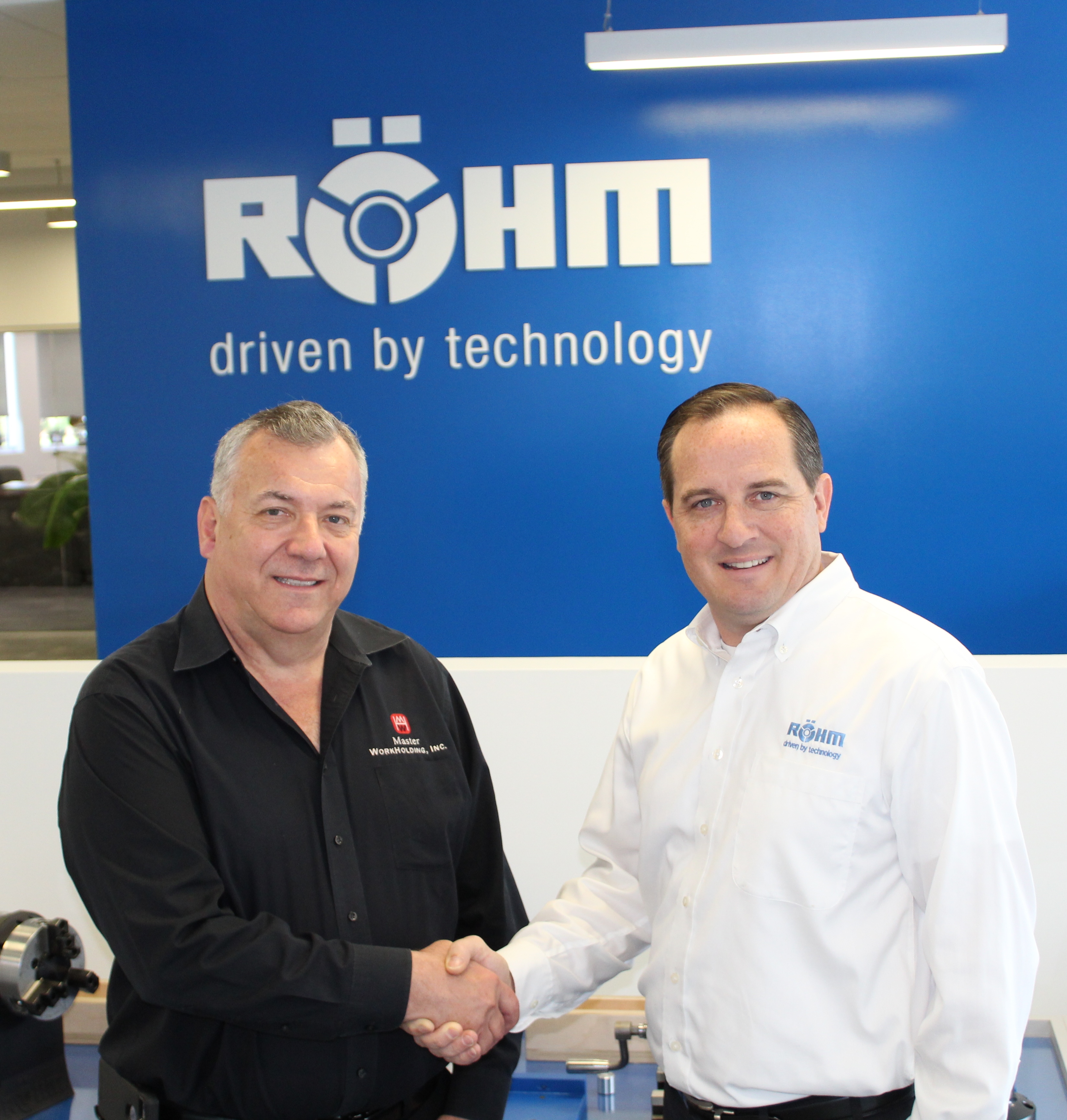
SUWANEE, Ga., August 20, 2018 — RÖHM Products of America Inc., has announced that it has acquired Master WorkHolding Inc. The acquisition enables RÖHM to combine its 100 years of workholding experience with Master WorkHolding’s 30 years of experience to deliver a truly complete range of standard and custom workholding products and automation solutions for all CNC equipment.
“With Master WorkHolding joining the RÖHM team, we will be able to deliver even more comprehensive workholding and automation solutions,” said Matthew Mayer, chief executive officer for RÖHM Products of America. “Both companies have prioritized helping manufacturers obtain quality solutions that maximize productivity and throughput, and this acquisition will make it even easier for our customers to obtain the highest levels of efficiency in turning, milling, grinding and robotic applications.”
Established in North Carolina in 1988, Master WorkHolding has specialized in the design and manufacture of custom prismatic workholding for manufacturers across the continent and around the world. Following the acquisition, the company will serve as RÖHM’s North American manufacturing entity and provide the company with prismatic clamping fixtures.
“This year marks Master WorkHolding’s 30th anniversary, and we are thrilled to celebrate it with our merger with RÖHM,” said Mike Powell, the company’s founder and president. “Together, we will be able to provide custom and standard lines of stationary and rotating workholding and automation, offering our customers a complete range of solutions.”
An active member of the Society of Manufacturing Technology (SME) and the Association of Manufacturing Technology (AMT), the latter of which he served as director, Powell has more than 40 years of experience as a strong supporter of the manufacturing industry. His company, which began as a two-man operation, is widely regarded as one of the premier workholding suppliers in the industry. Prior to the acquisition, the ISO 9001-2015-certified Master WorkHolding sold and delivered thousands of projects over the last 30 years.
Contact Details
Contact Details
Related Glossary Terms
- computer numerical control ( CNC)
computer numerical control ( CNC)
Microprocessor-based controller dedicated to a machine tool that permits the creation or modification of parts. Programmed numerical control activates the machine’s servos and spindle drives and controls the various machining operations. See DNC, direct numerical control; NC, numerical control.
- gang cutting ( milling)
gang cutting ( milling)
Machining with several cutters mounted on a single arbor, generally for simultaneous cutting.
- grinding
grinding
Machining operation in which material is removed from the workpiece by a powered abrasive wheel, stone, belt, paste, sheet, compound, slurry, etc. Takes various forms: surface grinding (creates flat and/or squared surfaces); cylindrical grinding (for external cylindrical and tapered shapes, fillets, undercuts, etc.); centerless grinding; chamfering; thread and form grinding; tool and cutter grinding; offhand grinding; lapping and polishing (grinding with extremely fine grits to create ultrasmooth surfaces); honing; and disc grinding.
- milling
milling
Machining operation in which metal or other material is removed by applying power to a rotating cutter. In vertical milling, the cutting tool is mounted vertically on the spindle. In horizontal milling, the cutting tool is mounted horizontally, either directly on the spindle or on an arbor. Horizontal milling is further broken down into conventional milling, where the cutter rotates opposite the direction of feed, or “up” into the workpiece; and climb milling, where the cutter rotates in the direction of feed, or “down” into the workpiece. Milling operations include plane or surface milling, endmilling, facemilling, angle milling, form milling and profiling.
- turning
turning
Workpiece is held in a chuck, mounted on a face plate or secured between centers and rotated while a cutting tool, normally a single-point tool, is fed into it along its periphery or across its end or face. Takes the form of straight turning (cutting along the periphery of the workpiece); taper turning (creating a taper); step turning (turning different-size diameters on the same work); chamfering (beveling an edge or shoulder); facing (cutting on an end); turning threads (usually external but can be internal); roughing (high-volume metal removal); and finishing (final light cuts). Performed on lathes, turning centers, chucking machines, automatic screw machines and similar machines.