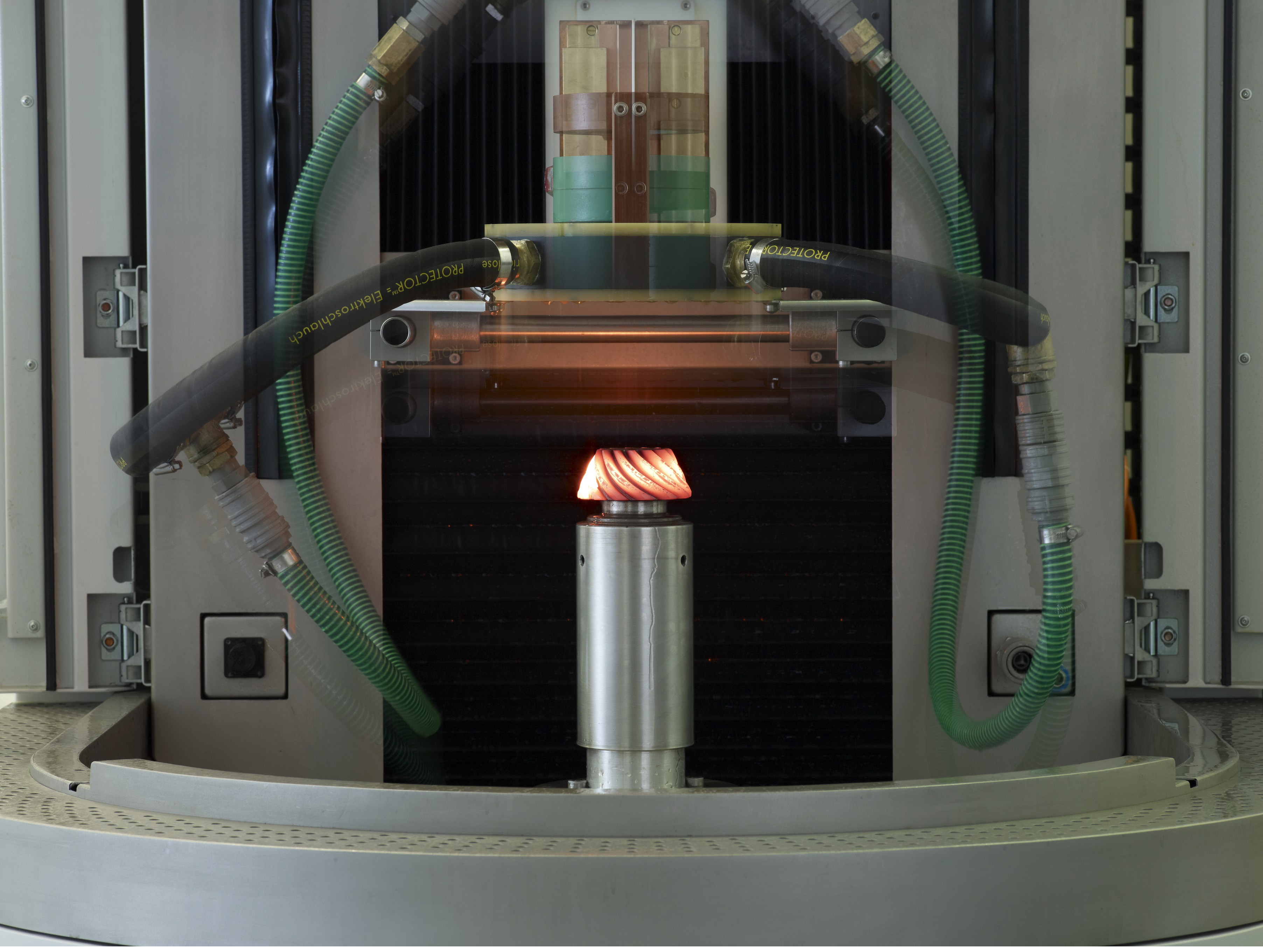
Article from EMAG
EMAG LLC announces its plans to hold its annual Technology Days at the North American headquarters in Farmington Hills, Mich., June 6-7. On June 6, the event will run from noon til 9 p.m. On June 7, from 8 a.m. til 2:30 p.m. The event will include a variety of machine tools under power for live demonstrations, plus a series of technical and market presentations by industry experts from the company.
Topics will cover all the machining and joining technologies EMAG brings to the market, including vertical milling, ECM, laser and induction hardening. The keynote presentations will be a discussion of innovative propulsion systems on June 6 and E-mobility trends and their impact on the traditional manufacturing landscape in the automotive supply chain on June 7. The event will be led by CEO of EMAG LLC for North America, Peter Loetzner. Other featured speakers will be Michael Robinet from HIS Markit and Brett Smith from the Center for Automotive Research.
All interested parties are welcome to attend this event, at no cost. To register, please visit: techdays.emag.com. This microsite contains the full agenda of presentations, as well as the complete list of the equipment being demonstrated.
Day one presentations on June 6 will cover material science and technology, while day two on June 7 will emphasize machining and assembly.
During the event, a variety of production machine tools will be on display for live demonstrations or full inspection, including:
VT 4 Vertical Lathe - Short cycle times, high precision and safe processing for shaft machining in the power transmission area. Short chip-to-chip times in 4-axis machining, workpiece grippers on two turrets and the EMAG vertical alignment technology that eliminates chip clusters in the machining area highlight this VMC.
VL 4 Vertical Turning Machine - Increased flexibility and diverse manufacturing capabilities for soft and hard machining of components up to 200mm diameters are offered by this advanced machine design. Interlinking of multiple machines for full production automation is also made possible with the flexible conveyor and workpiece chucking arrangements.
VL 3 DUO Multi-Spindle Machine - This CNC machine is an efficient twin-spindle machine solution for chucked parts up to 150mm in diameter and expands the EMAG offering in its VL Series. Each work area has its own spindle for independent operation and each tool turret has 12 positions, which can be loaded with live or static tools. Features EMAG TrackMotion for full automation, including part flipping between OP 10 and OP 20.
VSC 400 Combined Turning and Grinding Center - Vertical turning and grinding in one machine, in a single setup. Other modules can be attached for full turning, drilling, milling, grinding and even honing or hardening. Typical workpieces include gearwheels, chain wheels, sliding sleeves, CVT parts, conrods, rocker arms, bearing and piston rings. The small footprint machine design virtually eliminates the need for gantry loaders.
Also being shown in live demo mode is the EMAG MIND-M 250 (pictured), a compact modular induction hardening machine.
EMAG engineers will be available to discuss the machines, the technologies and the Industry 4.0 services offered by the company.
Related Glossary Terms
- computer numerical control ( CNC)
computer numerical control ( CNC)
Microprocessor-based controller dedicated to a machine tool that permits the creation or modification of parts. Programmed numerical control activates the machine’s servos and spindle drives and controls the various machining operations. See DNC, direct numerical control; NC, numerical control.
- electrochemical machining ( ECM)
electrochemical machining ( ECM)
Operation in which electrical current flows between a workpiece and conductive tool through an electrolyte. Initiates a chemical reaction that dissolves metal from the workpiece at a controlled rate. Unlike with traditional cutting methods, workpiece hardness is not a factor, making ECM suitable for difficult-to-machine materials. Takes such forms as electrochemical grinding, electrochemical honing and electrochemical turning.
- gang cutting ( milling)
gang cutting ( milling)
Machining with several cutters mounted on a single arbor, generally for simultaneous cutting.
- grinding
grinding
Machining operation in which material is removed from the workpiece by a powered abrasive wheel, stone, belt, paste, sheet, compound, slurry, etc. Takes various forms: surface grinding (creates flat and/or squared surfaces); cylindrical grinding (for external cylindrical and tapered shapes, fillets, undercuts, etc.); centerless grinding; chamfering; thread and form grinding; tool and cutter grinding; offhand grinding; lapping and polishing (grinding with extremely fine grits to create ultrasmooth surfaces); honing; and disc grinding.
- hardening
hardening
Process of increasing the surface hardness of a part. It is accomplished by heating a piece of steel to a temperature within or above its critical range and then cooling (or quenching) it rapidly. In any heat-treatment operation, the rate of heating is important. Heat flows from the exterior to the interior of steel at a definite rate. If the steel is heated too quickly, the outside becomes hotter than the inside and the desired uniform structure cannot be obtained. If a piece is irregular in shape, a slow heating rate is essential to prevent warping and cracking. The heavier the section, the longer the heating time must be to achieve uniform results. Even after the correct temperature has been reached, the piece should be held at the temperature for a sufficient period of time to permit its thickest section to attain a uniform temperature. See workhardening.
- induction hardening
induction hardening
Surface-hardening process in which only the surface layer of a suitable ferrous workpiece is heated by electromagnetic induction to above the upper critical temperature and immediately quenched.
- lathe
lathe
Turning machine capable of sawing, milling, grinding, gear-cutting, drilling, reaming, boring, threading, facing, chamfering, grooving, knurling, spinning, parting, necking, taper-cutting, and cam- and eccentric-cutting, as well as step- and straight-turning. Comes in a variety of forms, ranging from manual to semiautomatic to fully automatic, with major types being engine lathes, turning and contouring lathes, turret lathes and numerical-control lathes. The engine lathe consists of a headstock and spindle, tailstock, bed, carriage (complete with apron) and cross slides. Features include gear- (speed) and feed-selector levers, toolpost, compound rest, lead screw and reversing lead screw, threading dial and rapid-traverse lever. Special lathe types include through-the-spindle, camshaft and crankshaft, brake drum and rotor, spinning and gun-barrel machines. Toolroom and bench lathes are used for precision work; the former for tool-and-die work and similar tasks, the latter for small workpieces (instruments, watches), normally without a power feed. Models are typically designated according to their “swing,” or the largest-diameter workpiece that can be rotated; bed length, or the distance between centers; and horsepower generated. See turning machine.
- milling
milling
Machining operation in which metal or other material is removed by applying power to a rotating cutter. In vertical milling, the cutting tool is mounted vertically on the spindle. In horizontal milling, the cutting tool is mounted horizontally, either directly on the spindle or on an arbor. Horizontal milling is further broken down into conventional milling, where the cutter rotates opposite the direction of feed, or “up” into the workpiece; and climb milling, where the cutter rotates in the direction of feed, or “down” into the workpiece. Milling operations include plane or surface milling, endmilling, facemilling, angle milling, form milling and profiling.
- turning
turning
Workpiece is held in a chuck, mounted on a face plate or secured between centers and rotated while a cutting tool, normally a single-point tool, is fed into it along its periphery or across its end or face. Takes the form of straight turning (cutting along the periphery of the workpiece); taper turning (creating a taper); step turning (turning different-size diameters on the same work); chamfering (beveling an edge or shoulder); facing (cutting on an end); turning threads (usually external but can be internal); roughing (high-volume metal removal); and finishing (final light cuts). Performed on lathes, turning centers, chucking machines, automatic screw machines and similar machines.
- turning machine
turning machine
Any machine that rotates a workpiece while feeding a cutting tool into it. See lathe.