a powered abrasive wheel, stone, belt, paste, sheet, compound, slurry, etc. Takes various forms: surface grinding (creates flat and/or squared surfaces); cylindrical grinding (for external cylindrical and tapered shapes, fillets, undercuts, etc.); centerless grinding; chamfering; thread and form grinding; tool and cutter grinding; offhand grinding; lapping and polishing (grinding with extremely fine grits to create ultrasmooth surfaces); honing; and disc grinding.
- milling
milling
Machining operation in which metal or other material is removed by applying power to a rotating cutter. In vertical milling, the cutting tool is mounted vertically on the spindle. In horizontal milling, the cutting tool is mounted horizontally, either directly on the spindle or on an arbor. Horizontal milling is further broken down into conventional milling, where the cutter rotates opposite the direction of feed, or “up” into the workpiece; and climb milling, where the cutter rotates in the direction of feed, or “down” into the workpiece. Milling operations include plane or surface milling, endmilling, facemilling, angle milling, form milling and profiling.
- turning
turning
Workpiece is held in a chuck, mounted on a face plate or secured between centers and rotated while a cutting tool, normally a single-point tool, is fed into it along its periphery or across its end or face. Takes the form of straight turning (cutting along the periphery of the workpiece); taper turning (creating a taper); step turning (turning different-size diameters on the same work); chamfering (beveling an edge or shoulder); facing (cutting on an end); turning threads (usually external but can be internal); roughing (high-volume metal removal); and finishing (final light cuts). Performed on lathes, turning centers, chucking machines, automatic screw machines and similar machines.