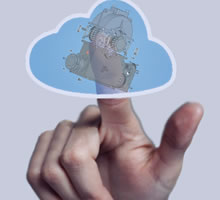
Every day, it happens. Someone from Houston calls, or maybe San Francisco, peddling precision-machined parts from China. Then there are the emails from people with fake names—like Lily, Annie and Susan—overflowing my inbox with offers of low part costs and excellent service. Please, China, I don’t want to buy machined parts from you. No metal stampings. No plastic injection molds or 3D-printed prototypes. And at the risk of offending those who do, you shouldn’t either.
I’m not here to bash China. I’ve visited manufacturing plants there. The ones that I saw were clean and efficient, their workers every bit as dedicated as those in this country. And I’ve worked with companies that were outsourcing many of their higher-volume products to Asia. For the most part, the costs were lower and the quality was acceptable, with a few exceptions. While lead times weren’t great, proper sales forecasting and production planning made the supply chain manageable. Those same statements can be made about Mexico, Romania, Brazil and other countries where labor costs are substantially lower than here in the U.S.
So what’s wrong with buying manufactured products from other countries? Call me old-fashioned or naïve, but America is a country built on manufacturing. As someone who once stood in front of a machine tool all day, I lament the loss of American-made Huffy bicycles. Our Radio Flyers have gone overseas. So too have the Hot Wheels I played with as a kid. Dell computers. Vending machines. Dinner flatware. Airplanes and automobiles. It’s a long list made largely of companies that over the past two decades succumbed to pressure from stockholders and board members to increase profit margins.
Now you might call me cynical. I blame our elected officials—pretty much all of them—but factory management, corporate investors, the economy and even consumers (maybe especially consumers) deserve some finger pointing as well. But setting all that aside, what’s important is how we go about fixing it.
I’m not suggesting we go back to the labor-intensive manufacturing methods of my youth. Automation and CNC machine tools have changed all that. And even if the companies I just picked on were to bring all that manufacturing back to U.S. shores, where would they find the workers?
In fact, that’s the whole point of this diatribe. Isn’t it time for us as American manufacturing people to embrace efficiency and leverage the skilled, talented people we already have in place to make our production levels sing?
Think your shop is already doing a good job? Maybe so, but answer these questions: What’s honestly your machine overall equipment effectiveness? Are you setting tools offline? Do you use quick-change tooling? How about machine probing, shop-floor vending systems, balancing machines, high-pressure coolant and toolpath simulation? I won’t even get started on the industrial internet of things and Industry 4.0, which, as I said in my previous post, may spell doom for more than a few shops. The point is that there’s so much more we could be doing to improve our manufacturing operations, yet it seems that a large percentage of shops don’t take advantage of the available technology. Please tell me I’m wrong.
Over the past 6 years, I’ve interviewed more than 1,500 people, from CEOs and machine operators to cutting tool suppliers and equipment salespeople. Most of them agree on one thing: The majority of shops have a long way to go in the efficiency department. Let’s get with the program, people, and not give anyone a reason to take more of our manufacturing overseas. Now’s the time to do it.
Related Glossary Terms
- computer numerical control ( CNC)
computer numerical control ( CNC)
Microprocessor-based controller dedicated to a machine tool that permits the creation or modification of parts. Programmed numerical control activates the machine’s servos and spindle drives and controls the various machining operations. See DNC, direct numerical control; NC, numerical control.
- coolant
coolant
Fluid that reduces temperature buildup at the tool/workpiece interface during machining. Normally takes the form of a liquid such as soluble or chemical mixtures (semisynthetic, synthetic) but can be pressurized air or other gas. Because of water’s ability to absorb great quantities of heat, it is widely used as a coolant and vehicle for various cutting compounds, with the water-to-compound ratio varying with the machining task. See cutting fluid; semisynthetic cutting fluid; soluble-oil cutting fluid; synthetic cutting fluid.
- sawing machine ( saw)
sawing machine ( saw)
Machine designed to use a serrated-tooth blade to cut metal or other material. Comes in a wide variety of styles but takes one of four basic forms: hacksaw (a simple, rugged machine that uses a reciprocating motion to part metal or other material); cold or circular saw (powers a circular blade that cuts structural materials); bandsaw (runs an endless band; the two basic types are cutoff and contour band machines, which cut intricate contours and shapes); and abrasive cutoff saw (similar in appearance to the cold saw, but uses an abrasive disc that rotates at high speeds rather than a blade with serrated teeth).
- toolpath( cutter path)
toolpath( cutter path)
2-D or 3-D path generated by program code or a CAM system and followed by tool when machining a part.