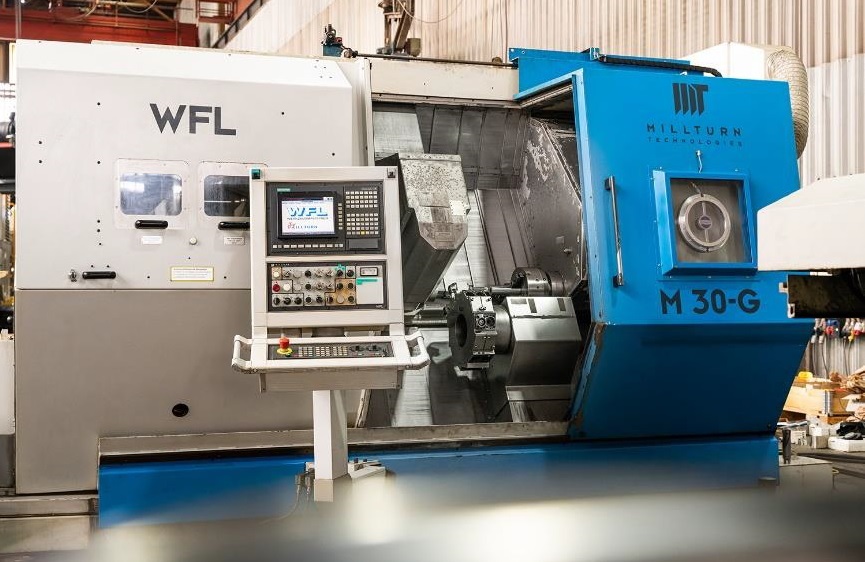
The M30 Millturn from WFL Millturn Technologies Inc. is one of the most popular and successful WFL machines in the extensive Millturn range. The classic Millturn complete machining centers ushered in a completely new era in their original version more than 25 years ago.
After all, this machine was the first WFL Millturn with an individual tool carrier for turning, drilling, and milling with a B-axis. Many of these old M30 machines are currently still in use. And when taken good care of, the oldest member of the Millturn family still delivers top performance even after many years. Ultimately, supreme quality and lasting accuracy are among the virtues of all WFL machines. We, therefore, decided to take the opportunity to take a closer look at one of these proto-Millturns.
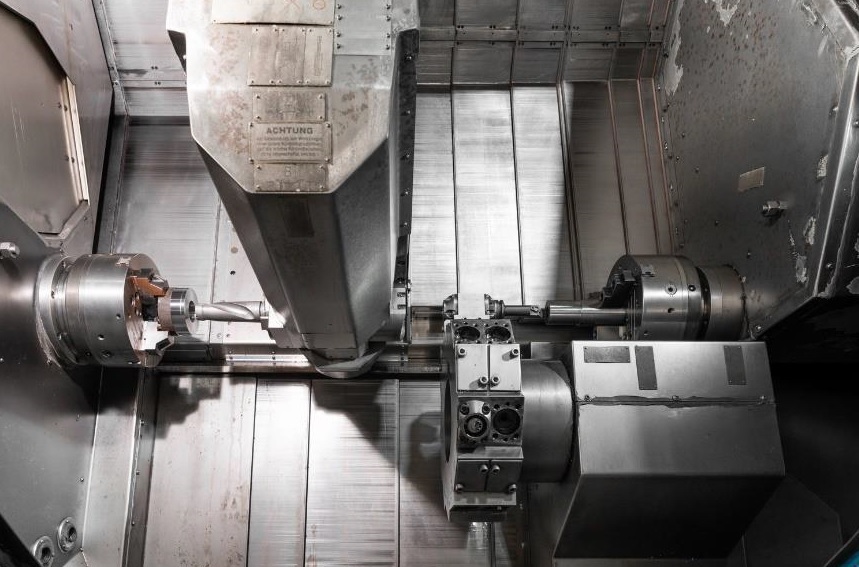
Although the details of the current design have very little in common with its original version, the basic structure with the stable 60° slant bed is still there. Particularly noteworthy features include the powerful headstock with a 37 kW main drive and 2-speed gearbox and an external C-axis. Although the design dates back to the earlier Voest-Alpine WNC slant bed machines, it is still used in the latest Millturn models of the M35, M40, and M50 series with modernized drive motors. Water-cooled direct drives are available as alternatives nowadays.
The first machines in the M30 series still had a 24-space magazine with an automatic tool changer permanently mounted on the milling unit. Back then, it was a reliable and practical solution.
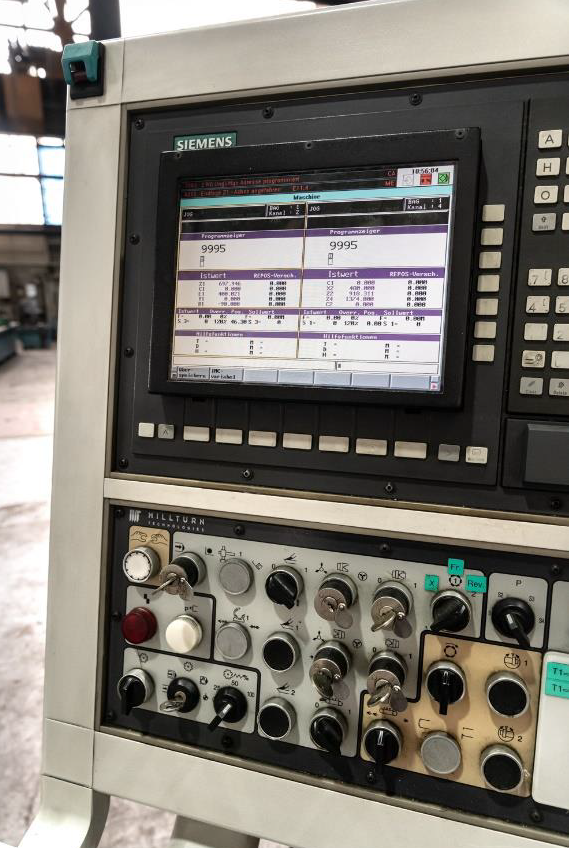
But soon, this magazine was replaced by an external magazine over the left-hand headstock that was much easier to operate and had an initial capacity of 48 tool stations, which was a lot back then. This made setting up the tools parallel to machining time possible for the first time. The capacity was then expanded to up to 96 tool stations. Modular systems such as HSK50, Capto C4, and KM50 were already available as tool systems.
Due to the higher power and stricter stability requirements, the system size had to be increased to HSK63 or Capto C6 for the current models. Even back then, the machine was offered an optional lower 2x24 disc turret and counter spindle.
The Siemens Sinumerik 880T was initially used as the control system for the first machines. The data memories of this control system were still in EPROM form and were therefore only writeable and erasable with a special device. The newer machines made back then were then delivered with the Sinumerik 840 C. This version already had a hard drive for data storage.
Depending on the configuration, the machine had up to 9 NC machining axes and could perform 5-axis interpolations. However, due to the lack of corresponding software solutions for the programming, this was a difficult and laborious undertaking back then. Thanks to the B-axis with 7.5 kW milling drive and 4,000 rpm, complex and highly precise oblique machining was possible with high productivity.
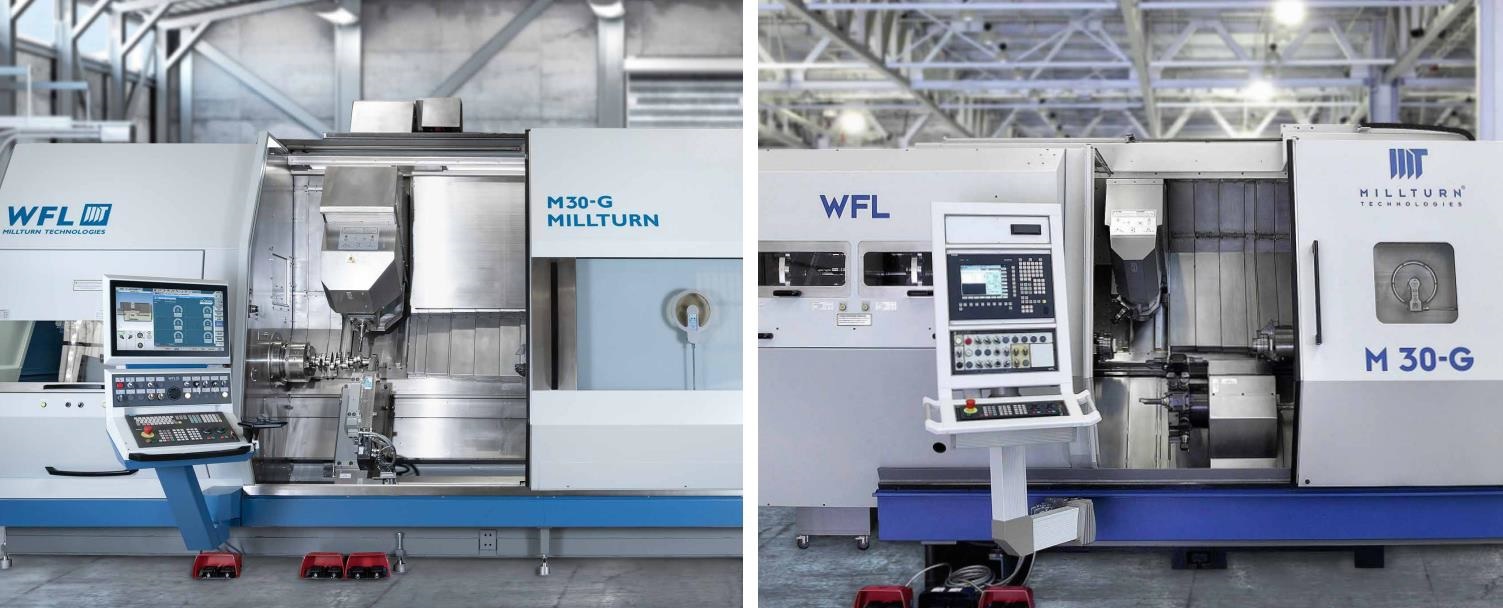
At the time, a new feature was the use of a compressor cooling unit to stabilize the temperature of the turning-boring-milling unit. This made it possible to perform lengthy milling operations with a high output. However, the high continuous speeds were the Achilles’ heel of the turning-boring-milling unit, because the permanent grease lubrication was simply not sufficient.
It was only with the newer models – which featured oil mist lubrication – that this problem was solved. But, so what, even back then it was possible to use large milling cutters and drills even for heavy roughing cuts since the milling unit achieved maximum performance even at lower speeds due to the gearbox design. When it came to turning, the machines were unbeatable anyway. The machines were predominantly used in the aerospace industry, the automotive sector, for hydraulic components, in the demanding field of mechanical engineering as well as in tool manufacture and medical technology. Typical areas of application were complex precision parts made of materials that are difficult to machine.
The successor models still benefit today from the experience gained from the large number of customer requests granted over several decades. The expectations placed on WFL are accordingly high. Ultimately, the machine is the means for exploiting all technological possibilities to the maximum. Then, as of now, technological innovations require a solid foundation.
Contact Details
Related Glossary Terms
- centers
centers
Cone-shaped pins that support a workpiece by one or two ends during machining. The centers fit into holes drilled in the workpiece ends. Centers that turn with the workpiece are called “live” centers; those that do not are called “dead” centers.
- gang cutting ( milling)
gang cutting ( milling)
Machining with several cutters mounted on a single arbor, generally for simultaneous cutting.
- milling
milling
Machining operation in which metal or other material is removed by applying power to a rotating cutter. In vertical milling, the cutting tool is mounted vertically on the spindle. In horizontal milling, the cutting tool is mounted horizontally, either directly on the spindle or on an arbor. Horizontal milling is further broken down into conventional milling, where the cutter rotates opposite the direction of feed, or “up” into the workpiece; and climb milling, where the cutter rotates in the direction of feed, or “down” into the workpiece. Milling operations include plane or surface milling, endmilling, facemilling, angle milling, form milling and profiling.
- numerical control ( NC)
numerical control ( NC)
Any controlled equipment that allows an operator to program its movement by entering a series of coded numbers and symbols. See CNC, computer numerical control; DNC, direct numerical control.
- parallel
parallel
Strip or block of precision-ground stock used to elevate a workpiece, while keeping it parallel to the worktable, to prevent cutter/table contact.
- turning
turning
Workpiece is held in a chuck, mounted on a face plate or secured between centers and rotated while a cutting tool, normally a single-point tool, is fed into it along its periphery or across its end or face. Takes the form of straight turning (cutting along the periphery of the workpiece); taper turning (creating a taper); step turning (turning different-size diameters on the same work); chamfering (beveling an edge or shoulder); facing (cutting on an end); turning threads (usually external but can be internal); roughing (high-volume metal removal); and finishing (final light cuts). Performed on lathes, turning centers, chucking machines, automatic screw machines and similar machines.