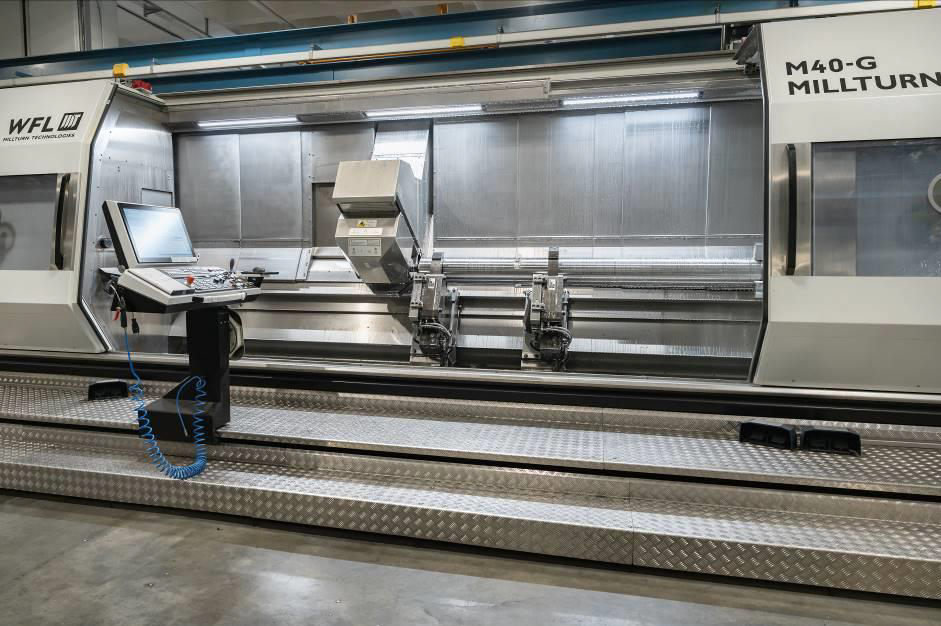
Mikrosan is a plastic extrusion line manufacturer, with its headquarters near Istanbul. The company was formed in 1978 by Naci Sönmez, hiring a small group of people.
Today, the company has more than 140 employees. Mikrosan operates two factories, the screw manufacturing is located in the main factory. All extrusion lines are manufactured and assembled in-house. In the headquarters, they also do assembly and the testing of the machines. The other factory is about 60 km away from the headquarters and in this factory, the assembly of the machine frames, as well as the painting of the components, is being done.
The company has about 20.000 square meters of production area in two factories. Another advantage of the company is that the nitriding (heat treatment) process is based in the factory, everything is done in-house. This is a specific advantage that Mikrosan is offering compared to the competition. Mikrosan’s products range from pipe extrusion lines and profile extrusion lines to granulation lines.
The company is producing especially for the plastics industry and the PVC market. Important products manufactured on extrusion machines are for example window profiles. Further products are PVC pipes, clean water pipes, pressure pipes, and granules. Mikrosan has already supplied more than 5000 extrusion lines all around the world so far, in more than 65 countries. The main markets are Turkey, Europe, the USA, and various Arabian Countries. The export rate is 60-70%, depending on the market conditions.
All from a single source
“Having the complete manufacturing process chain directly at Mikrosan is very important for us”, said Abdullah Demirci, technical manager. The core competence is the manufacturing of all the screws and barrels in-house, as customer requirements can be better fulfilled. Mikrosan is using a universal software “Unigraphics” to program screws and barrels.
“To make a good extruder you need to make a good screw. You need good software, you need a good machine, you need the good stuff. The universal software has the advantage that you are not limited with screw programming, you can use different machining strategies, depending on your machine and on your products,” said Demirci.
Mikrosan is using an M40-G Millturn with a 4,500 mm center distance and a swing of 520 mm for screw manufacturing. Important for Mikrosan’s decision for the WFL was the superior output and torque values of the spindle drives.
“The advantage of the WFL machine is the chuck and the tailstock function of the counter spindle. The size is perfect for us, because of the long center distance and the strength of the machine. It can easily handle different screws and barrels. The power of the turning spindle with up to 54 kW and the milling spindle with 33 kW was also an important point for us. WFL was from the very beginning the right partner. As far as communication is concerned, we had just one face, one contact person that we gave all the feedback within the project execution. So, the process was very easy for us”, Abdullah Demirci is describing.
The WFL is used for high precision machining operations as well as for pre-machining for screws and barrels. Middle-sized to big-sized screws are done on the WFL. The range size of screws machined on the WFL starts from just 90 mm in diameter.
With the WFL machine, Mikrosan achieves the manufacturing of a screw in only one clamping. The longest part ever produced on the machine was approximately 4000 mm. The usage of nitriding steels, with a DIN Norm of 1.8519/1.8550, is the industry standard of the market. Screws are normally made of 1.8519/1.8550 and barrels are made of 1.8550. After machining the workpieces they need heat treatment to harden the surface. In another step nitriding needs to be done, otherwise, the parts would have a very short lifetime.
“We have more than 250 extrusion line production capacity per year, one extrusion line includes at least 5 machines. That means we are producing more than 1000 machines per year”, said Demirci.
Versatility counts
“Now we are still learning and are still developing with the WFL. We are always adapting cutting strategies or creating new ones. The fact is that a lot of different screw and barrel geometries are being produced on the WFL machine. It is not a serial production, it always changes. Our software and the machine are capable of various designs. We are open to developing anything and the machine is capable of doing complex geometries of screws and barrels. So we can cover a wide range of parts. The 5-axis simultaneous machining cycle in the machine is a big advantage, this technology is especially used for manufacturing twin screws. When the geometry changes then you are getting a smooth transition with this cycle. This offers us continuous machining,” said Demirci.
Priority when choosing the new machine was the size of the machine. Furthermore, the structure of the machine was a big point why the machine has been bought. 5-axis simultaneous machining was one of the major requirements. The steady rest and the ability to clamp the part only one time was also important advantage.
WFL provided the postprocessor for the simple usage of the programs. That was a very critical issue. To run the machine as a turning machine as well as a milling machine the tailstock function of the counter spindle was very important.
For screw machining special steady rests are required because the parts are very slender. The length/diameter ratio is up to 40/1, so a special machine structure is needed, otherwise, there would be a risk of vibrations and the required good surface quality could not be achieved. For a good surface quality, it is also necessary that the clamping and workpiece support is very stable, and steady rests must be capable to move during machining operations. While moving the milling head, the steady rests are moving simultaneously, everything is synchronized with the milling head. This is a great advantage.
“After starting to work together our production times for screws and barrels have been reduced significantly. Furthermore, the delivery times decreased accordingly. However, we still see a potential for a further productivity increase, said Demirci.
The tool measuring in the machine is a big advantage. The machine compensates for the correct dimension by measuring the tool length by laser. Another advantage is the simulation software, Crashguard Studio. Before machining, we are using CrashGuard Studio to simulate the program. Possible collisions can already be detected in the programming phase. Operators can use the software on the machine and can therefore adapt the programs. WFL cycles are useful for easy machining. Furthermore, the CrashGuard anti-collision software protects the machines during machining and stops the machine even in case of operating errors. Additionally, Mikrosan is using the WFL software iControl Advanced to optimize and monitor the machining process.
Future steps
Mikrosan will continue to focus on its core competence. Being number one in the plastics industry with the manufacturing of screws and barrels is the major objective. In the future, some new investments will be done. The strategic location of Mikrosan as well as the fact that everything is done in-house is providing huge flexibility. Due to the special requirements of the customers, all the machines are tailor-made. This is a big advantage of Mikrosan.
Mikrosan’s machines are already prepared and ready for Industrie 4.0. Customers are starting to use the advantages of predictive maintenance. When companies have several extrusion lines in the factory they are always best informed about what is happening. “Planned stops are always better than an unplanned stop. Companies can act more consequently and can make provisions for the future.
Contact Details
Related Glossary Terms
- chuck
chuck
Workholding device that affixes to a mill, lathe or drill-press spindle. It holds a tool or workpiece by one end, allowing it to be rotated. May also be fitted to the machine table to hold a workpiece. Two or more adjustable jaws actually hold the tool or part. May be actuated manually, pneumatically, hydraulically or electrically. See collet.
- extrusion
extrusion
Conversion of an ingot or billet into lengths of uniform cross section by forcing metal to flow plastically through a die orifice.
- gang cutting ( milling)
gang cutting ( milling)
Machining with several cutters mounted on a single arbor, generally for simultaneous cutting.
- milling
milling
Machining operation in which metal or other material is removed by applying power to a rotating cutter. In vertical milling, the cutting tool is mounted vertically on the spindle. In horizontal milling, the cutting tool is mounted horizontally, either directly on the spindle or on an arbor. Horizontal milling is further broken down into conventional milling, where the cutter rotates opposite the direction of feed, or “up” into the workpiece; and climb milling, where the cutter rotates in the direction of feed, or “down” into the workpiece. Milling operations include plane or surface milling, endmilling, facemilling, angle milling, form milling and profiling.
- milling machine ( mill)
milling machine ( mill)
Runs endmills and arbor-mounted milling cutters. Features include a head with a spindle that drives the cutters; a column, knee and table that provide motion in the three Cartesian axes; and a base that supports the components and houses the cutting-fluid pump and reservoir. The work is mounted on the table and fed into the rotating cutter or endmill to accomplish the milling steps; vertical milling machines also feed endmills into the work by means of a spindle-mounted quill. Models range from small manual machines to big bed-type and duplex mills. All take one of three basic forms: vertical, horizontal or convertible horizontal/vertical. Vertical machines may be knee-type (the table is mounted on a knee that can be elevated) or bed-type (the table is securely supported and only moves horizontally). In general, horizontal machines are bigger and more powerful, while vertical machines are lighter but more versatile and easier to set up and operate.
- nitriding
nitriding
Introducing nitrogen into the surface layer of a solid ferrous alloy. This is done to increase hardness, wear resistance and fatigue strength.
- precision machining ( precision measurement)
precision machining ( precision measurement)
Machining and measuring to exacting standards. Four basic considerations are: dimensions, or geometrical characteristics such as lengths, angles and diameters of which the sizes are numerically specified; limits, or the maximum and minimum sizes permissible for a specified dimension; tolerances, or the total permissible variations in size; and allowances, or the prescribed differences in dimensions between mating parts.
- steady rest
steady rest
Supports long, thin or flexible work being turned on a lathe. Mounts on the bed’s ways and, unlike a follower rest, remains at the point where mounted. See follower rest.
- turning
turning
Workpiece is held in a chuck, mounted on a face plate or secured between centers and rotated while a cutting tool, normally a single-point tool, is fed into it along its periphery or across its end or face. Takes the form of straight turning (cutting along the periphery of the workpiece); taper turning (creating a taper); step turning (turning different-size diameters on the same work); chamfering (beveling an edge or shoulder); facing (cutting on an end); turning threads (usually external but can be internal); roughing (high-volume metal removal); and finishing (final light cuts). Performed on lathes, turning centers, chucking machines, automatic screw machines and similar machines.
- turning machine
turning machine
Any machine that rotates a workpiece while feeding a cutting tool into it. See lathe.