END USER: Independent Protection Co. Inc., (574) 533-4116, www.ipclp.com.
CHALLENGE: Bring outsourced parts in-house that were being milled and machine them on a CNC lathe.
SOLUTION: A 6-axis turning center equipped with a bar feeder.
SOLUTION PROVIDERS: Eurotech, (352) 799-5223, www.eurotechelite.com; Superior Equipment Solutions, (937) 704-0357, www.supequipment.com.
Because lightning strikes Earth more than 4.3 million times per day, protection from this form of Mother Nature’s wrath is in great demand. That’s where Independent Protection Co. Inc. enters the picture. The Goshen, Ind., company manufactures high-performance lightning rods and other lightning protection devices and offers system design and layout services, installation assistance and onsite supervision.
IPC also makes parts for transit buses and specialty vehicles for its sister company, Turtle Top, New Paris, Ind. One type of part for those applications is a steel seat track T-nut.
IPC outsourced production, but wanted to bring it in-house to reduce lead times and costs, noted Plant Manager Tony Bradley. He added that the machine shops producing those parts for IPC were running them on milling machines, which requires paying labor to cut the raw workpiece material, load it in a jig, machine the parts while monitoring the machine throughout the day and then unload the finished part from the jig.
Having a shop produce the parts on a bar-fed lathe would alleviate a great deal of operator intervention, but finding a job shop to do that proved problematic. “The companies we talked to did not want to run the steel T-nuts on their CNC lathes as they would not guarantee their machines could run them,” Bradley said.
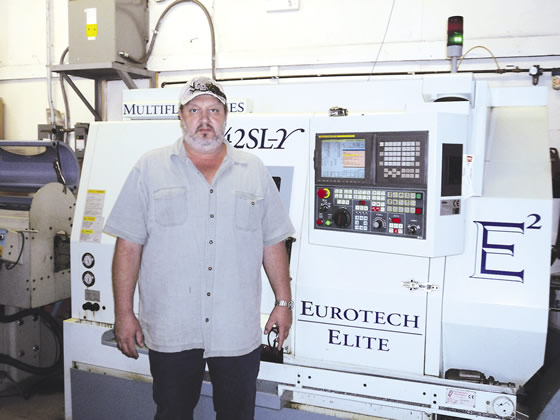
Plant Manager Tony Bradley says the Eurotech E42SL-Y turning center enabled IPC bring production of outsourced T-nut parts (inset) in-house and reduced the scrap from about 25 percent to 3 percent.
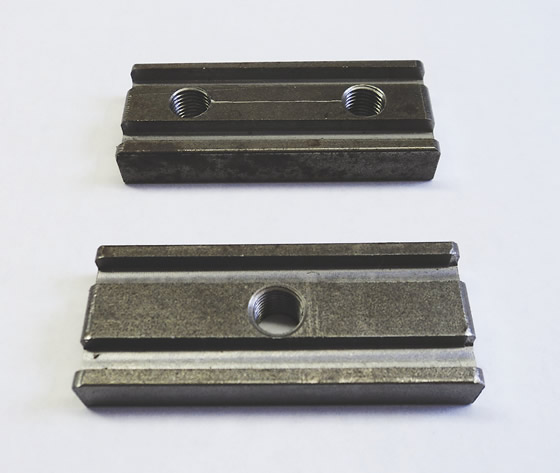
He started researching offerings from lathe builders and quickly ran into a dead end with the first builder. “Once we got into the T-nuts, he said, ‘My machine won’t do that. I won’t guarantee it will hold up and do it accurately,’ ” Bradley recalled. “Then I ran across a Web page that said, ‘Take the Eurotech challenge,’ so I answered the questions on it and the next day I got a call from Brendon Gideon at Superior Equipment, Eurotech’s distributor for Indiana.”
After showing him the T-nut parts and some lightning protection parts that IPC wanted to turn, Bradley noted Superior Equipment Solutions, Franklin, Ohio, guaranteed the Eurotech E42SL-Y 6-axis turning center would be an effective solution. Eurotech is located in Brooksville, Fla.
After purchasing the machine, which is fed 44 "-long bar stock, IPC received training from Eurotech. “We didn’t know anything about programming the machine and in 3 days they had us trained,” Bradley said.
IPC produces more than 14,000 T-nuts annually on the Eurotech machine, as well as a similar volume of lightning protection parts made of bronze, aluminum and copper. Prior to acquiring the Eurotech lathe, IPC machined those lightning protection parts on manual lathes and drill presses.
In addition, IPC machined workpieces produced via sand molding in its foundry. That casting process, however, can create inclusions in the workpieces, Bradley pointed out. “Sometimes you get hollow areas in the center of them that we call ‘blow holes,’ ” he said. “Scrap rates can go through the roof. With the Eurotech, we’re doing them out of billet rod. It’s more accurate and produces a better part all around.”
After switching to billet rod, the scrap rate dropped from around 25 percent to less than 3 percent, while throughput time dropped 80 percent, from 5 days to 1 day, on most parts, Bradley said. IPC also reduced the number of mold lines in the foundry from three to one. The remaining line primarily produces flat bases that can’t be turned.
In addition, Bradley said purchasing the E42SL-Y enabled IPC, which runs one shift, to go from 15 machine operators to nine, running lights out the rest of the day and on weekends. “I don’t live too far from work, so I can load the machine up, then pop in and throw some more bars on when it’s empty.”
Related Glossary Terms
- computer numerical control ( CNC)
computer numerical control ( CNC)
Microprocessor-based controller dedicated to a machine tool that permits the creation or modification of parts. Programmed numerical control activates the machine’s servos and spindle drives and controls the various machining operations. See DNC, direct numerical control; NC, numerical control.
- flat ( screw flat)
flat ( screw flat)
Flat surface machined into the shank of a cutting tool for enhanced holding of the tool.
- gang cutting ( milling)
gang cutting ( milling)
Machining with several cutters mounted on a single arbor, generally for simultaneous cutting.
- jig
jig
Tooling usually considered to be a stationary apparatus. A jig assists in the assembly or manufacture of a part or device. It holds the workpiece while guiding the cutting tool with a bushing. A jig used in subassembly or final assembly might provide assembly aids such as alignments and adjustments. See fixture.
- lathe
lathe
Turning machine capable of sawing, milling, grinding, gear-cutting, drilling, reaming, boring, threading, facing, chamfering, grooving, knurling, spinning, parting, necking, taper-cutting, and cam- and eccentric-cutting, as well as step- and straight-turning. Comes in a variety of forms, ranging from manual to semiautomatic to fully automatic, with major types being engine lathes, turning and contouring lathes, turret lathes and numerical-control lathes. The engine lathe consists of a headstock and spindle, tailstock, bed, carriage (complete with apron) and cross slides. Features include gear- (speed) and feed-selector levers, toolpost, compound rest, lead screw and reversing lead screw, threading dial and rapid-traverse lever. Special lathe types include through-the-spindle, camshaft and crankshaft, brake drum and rotor, spinning and gun-barrel machines. Toolroom and bench lathes are used for precision work; the former for tool-and-die work and similar tasks, the latter for small workpieces (instruments, watches), normally without a power feed. Models are typically designated according to their “swing,” or the largest-diameter workpiece that can be rotated; bed length, or the distance between centers; and horsepower generated. See turning machine.
- milling
milling
Machining operation in which metal or other material is removed by applying power to a rotating cutter. In vertical milling, the cutting tool is mounted vertically on the spindle. In horizontal milling, the cutting tool is mounted horizontally, either directly on the spindle or on an arbor. Horizontal milling is further broken down into conventional milling, where the cutter rotates opposite the direction of feed, or “up” into the workpiece; and climb milling, where the cutter rotates in the direction of feed, or “down” into the workpiece. Milling operations include plane or surface milling, endmilling, facemilling, angle milling, form milling and profiling.
- turning
turning
Workpiece is held in a chuck, mounted on a face plate or secured between centers and rotated while a cutting tool, normally a single-point tool, is fed into it along its periphery or across its end or face. Takes the form of straight turning (cutting along the periphery of the workpiece); taper turning (creating a taper); step turning (turning different-size diameters on the same work); chamfering (beveling an edge or shoulder); facing (cutting on an end); turning threads (usually external but can be internal); roughing (high-volume metal removal); and finishing (final light cuts). Performed on lathes, turning centers, chucking machines, automatic screw machines and similar machines.
- web
web
On a rotating tool, the portion of the tool body that joins the lands. Web is thicker at the shank end, relative to the point end, providing maximum torsional strength.