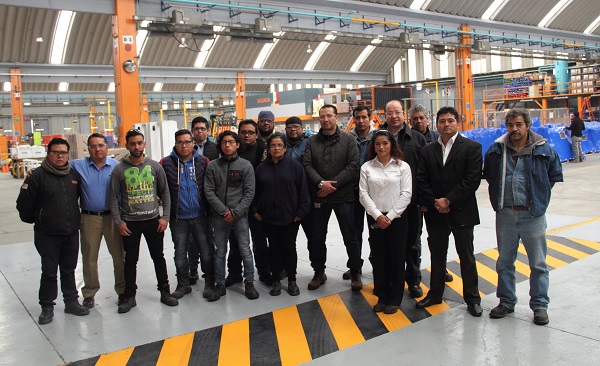
To support rapid expansion at its Mexico facility, the team at KUKA Automotive appointed Dormer Pramet its primary cutting tools supplier over the next three years. Working with local distributor CC Tools, Dormer Pramet will provide more than 150 standard round tools, special end mills and reamers, as well as indexable inserts and cutters.
KUKA Automotive is an international producer of intelligent automation solutions, with total sales of around three billion Euros and whose primary customers are from the automotive and general engineering industries.
KUKA Mexico is located in Toluca de Lerdo, just outside of Mexico City, and offers a broad range of highly modular robots, covering all common payload categories from 3kg to 1000kg. Currently, the KUKA Toluca de Lerdo facility has nine CNC machines, with eight conventional milling machines, one CNC lathe and two conventional lathes.
Another four machines will be arriving in early 2018. KUKA has work order contracts signed until 2022 and expects to double production in 2018 with a full floor of CNC machines by the end of 2019.
Dormer Pramet is a one-stop manufacturer of rotary and indexable drilling, milling, threading and turning tools. Market-leading brands include Precision Twist Drill (PTD), Union Butterfield, Dormer and Pramet.
The partnership includes several new and existing ranges from each of Dormer Pramet’s product brands. This includes the recently launched Dormer Force X drills and Dormer Shark Line material-specific taps.
Its product offer is enhanced with Dormer HSS A002 drills, Precision Twist Drill end mills and Pramet ADMX, LNGX and HNGX milling cutters and inserts. To further support the on-site demand, a full-service vending machine was placed into KUKA´s facility to optimize management of cutting tool inventory.
Going above and beyond in this partnership meant deeply engaging all parties to ensure optimal machining performance. KUKA and Dormer Pramet tested all tools in production environment conditions to guarantee the required service levels.
The Dormer Shark Line taps reduced more than two thirds of the tapping process, running from a previous 90 rpm up to a new optimal level of 620 rpm. The Pramet LNGX inserts performed 25 percent better than the incumbent tools, as well as providing a superior surface finish.
Also, the Pramet ZDCW inserts for high feed milling tremendously improved performance versus the current tooling, increasing performance by up to 200 percent.
Eduardo Medina, Director of Mexico Operations at KUKA Systems Mexico, said: “Although Dormer Pramet is a global cutting tool manufacturer with a wide product portfolio, the team were flexible to our needs and offered the personal touch to understand our processes and align the appropriate tools for optimal support.”
Both teams are excited to continually develop this relationship and grow together in future expansions.
“We are delighted to create this new partnership with KUKA,” stated Dormer Pramet’s Rosalba Iturbe, Territory Sales Manager, who along with Fernando Perez, Application Specialist, established the partnership.
Rosalba goes on to say: “From the initial discussions to successful field tests, we showed our strength as a simply reliable cutting tool partner capable of supporting KUKA now and into the future, as they continue to expand and grow.”
Contact Details
Related Glossary Terms
- computer numerical control ( CNC)
computer numerical control ( CNC)
Microprocessor-based controller dedicated to a machine tool that permits the creation or modification of parts. Programmed numerical control activates the machine’s servos and spindle drives and controls the various machining operations. See DNC, direct numerical control; NC, numerical control.
- conventional milling ( up milling)
conventional milling ( up milling)
Cutter rotation is opposite that of the feed at the point of contact. Chips are cut at minimal thickness at the initial engagement of the cutter’s teeth with the workpiece and increase to a maximum thickness at the end of engagement. See climb milling.
- feed
feed
Rate of change of position of the tool as a whole, relative to the workpiece while cutting.
- gang cutting ( milling)
gang cutting ( milling)
Machining with several cutters mounted on a single arbor, generally for simultaneous cutting.
- high-speed steels ( HSS)
high-speed steels ( HSS)
Available in two major types: tungsten high-speed steels (designated by letter T having tungsten as the principal alloying element) and molybdenum high-speed steels (designated by letter M having molybdenum as the principal alloying element). The type T high-speed steels containing cobalt have higher wear resistance and greater red (hot) hardness, withstanding cutting temperature up to 1,100º F (590º C). The type T steels are used to fabricate metalcutting tools (milling cutters, drills, reamers and taps), woodworking tools, various types of punches and dies, ball and roller bearings. The type M steels are used for cutting tools and various types of dies.
- lathe
lathe
Turning machine capable of sawing, milling, grinding, gear-cutting, drilling, reaming, boring, threading, facing, chamfering, grooving, knurling, spinning, parting, necking, taper-cutting, and cam- and eccentric-cutting, as well as step- and straight-turning. Comes in a variety of forms, ranging from manual to semiautomatic to fully automatic, with major types being engine lathes, turning and contouring lathes, turret lathes and numerical-control lathes. The engine lathe consists of a headstock and spindle, tailstock, bed, carriage (complete with apron) and cross slides. Features include gear- (speed) and feed-selector levers, toolpost, compound rest, lead screw and reversing lead screw, threading dial and rapid-traverse lever. Special lathe types include through-the-spindle, camshaft and crankshaft, brake drum and rotor, spinning and gun-barrel machines. Toolroom and bench lathes are used for precision work; the former for tool-and-die work and similar tasks, the latter for small workpieces (instruments, watches), normally without a power feed. Models are typically designated according to their “swing,” or the largest-diameter workpiece that can be rotated; bed length, or the distance between centers; and horsepower generated. See turning machine.
- milling
milling
Machining operation in which metal or other material is removed by applying power to a rotating cutter. In vertical milling, the cutting tool is mounted vertically on the spindle. In horizontal milling, the cutting tool is mounted horizontally, either directly on the spindle or on an arbor. Horizontal milling is further broken down into conventional milling, where the cutter rotates opposite the direction of feed, or “up” into the workpiece; and climb milling, where the cutter rotates in the direction of feed, or “down” into the workpiece. Milling operations include plane or surface milling, endmilling, facemilling, angle milling, form milling and profiling.
- payload ( workload)
payload ( workload)
Maximum load that the robot can handle safely.
- tapping
tapping
Machining operation in which a tap, with teeth on its periphery, cuts internal threads in a predrilled hole having a smaller diameter than the tap diameter. Threads are formed by a combined rotary and axial-relative motion between tap and workpiece. See tap.
- threading
threading
Process of both external (e.g., thread milling) and internal (e.g., tapping, thread milling) cutting, turning and rolling of threads into particular material. Standardized specifications are available to determine the desired results of the threading process. Numerous thread-series designations are written for specific applications. Threading often is performed on a lathe. Specifications such as thread height are critical in determining the strength of the threads. The material used is taken into consideration in determining the expected results of any particular application for that threaded piece. In external threading, a calculated depth is required as well as a particular angle to the cut. To perform internal threading, the exact diameter to bore the hole is critical before threading. The threads are distinguished from one another by the amount of tolerance and/or allowance that is specified. See turning.
- turning
turning
Workpiece is held in a chuck, mounted on a face plate or secured between centers and rotated while a cutting tool, normally a single-point tool, is fed into it along its periphery or across its end or face. Takes the form of straight turning (cutting along the periphery of the workpiece); taper turning (creating a taper); step turning (turning different-size diameters on the same work); chamfering (beveling an edge or shoulder); facing (cutting on an end); turning threads (usually external but can be internal); roughing (high-volume metal removal); and finishing (final light cuts). Performed on lathes, turning centers, chucking machines, automatic screw machines and similar machines.
- twist drill
twist drill
Most common type of drill, having two or more cutting edges, and having helical grooves adjacent thereto for the passage of chips and for admitting coolant to the cutting edges. Twist drills are used either for originating holes or for enlarging existing holes. Standard twist drills come in fractional sizes from 1¼16" to 11¼2", wire-gage sizes from 1 to 80, letter sizes A to Z and metric sizes.