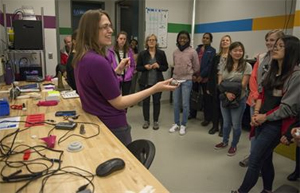
In manufacturing, the nature of the work as well as the nature of the workers are changing: What’s a prospective employer to do? Some pre-Manufacturing Day discussion.
The work has changed: A recent article at Mitsubishi Heavy Industries’ Spectra web site looks at how the terms ‘white-collar- and ‘blue-collar’ are now longer adequate to describe modern manufacturing work. Using an employee at Mitsubishi Hitachi Power Systems as one example, the article by Keith Breene describes why this is ‘new-collar’ work:
“Takeshi has been making rotors for nuclear and thermal power plants for more than a quarter century. As a lathe operator, he would classically be regarded as a blue-collar worker. Yet his work requires levels of accuracy and skill that would challenge even a brain surgeon. Rotors must be manufactured to within 5µm of the required size.”
The rise in workforce skill level makes the facility a more egalitarian workplace, Breene argues:
“…[I]n many factories you would be hard pressed to tell who is working on the ‘shop floor’ and who is plant manager. In the 21st century manufacturing plant, everyone is solving problems, everyone is highly skilled. Everyone, in short, is new-collar.”
Unfortunately, this change in status and stature for the modern manufacturing worker is not yet well-understood among young people looking to enter the workforce:
“That new-collar jobs are safer, more intellectually demanding and better paid than the blue-collar jobs that came before them should make a career in modern manufacturing more appealing than ever.”
(Read Meet Manufacturing’s New-Collar Workers in its entirety here.)
The workers are changing too: There’s another side to the problem of manufacturing positions going unfilled, however. If the new generation isn’t up to speed on clean, high-tech manufacturing, it’s also true that many manufacturers aren’t up to speed on the mindset and abilities of these prospective employees.
The latter issue is addressed in a new Tooling-U-SME White Paper, titled Embracing Millennials: Closing the Manufacturing Skills Gap and Gaining a Competitive Advantage. “It is true that millennials offer unique differences in the workplace than their predecessors,” the introduction notes. “After all, they are shaped by their own life experiences—think recessions, debt, ubiquitous technology. They are also not afraid to question and push boundaries.”
The 16-page paper is worth reading in full. It includes the following 7 tips for working with millennials:
- “Don’t generalize about them.” Respect their individuality.
- “Communicate your corporate mission.” Let them see how their work contributes to it.
- “Show them their future.” Have a visible and accessible path forward.
- “Provide continual learning opportunities.”
- “Go digital.” These folks grew up with the computer and smart phone. Nix the paper already.
- “Allow them to share their ideas.”
- “Provide regular and immediate feedback.”
(The free white paper may be downloaded as a PDF here. Registration required.)
Sizing each other up: But first you have to get future employees in the door—and a good time to start doing so is Manufacturing Day, coming up on Friday, October 6th. Manufacturing Day events let the new generation (or generations—many are aimed at middle- and high-school students) see what our field can offer.
Whether you’re already planning to host a public STEM event at your facility on Manufacturing Day this year or if you’re interested in hosting one in the future, you might benefit from an article by Jennifer Bannink at machine-tool maker Tormach’s blog: It’s called “Bridge Education and Business: 6 Ways to Guarantee a Successful STEM Event.” You can read it here.
Related Glossary Terms
- lathe
lathe
Turning machine capable of sawing, milling, grinding, gear-cutting, drilling, reaming, boring, threading, facing, chamfering, grooving, knurling, spinning, parting, necking, taper-cutting, and cam- and eccentric-cutting, as well as step- and straight-turning. Comes in a variety of forms, ranging from manual to semiautomatic to fully automatic, with major types being engine lathes, turning and contouring lathes, turret lathes and numerical-control lathes. The engine lathe consists of a headstock and spindle, tailstock, bed, carriage (complete with apron) and cross slides. Features include gear- (speed) and feed-selector levers, toolpost, compound rest, lead screw and reversing lead screw, threading dial and rapid-traverse lever. Special lathe types include through-the-spindle, camshaft and crankshaft, brake drum and rotor, spinning and gun-barrel machines. Toolroom and bench lathes are used for precision work; the former for tool-and-die work and similar tasks, the latter for small workpieces (instruments, watches), normally without a power feed. Models are typically designated according to their “swing,” or the largest-diameter workpiece that can be rotated; bed length, or the distance between centers; and horsepower generated. See turning machine.
- web
web
On a rotating tool, the portion of the tool body that joins the lands. Web is thicker at the shank end, relative to the point end, providing maximum torsional strength.