Manufacturers of machined metal parts leave money on the table when leaving coolant on chips.
For example, if a manufacturer sends a typical scrap shipment of about 18,144 kg (40,000 lbs.) of coolant-laden chips to a recycler, about 20% of the weight is moisture, said Mike Hook, director of sales and marketing at Kalamazoo, Michigan-based Prab Inc., which makes equipment to move scrap metal chips and convert them to dry chips or compact briquettes. That equals about 3,629 kg (8,000 lbs.) of fluid, or roughly 3,785 L (1,000 gal.), because coolant weighs about 3.6 kg (8 lbs.) per gallon.
“That has to be disposed of by the recycler and hauled by the hauler,” he said. “And you lose all the value of that in terms of coolant that could be reused, so you have to buy 1,000 gal. of new coolant to replace it.”
Hook said scrap recyclers usually accept coolant-laden chips but back-charge a customer to handle and dispose of the fluid.
“Dry, reduced metal scrap is going to be the most valuable to the recycler,” he said.
Additionally, Hook said legislation makes a part manufacturer responsible for coolant from cradle to grave, so a hauler isn’t liable if coolant leaks or otherwise escapes from a container during transport.
Protecting the Planet
Not only is metalworking fluid a significant expense for part manufacturers and a rising one as the petroleum and other products needed to make it increase in cost, but the environmental protection regulations for scrap and fluid disposal continue to become stricter and pricier when violated, said Justin Viner, regional sales manager for Knoll America Inc. The Madison Heights, Michigan-based company, which is building a new headquarters in Dallas, North Carolina, also offers a wide range of equipment for central chip handling systems, including conveyors, pumps, coolant filtration, shredders, centrifuges and briquetters.
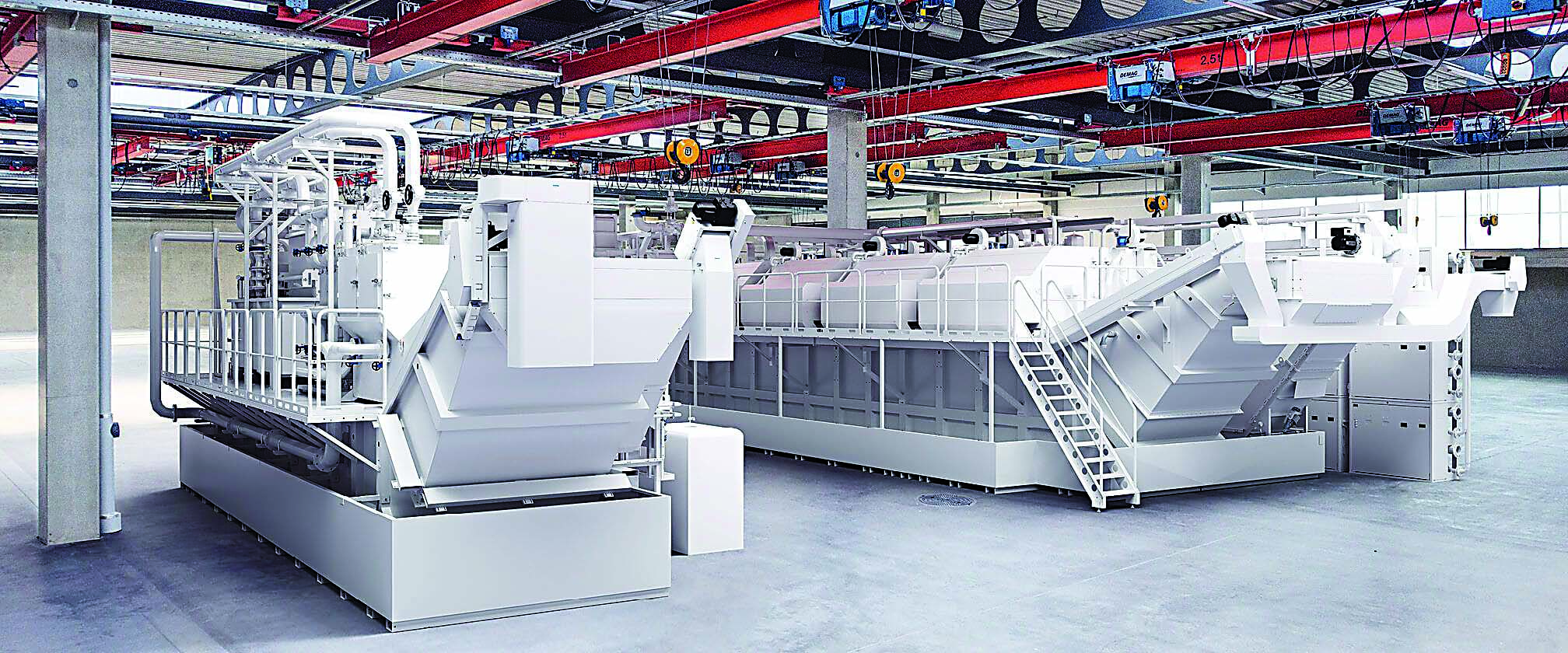
“The cleaner the chips are, the better it is to get rid of them,” he said, either by recycling or disposing of them.
Viner said an automated central chip handling system enables chip processing to be performed outside a production area, enhancing worker safety.
Using conveyors and sensors, he said the system is automated until the stage at which chips are dumped into containers.
“You can have robots even at that point to reduce personnel costs and remove the chips into containers,” Viner said.
Nonetheless, he said it’s easier to integrate an automated central system when machining centers are installed before rather than after.
“Sometimes it is an afterthought for companies,” Viner said.
Hook explained that creating a central system traditionally involved setting machine tools along a trench into which chips and fluid are conveyed to a centrifuge to wring out the fluid or to a briquetter to squeeze out the fluid and turn the chips into pucks before sending filtered fluid back to the machines and the scrap to trailers.
“It’s very simple and effective,” he said.
In addition to mechanical conveyors, Hook said material can be conveyed pneumatically to more efficiently transport it longer distances, which is especially
beneficial for newer modular shop layouts where companies adjust production processes based on changing workflow.
“The flexible automation makes a lot of sense,” he said.
Hook said electronic automation also plays a role in chip handling systems, allowing end users to communicate with partner organizations. This capability enables a system, for example, to tell a scrap dealer that bins are full and need to be collected.
Working with sister company KMC Global Controls & Automation in Kalamazoo, he said Prab offers an Industrial Internet of Things option for chip handling systems that monitors parameters, such as run times and downtimes, and sends data to customers so they can use it in Industry 4.0 initiatives.
“Some of this technology gets into predictive maintenance,” Hook said, “where we have sensors that will sense precursors to failure to make sure the equipment is serviced prior to it breaking down.”
Drying Out
Fundamental to an automated central chip handling system is a wringer/centrifuge or briquetter. Prab reports that its centrifuges and briquetters reclaim up to 99% of metalcutting fluids while saving space.
“Our equipment has proved to reduce scrap volume up to 90%,” said Marketing Coordinator Jack Gould. “The oil savings is a big part of it as well, especially with a centrifugal wringer system.”
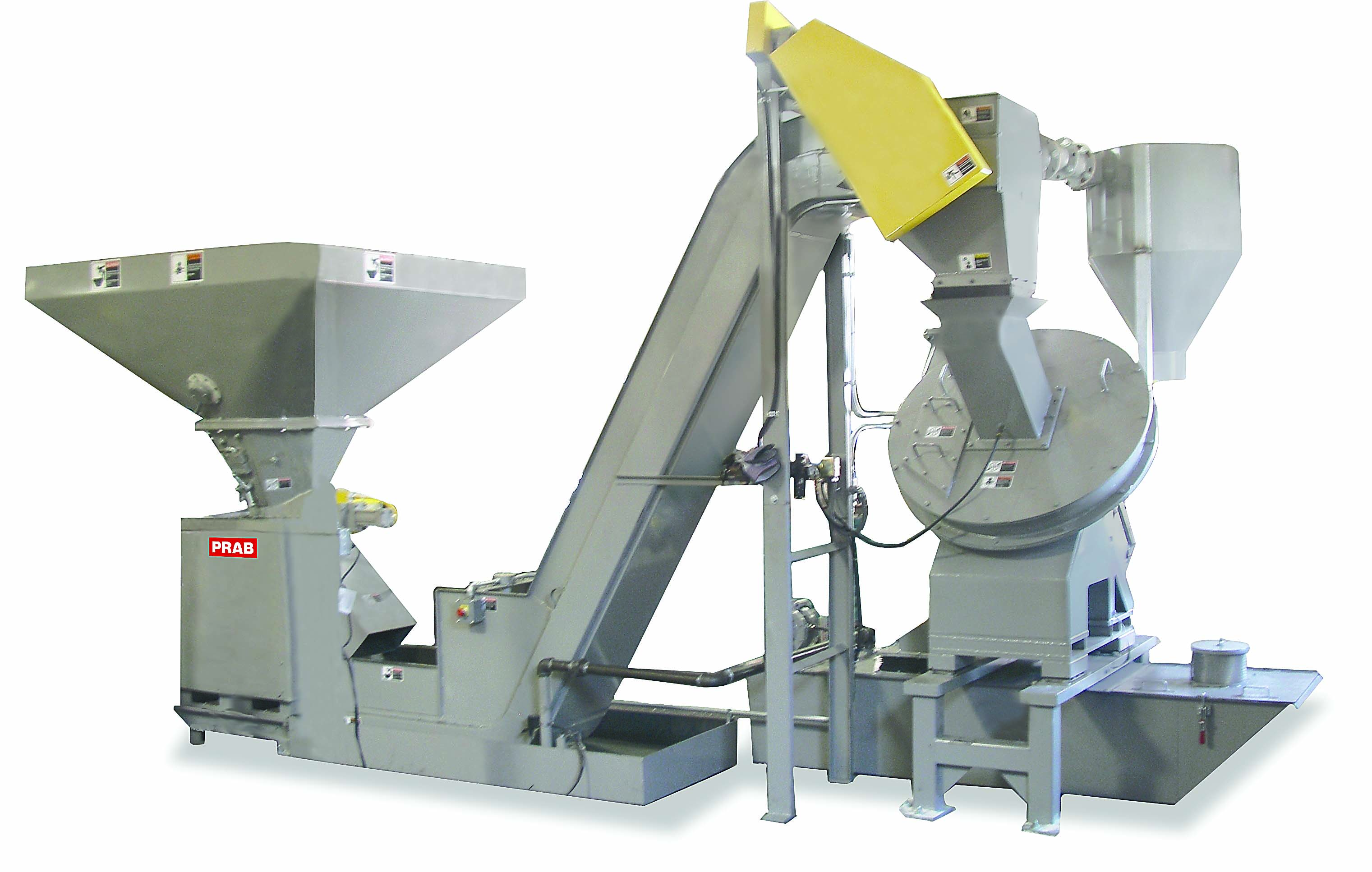
He said briquetted pucks are slightly cleaner than loose chips, are easier to transport and enable more efficient re-melts. As a result, recyclers frequently pay more for pucks than dry chips. He offered the example of a customer, Martin-Baker America Inc., which received 17 cents more per pound for briquettes than loose chips.
“The briquetter can increase scrap value up to 25%,” Gould said. “That adds up quickly.”
Viner pointed out that some metals, such as magnesium, must be pressed because the material is flammable and compacting prevents chips from igniting. In addition, grinding slurry is well suited for pressing, he said. Knoll America offers the MicroPur reversible flow filter for separating superfine impurities from oils, and an ideal application is grinding carbide and high-speed steel cutting tools.
He said briquetting is suitable for central systems, which usually service at least 30 machines, rather than stand-alone machines.
Hook said companies that have their own re-melt facilities, such as die casters that both cast metal and perform secondary machining operations, can benefit from wringing chips in centrifuges prior to briquetting to increase melt efficiency.
“It doesn’t have to leave the facility,” he said, “and they can control their alloys and contamination very well.”
Breaking Down
“Prior to being processed into dry chips or compact pucks,” Gould said, “vertical-axis crushers and shredders are available to make bulky wads of turnings more manageable. A shredder reduces light to moderate wads of metal turnings into flowable chips.”
A vertical-axis crusher, however, reduces turnings and bulky wads into shovel-grade chips. Prab reports that a shredder reduces turnings volume up to four times at the source, and a crusher reduces scrap volume up to a 6-1 ratio.
“A shredder is an option for the company’s E-Series fully automated chip system, which is one of Prab’s more popular offerings,” Gould said. “We recommend it if you have nominal chip throughput.”
He said the system can process a variety of workpiece materials at a rate of 113 kg (250 lbs.) per hour for aluminum chips, 272 kg (600 lbs.) per hour for brass, 340 kg (750 lbs.) per hour for steel and 363 kg (800 lbs.) per hour for cast iron.
“The E-Series system is compact enough to be moved with a forklift,” Gould said. “They’re used for smaller plug-and-play applications.”
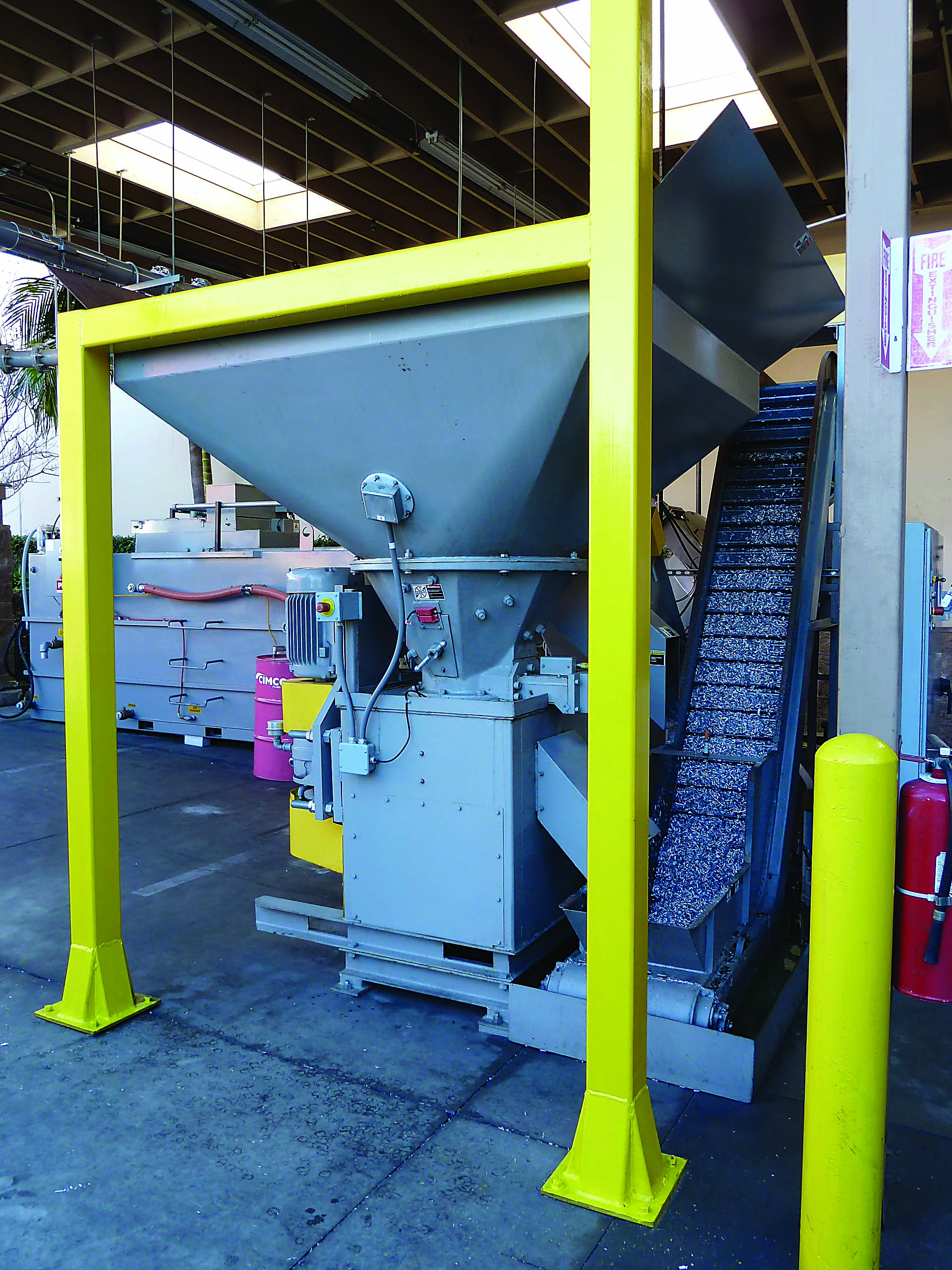
Hook said Prab also offers the Bundle Breaker, a pre-processing piece of equipment with dual rotating cylinders to shred apart stringy wads of chips, turning and bundles. That capability is particularly beneficial when long, stringy ribbons of material become tied together while a solid piece of metal is held inside.
“The biggest challenge in the automatic scrap handling business is in parts, bar ends and contamination making it into the scrap flow,” he said.
Hook said if a relatively large chunk of solid metal is introduced into a centrifuge spinning at, say, 1,700 rpm, damage to the wringer is likely.
“You basically turn it into a projectile at that point in time,” he said.
Parting Ways
Prior to shredding or crushing, Hook said chip wads frequently go through a solid separator, and Prab provides four different types that use air, vibration or a combination of both.
“Even though crushers or shredders can oftentimes handle or even process some of the solids,” he said, “as you can expect, anytime a sold piece meets a high-torque piece of equipment, no matter how fast the clutch disengages or overload kicks on, there’s always the potential for damage.”
In addition to separating solids from chips and turnings, Hook emphasized it’s important to have some sort of separation technology to avoid one type of workpiece material being processed with another type and causing cross contamination. The simplest, most widely used is magnetic separation, which separates ferrous from nonferrous materials. When there is a significant difference in the density of metals being processed, density separation is possible. In addition, eddy current separators are available for nonferrous materials.
“However,” he said, “by the time you get to that level, you might be better off having dedicated systems to do your higher-percentage materials.”
One way to reduce the amount of coolant on chips is to apply substantially less by machining with a minimum-quantity lubrication
system. Viner said Knoll America offers AerosolMaster 4000 ATS and 4000 Cryolub MQL systems for almost all machining processes with geometrically defined cutting edges, such as on machining centers, process lines and turning, milling, drilling and sawing machines.
“I don’t think it has been adopted enough yet,” he said, “but it will eventually. The chips are a lot cleaner when they come out.”
In the meantime, manufacturers of chip handling systems continue to refine and enhance their
equipment.
“We have incorporated many more features into our equipment to make them less user-intensive and less maintenance-intensive so systems can generally be set up to run without manual intervention,” Hook said. “The only time intervention is required is when something goes amiss.”
For more information from Prab about chip handling systems and from Sandvik Coromant about chip management, view video presentations at cteplus.delivr.com/2n8aq and cteplus.delivr.com/272pe
Chip Control Through Oscillation
Prior to processing chips in a chip handling system, it’s beneficial to control how chips are formed so they flow through the system without being caught in conveyors or needing to be crushed or shredded into a manageable size. This capability is especially helpful when thread turning, which tends to generate long, stringy and tangled turnings. The chips not only take extra work to process but tend to coil around robots, chucks, tools and components.
In addition, chip control when thread turning has become increasingly challenging as more part manufacturers machine more near-net-shape forgings, such as ones made of low-carbon steel for automotive applications, and only remove a small amount of material, said John Winter, product manager of East U.S. for Sandvik Coromant Co.
“You need a certain chip thickness as you’re processing the part in order to gain chip control,” he said.
To overcome these issues, the Mebane, North Carolina-based toolmaker developed the OptiThreading software module for its cloud-based CoroPlus Tool Path software. Winter explained that the module creates CNC threading code based on the cutting data parameters to mechanically control the chip and provide the correct number of passes with evenly distributed cutting forces.
He said the code enables toolpaths that deliver controlled, oscillating movements that go in and out of a cut on all passes except the last one, which is a straight, conventional toolpath.
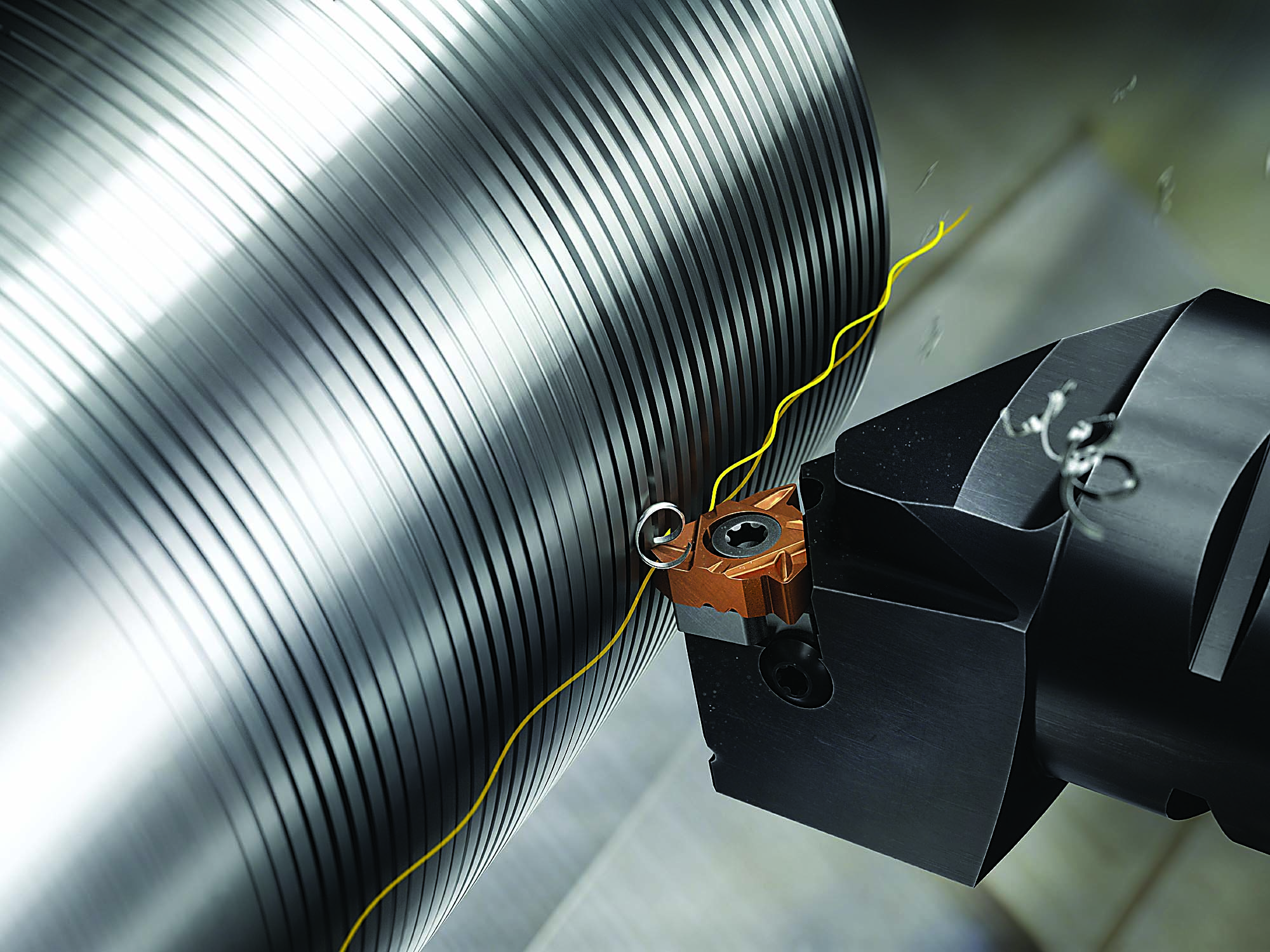
“Even in the final pass when you are creating that full chip form,” Winter said, “you still are managing the chip.”
The resulting chips are 50.8 mm (2") to 101.6 mm (4") long.
“That chip is manageable enough that it should get through the chip hopper,” Winter said.
Because OptiThreading creates high cutting forces on a tool as it moves in and out of a cut, he recommends using only CoroThread 266 indexable-insert thread turning tools. The tool body features the iLock interface, a locking mechanism that provides insert security by preventing it from moving in the pocket.
“The CoroThread 266 has a rail within the shim that goes right into the back of the insert and supports it and keeps it from moving,” Winter said. “You get a better-quality thread.”
He said the cutting movement during the OptiThreading process extends tool life because wear is spread over a larger area of an insert instead of one spot when conventional thread turning. Also, having pocket security enables an insert to handle a heavier load and reduce the number of passes, depending on the thread size, finish specification and the number of passes required.
The process is suitable for external and internal threading. Winter said internal threading can be the more problematic of the two because chips tend to ball up more when they’re inside a part. To overcome that issue, he recommends a pull threading operation when using OptiThreading to flow chips out of the part instead of staying inside.
He said tool grades are available for threading a variety of workpiece materials, including steel, stainless steel, iron, brass and heat-resistant superalloys. Sandvik Coromant even successfully tested the process on drawn over mandrel steel tubing. DOM is a metalforming process that starts with an electrically welded formed tube, which is cold-drawn through a die and over the sides of a mandrel.
“I don’t know anyone who can get chip control when threading that material,” Winter said.
— Alan Richter
Contact Details
Contact Details
Contact Details
Related Glossary Terms
- alloys
alloys
Substances having metallic properties and being composed of two or more chemical elements of which at least one is a metal.
- centers
centers
Cone-shaped pins that support a workpiece by one or two ends during machining. The centers fit into holes drilled in the workpiece ends. Centers that turn with the workpiece are called “live” centers; those that do not are called “dead” centers.
- centrifuge
centrifuge
Filtering device that uses a spinning bowl and the differences in specific gravities of materials to separate one from another. A centrifuge can be used to separate loosely emulsified and free oils from water-diluted metalworking fluid mixes and to remove metalworking fluids from chips.
- computer numerical control ( CNC)
computer numerical control ( CNC)
Microprocessor-based controller dedicated to a machine tool that permits the creation or modification of parts. Programmed numerical control activates the machine’s servos and spindle drives and controls the various machining operations. See DNC, direct numerical control; NC, numerical control.
- coolant
coolant
Fluid that reduces temperature buildup at the tool/workpiece interface during machining. Normally takes the form of a liquid such as soluble or chemical mixtures (semisynthetic, synthetic) but can be pressurized air or other gas. Because of water’s ability to absorb great quantities of heat, it is widely used as a coolant and vehicle for various cutting compounds, with the water-to-compound ratio varying with the machining task. See cutting fluid; semisynthetic cutting fluid; soluble-oil cutting fluid; synthetic cutting fluid.
- gang cutting ( milling)
gang cutting ( milling)
Machining with several cutters mounted on a single arbor, generally for simultaneous cutting.
- grinding
grinding
Machining operation in which material is removed from the workpiece by a powered abrasive wheel, stone, belt, paste, sheet, compound, slurry, etc. Takes various forms: surface grinding (creates flat and/or squared surfaces); cylindrical grinding (for external cylindrical and tapered shapes, fillets, undercuts, etc.); centerless grinding; chamfering; thread and form grinding; tool and cutter grinding; offhand grinding; lapping and polishing (grinding with extremely fine grits to create ultrasmooth surfaces); honing; and disc grinding.
- mandrel
mandrel
Workholder for turning that fits inside hollow workpieces. Types available include expanding, pin and threaded.
- metalcutting ( material cutting)
metalcutting ( material cutting)
Any machining process used to part metal or other material or give a workpiece a new configuration. Conventionally applies to machining operations in which a cutting tool mechanically removes material in the form of chips; applies to any process in which metal or material is removed to create new shapes. See metalforming.
- metalforming
metalforming
Manufacturing processes in which products are given new shapes either by casting or by some form of mechanical deformation, such as forging, stamping, bending and spinning. Some processes, such as stamping, may use dies or tools with cutting edges to cut as well as form parts.
- metalworking
metalworking
Any manufacturing process in which metal is processed or machined such that the workpiece is given a new shape. Broadly defined, the term includes processes such as design and layout, heat-treating, material handling and inspection.
- milling
milling
Machining operation in which metal or other material is removed by applying power to a rotating cutter. In vertical milling, the cutting tool is mounted vertically on the spindle. In horizontal milling, the cutting tool is mounted horizontally, either directly on the spindle or on an arbor. Horizontal milling is further broken down into conventional milling, where the cutter rotates opposite the direction of feed, or “up” into the workpiece; and climb milling, where the cutter rotates in the direction of feed, or “down” into the workpiece. Milling operations include plane or surface milling, endmilling, facemilling, angle milling, form milling and profiling.
- minimum-quantity lubrication
minimum-quantity lubrication
Use of cutting fluids of only a minute amount—typically at a flow rate of 50 to 500 ml/hr.—which is about three to four orders of magnitude lower than the amount commonly used in flood cooling. The concept addresses the issues of environmental intrusiveness and occupational hazards associated with the airborne cutting fluid particles on factory shop floors. The minimization of cutting fluid also saves lubricant costs and the cleaning cycle time for workpieces, tooling and machines. Sometimes referred to as “near-dry lubrication” or “microlubrication.”
- parting
parting
When used in lathe or screw-machine operations, this process separates a completed part from chuck-held or collet-fed stock by means of a very narrow, flat-end cutting, or parting, tool.
- sawing
sawing
Machining operation in which a powered machine, usually equipped with a blade having milled or ground teeth, is used to part material (cutoff) or give it a new shape (contour bandsawing, band machining). Four basic types of sawing operations are: hacksawing (power or manual operation in which the blade moves back and forth through the work, cutting on one of the strokes); cold or circular sawing (a rotating, circular, toothed blade parts the material much as a workshop table saw or radial-arm saw cuts wood); bandsawing (a flexible, toothed blade rides on wheels under tension and is guided through the work); and abrasive sawing (abrasive points attached to a fiber or metal backing part stock, could be considered a grinding operation).
- superalloys
superalloys
Tough, difficult-to-machine alloys; includes Hastelloy, Inconel and Monel. Many are nickel-base metals.
- threading
threading
Process of both external (e.g., thread milling) and internal (e.g., tapping, thread milling) cutting, turning and rolling of threads into particular material. Standardized specifications are available to determine the desired results of the threading process. Numerous thread-series designations are written for specific applications. Threading often is performed on a lathe. Specifications such as thread height are critical in determining the strength of the threads. The material used is taken into consideration in determining the expected results of any particular application for that threaded piece. In external threading, a calculated depth is required as well as a particular angle to the cut. To perform internal threading, the exact diameter to bore the hole is critical before threading. The threads are distinguished from one another by the amount of tolerance and/or allowance that is specified. See turning.
- toolpath( cutter path)
toolpath( cutter path)
2-D or 3-D path generated by program code or a CAM system and followed by tool when machining a part.
- turning
turning
Workpiece is held in a chuck, mounted on a face plate or secured between centers and rotated while a cutting tool, normally a single-point tool, is fed into it along its periphery or across its end or face. Takes the form of straight turning (cutting along the periphery of the workpiece); taper turning (creating a taper); step turning (turning different-size diameters on the same work); chamfering (beveling an edge or shoulder); facing (cutting on an end); turning threads (usually external but can be internal); roughing (high-volume metal removal); and finishing (final light cuts). Performed on lathes, turning centers, chucking machines, automatic screw machines and similar machines.
Contributors
Knoll America Inc.
248-498-1400
www.knollamerica.com
Prab Inc.
877-558-9834
www.prab.com
Sandvik Coromant Co.
800-726-3845
www.sandvik.coromant.com/us