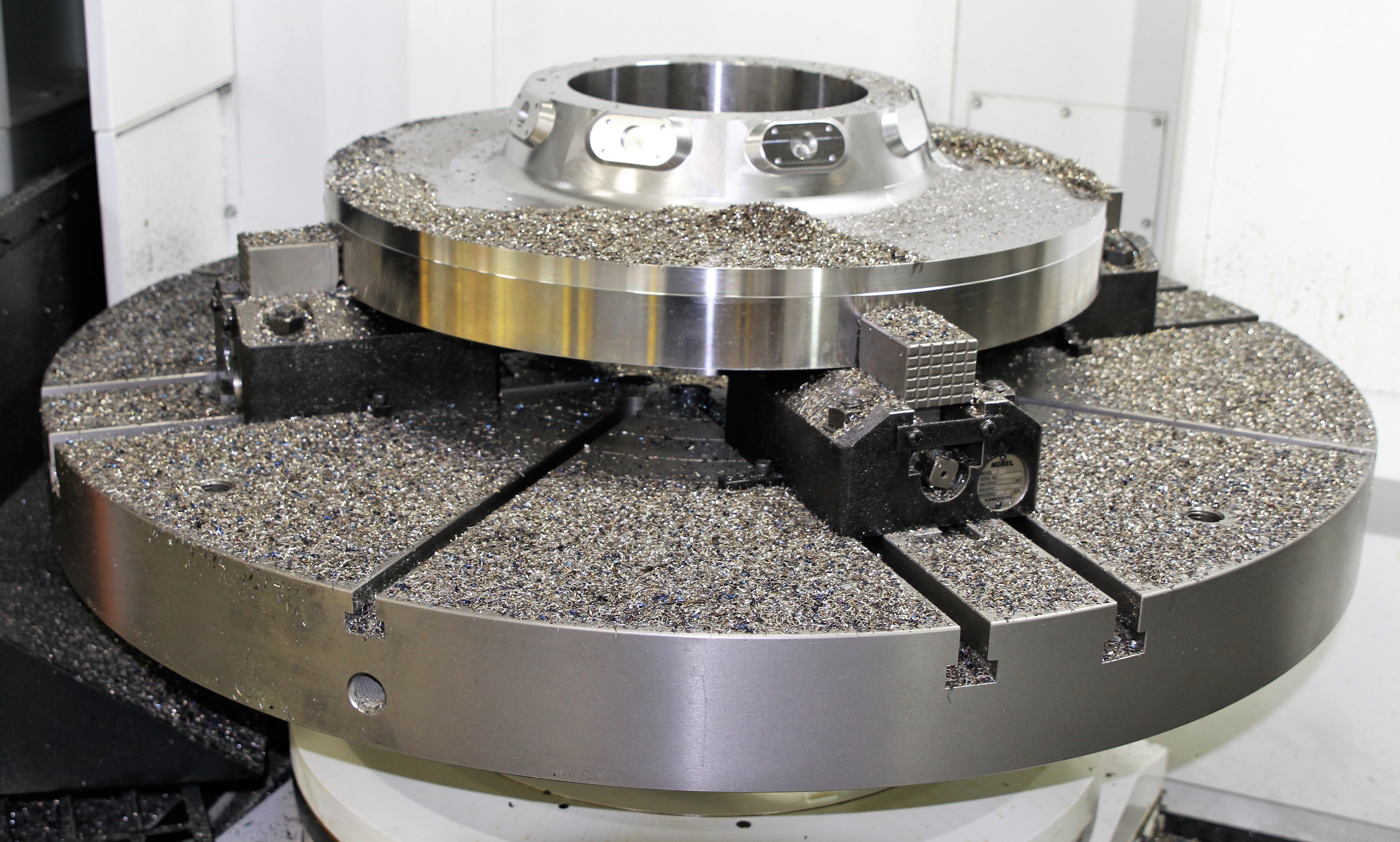
Schaumburg, IL – August 13, 2018 – Kitagawa NorthTech, Inc., a specialist in Standard Power Chucks, Advanced and Custom Engineered Workholding, has acquired the exclusive distribution, sales and marketing rights for Kawatatec Nobel branded chucks for North America. Due to their rugged build and extremely large size, the Nobel brand of Chucks now available from Kitagawa NorthTech have become synonymous with Oil & Gas industry applications over the last three decades. Nobel Chucks are popular in oil and gas country applications because of their unique features, forged steel bodies, large bore size, time-tested performance and reliability in these demanding applications.
Available up to 3.5 Meters (11.48’) in size, Kitagawa NorthTech’s Nobel Chucks, Face Plates and Oil Country Chucks Serve a Wide Range of Applications
The Nobel Large Power, Manual & Special VTL Face Plates and Chucks are designed for Large Bearing, Aerospace, Power Generation and large Commercial work, while the Nobel Oil Country Chucks are uniquely suited for Down-Hole Drilling, Instrumentation, Fracking & Refining.
Kitagawa NorthTech Nobel Chucks are also available in a wide assortment of sizes, styles and configurations including large Face Plates with Boring Mill Jaws, manual Independent 4 Jaw, 3 Jaw Scroll, Power Combination Chucks, Indexing Chucks, Pull Down Chucks and Special Application 6 Jaw 2+2+2 Chucks for thin wall machining up to 3.5 meters. The Kitagawa NorthTech Nobel Special Large Bore Oil and Gas Chucks up to 42” diameter can handle spindle pass through of up to 14.5” diameter.
Kevin Bennett, VP of Sales & Marketing adds, “Kitagawa and Kawatatec are two like-minded companies. We both share a similar heritage and approach to design, manufacturing principles and quality standards, so we believed the Nobel brand to be an excellent addition to join our ever expanding family of Workholding Solutions. Our comprehensive family also includes, standard, advanced and engineered workholding and custom engineered workholding solutions for rotational, stationary, grinding, turning and milling. Acquiring the Nobel brand distribution rights for North America also reinforces our vision and promise to customers to be their turnkey workholding supplier in North America.”
Kitagawa NorthTech earlier this year absorbed ITEX Workholding operations, which previously held the distribution rights for Nobel Chucks in North America. Principal of ITEX, Mike Roberts joined Kitagawa NorthTech, Inc to provide continuity in selling Nobel products, along with his tremendous knowledge and breadth of oil & gas industry experience. He currently serves as Regional Sales Manager for Kitagawa NorthTech throughout the Southwest.
Nobel Brand Chucks from Kitagawa NorthTech Complete Large Diameter VTL Workholding Offering
With the addition of Nobel brand chucks, Kitagawa NorthTech offers the most comprehensive family of VTL Workholding solutions available in the industry. The family includes Manual and Power Wrench Scroll Chucks, 4 Jaw Independent Chucks, Incredibly Large 6 Jaw Pin Arbor PullDown Chucks, Large 6 Jaw 2+2+2 Thin Wall Ring Application Chucks, Combination Power/Boring Mill Jaw Chucks and Face Plates with Boring Mill Jaws. They also offer Large Manual and Hydraulic Part Specific VTL Turning Fixtures.
Contact Details
Related Glossary Terms
- arbor
arbor
Shaft used for rotary support in machining applications. In grinding, the spindle for mounting the wheel; in milling and other cutting operations, the shaft for mounting the cutter.
- boring
boring
Enlarging a hole that already has been drilled or cored. Generally, it is an operation of truing the previously drilled hole with a single-point, lathe-type tool. Boring is essentially internal turning, in that usually a single-point cutting tool forms the internal shape. Some tools are available with two cutting edges to balance cutting forces.
- gang cutting ( milling)
gang cutting ( milling)
Machining with several cutters mounted on a single arbor, generally for simultaneous cutting.
- grinding
grinding
Machining operation in which material is removed from the workpiece by a powered abrasive wheel, stone, belt, paste, sheet, compound, slurry, etc. Takes various forms: surface grinding (creates flat and/or squared surfaces); cylindrical grinding (for external cylindrical and tapered shapes, fillets, undercuts, etc.); centerless grinding; chamfering; thread and form grinding; tool and cutter grinding; offhand grinding; lapping and polishing (grinding with extremely fine grits to create ultrasmooth surfaces); honing; and disc grinding.
- milling
milling
Machining operation in which metal or other material is removed by applying power to a rotating cutter. In vertical milling, the cutting tool is mounted vertically on the spindle. In horizontal milling, the cutting tool is mounted horizontally, either directly on the spindle or on an arbor. Horizontal milling is further broken down into conventional milling, where the cutter rotates opposite the direction of feed, or “up” into the workpiece; and climb milling, where the cutter rotates in the direction of feed, or “down” into the workpiece. Milling operations include plane or surface milling, endmilling, facemilling, angle milling, form milling and profiling.
- milling machine ( mill)
milling machine ( mill)
Runs endmills and arbor-mounted milling cutters. Features include a head with a spindle that drives the cutters; a column, knee and table that provide motion in the three Cartesian axes; and a base that supports the components and houses the cutting-fluid pump and reservoir. The work is mounted on the table and fed into the rotating cutter or endmill to accomplish the milling steps; vertical milling machines also feed endmills into the work by means of a spindle-mounted quill. Models range from small manual machines to big bed-type and duplex mills. All take one of three basic forms: vertical, horizontal or convertible horizontal/vertical. Vertical machines may be knee-type (the table is mounted on a knee that can be elevated) or bed-type (the table is securely supported and only moves horizontally). In general, horizontal machines are bigger and more powerful, while vertical machines are lighter but more versatile and easier to set up and operate.
- turning
turning
Workpiece is held in a chuck, mounted on a face plate or secured between centers and rotated while a cutting tool, normally a single-point tool, is fed into it along its periphery or across its end or face. Takes the form of straight turning (cutting along the periphery of the workpiece); taper turning (creating a taper); step turning (turning different-size diameters on the same work); chamfering (beveling an edge or shoulder); facing (cutting on an end); turning threads (usually external but can be internal); roughing (high-volume metal removal); and finishing (final light cuts). Performed on lathes, turning centers, chucking machines, automatic screw machines and similar machines.