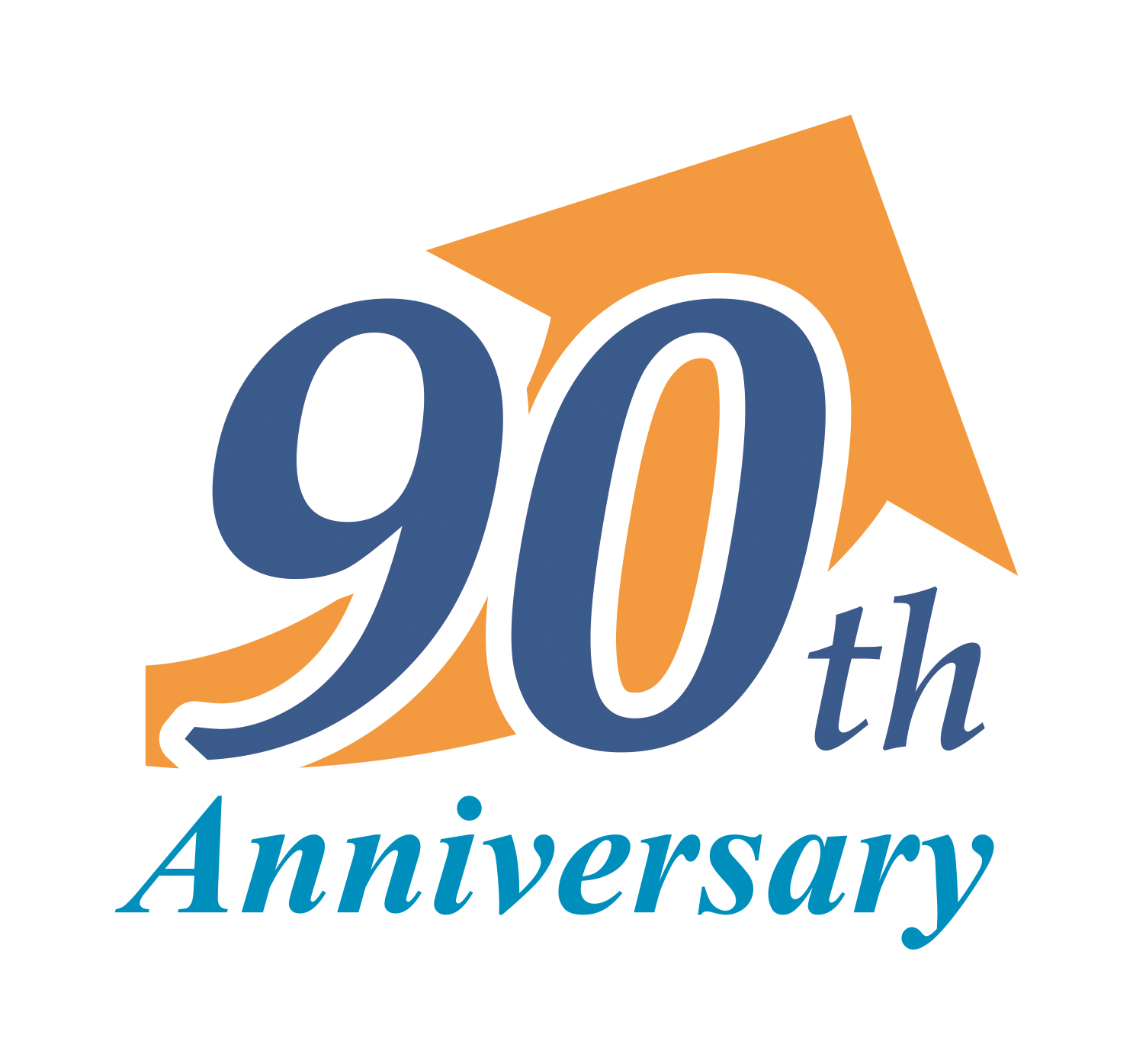
[FRANKLIN LAKES, NJ – AUGUST 2018] Mitsui Seiki, known for its ultra-precise machine tools providing high volumetric accuracies, celebrates its 90th anniversary this fall, and one of the ways the company will mark it is with a champagne toast during IMTS 2018.
“Looking back on our history, the very foundation of precision measurement – gage blocks – were among our first products,” said Robb Hudson, CEO of Mitsui Seiki USA, Inc. Indeed, in 1928, the company manufactured measuring devices, such as gage blocks and micrometers. By 1935, the company developed its first jig boring machine. It was the first in Japan, sparking the machine tool industry there. Industrialists referred to it as Japan’s first “mother” machine because other machine tool builders used it to make their critical precision components. Jig boring machines are often referred to as “mother” machines to this day. Flash ahead to 2018, and the company continues to design and build jig borers, jig grinders, 3-, 4- and 5-axis CNC vertical and horizontal machining centers – including hybrid variations – and internal and external thread grinders.
Mr. Okuda, president of Mitsui Seiki Kogyo Co., Ltd. in Japan, looks upon this milestone anniversary as an opportunity to focus on “internal reformation” to continue to raise quality, productivity and reduce lead times from the headquarters factory, located on the outskirts of Tokyo. He also has goals to expand into other markets, such as mold and prototype sectors. The company is widely known for its expertise in machine tool solutions for hard metal aerospace parts required in jet engines and structural components.
“It’s the perfect time to have this significant milestone anniversary to celebrate,” continues Mr. Hudson. “Manufacturing is abuzz with activity, and we have many opportunities to develop new and efficient machine tool solutions for our sophisticated customer base. At IMTS this year we are launching a new VMC that also finish grinds and we are also pursuing the Blue Arc™ technology in a significant and dedicated manner with GE. The way I look at it is we are positioning ourselves right now for the next 90 years, helping our customers achieve their goals in precision parts manufacturing, factory automation and connectivity across the enterprise.”
Contact Details
Related Glossary Terms
- boring
boring
Enlarging a hole that already has been drilled or cored. Generally, it is an operation of truing the previously drilled hole with a single-point, lathe-type tool. Boring is essentially internal turning, in that usually a single-point cutting tool forms the internal shape. Some tools are available with two cutting edges to balance cutting forces.
- boring machine
boring machine
Similar to a turning machine except that the cutting tool (single-point or multiple-cutting-edge), rather than the workpiece, rotates to perform internal cuts. However, boring can be accomplished by holding the tool stationary and turning the workpiece. Takes a variety of vertical, slanted and horizontal forms, and has one or more spindles. Typically a large, powerful machine, it can readily hold tolerances to 0.0001". See jig boring; lathe; turning machine.
- centers
centers
Cone-shaped pins that support a workpiece by one or two ends during machining. The centers fit into holes drilled in the workpiece ends. Centers that turn with the workpiece are called “live” centers; those that do not are called “dead” centers.
- computer numerical control ( CNC)
computer numerical control ( CNC)
Microprocessor-based controller dedicated to a machine tool that permits the creation or modification of parts. Programmed numerical control activates the machine’s servos and spindle drives and controls the various machining operations. See DNC, direct numerical control; NC, numerical control.
- flash
flash
Thin web or film of metal on a casting that occurs at die partings and around air vents and movable cores. This excess metal is due to necessary working and operating clearances in a die. Flash also is the excess material squeezed out of the cavity as a compression mold closes or as pressure is applied to the cavity.
- jig
jig
Tooling usually considered to be a stationary apparatus. A jig assists in the assembly or manufacture of a part or device. It holds the workpiece while guiding the cutting tool with a bushing. A jig used in subassembly or final assembly might provide assembly aids such as alignments and adjustments. See fixture.
- jig boring
jig boring
High-precision machining (a sophisticated form of milling) that originally pertained to jig and fixture manufacturing. Basic jig-boring processes include centering, drilling, reaming, through and step boring, counterboring and contouring.
- precision machining ( precision measurement)
precision machining ( precision measurement)
Machining and measuring to exacting standards. Four basic considerations are: dimensions, or geometrical characteristics such as lengths, angles and diameters of which the sizes are numerically specified; limits, or the maximum and minimum sizes permissible for a specified dimension; tolerances, or the total permissible variations in size; and allowances, or the prescribed differences in dimensions between mating parts.