END USER: Dura-Mill Inc., (800) 444-6455, www.duramill.com.
CHALLENGE: Eliminate component degradation on tool grinding machines.
SOLUTION: Switching to a low-viscosity, cobalt-inhibited, hydrocracked synthetic grinding oil.
SOLUTION PROVIDER: Blaser Swisslube Inc., (845) 294-3200, www.blaser.com.
Grinding oil is essential when grinding high-performance carbide cutting tools. It’s needed to keep grinding burn at bay and provide lubricity at the wheel/workpiece interface to impart the required surface finishes. However, an oil with an improper formulation can have unintended consequences.
Dura-Mill Inc., Malta, N.Y., produces solid-carbide endmills, such as its WhisperKut and WhisperKut Plus with an asymmetrical variable-helix design to reduce harmful harmonic resonance. The toolmaker was experiencing machine tool issues but having trouble pinpointing the exact cause, noted Charles Ward, Dura-Mill’s plant engineer.
“The electrical cabling was failing at an astounding rate in several different brands of machines,” Ward said, adding that the plastic wire ways that prevent wires from becoming tangled were also cracking and falling apart.
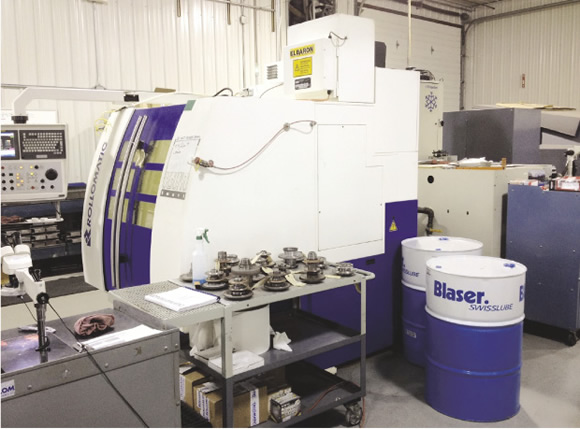
After switching to Blaser Swisslube’s Blasogrind HC5 synthetic grinding oil, Dura-Mill eliminated degradation to plastic components in its grinding machines (above) for producing solid-carbide endmills (below).
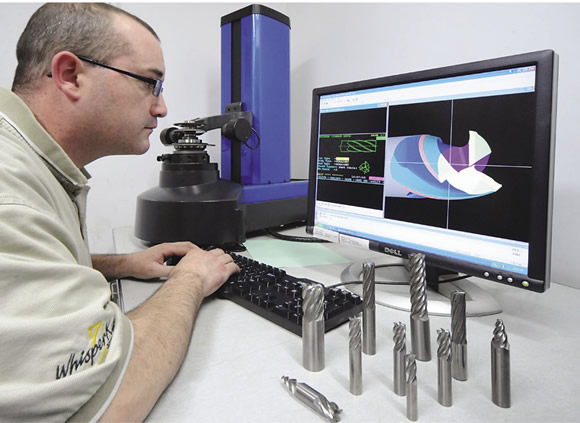
He explained that once the outer jacket of a wire hardened and broke, the same thing would happen to the inner jacket. “In a lot of cases, when the inner jacket breaks, it’ll take the copper wire with it and the machine will fail,” Ward said. “On average, every couple of years we had to replace several thousand dollars worth of cables and be down a couple of days doing it.”
In addition, oil mist caused external plastic components to deteriorate.
On-site for an unrelated reason, an engineer from a grinding machine builder noticed the deterioration inside a machine, felt the nonsynthetic, hydro-treated grinding oil and asked about the type of oil being applied, Ward noted.
After the engineer informed the toolmaker that he had seen similar problems with that type of oil, Dura-Mill knew it needed to make a change. “We asked for a recommendation,” Ward said, “and that’s when we were directed to the people at Blaser Swisslube.”
Metalworking fluids manufacturer Blaser Swisslube Inc., Goshen, N.Y., sent Joe Giza, area manager, and Uli Kuster, grinding applications manager, to investigate the problems Dura-Mill was experiencing and present a solution. After investigating and analyzing the issues, they determined Blaser’s Blasogrind HC5 was needed and commenced testing. The low-viscosity, cobalt-inhibited, hydrocracked synthetic grinding oil is approved for use in all major oil filtration systems and is recommended by various tool grinding machine builders, according to the company.
During testing, Dura-Mill’s engineers, in conjunction with Blaser’s grinding applications team, set out to determine if any additional productivity benefits could be realized by increasing wheel speeds and feed rates on the grinders.
The toolmaker initially reduced cycle time from a previous best of 10.5 minutes to 9.25 minutes and achieved fluting rates for a ¾ " tool of 7 to 9 ipm with a 0.170 " DOC, according to Ward. “This is a substantial productivity gain, especially when you take into account that our surface finish has not decreased and no stress cracks are being introduced into the tool surface,” he said. “It is also incredible that the power draw on the machines’ spindles has not increased. We can only attribute this to the higher lubricity properties of the oil.”
Dura-Mill then sought to tweak the process to a higher level of productivity without negatively impacting tool quality. “We were amazed that we were able to achieve a 20 to 30 percent increase in our metal-removal rates pretty much across the board, with a 20 percent decrease in cycle time, on average, just by switching out the oil,” said Chris Clairmont, chief CNC programmer for Dura-Mill. He added that the Blaser oil feels slicker and cleaner than the previous product.
According to Brett Reynolds, senior applications engineer – west for Blaser Swisslube, the Blasogrind HC grinding oil series has a unique EP additive package that, when combined with the base oil, solved and stopped the attack of the sealing materials and plastic components. “It is my belief that the competitor’s oil had an additive in it that was causing the attack of the plastic and sealing materials,” he said. “As to which additive, I don’t know.”
In addition to eliminating the machine damage, which included the cables, the new oil squashed a biofilm issue that the previous oil was causing in one machine. Although biological growth is uncommon in pure oil, it’s not unheard of, Ward pointed out. “It looked like something from a frog pond floating around in there,” he said, “and it had a distinct, nasty odor. It’s been quite some time now and the problem has not returned.”
Related Glossary Terms
- computer numerical control ( CNC)
computer numerical control ( CNC)
Microprocessor-based controller dedicated to a machine tool that permits the creation or modification of parts. Programmed numerical control activates the machine’s servos and spindle drives and controls the various machining operations. See DNC, direct numerical control; NC, numerical control.
- extreme pressure additives ( EP)
extreme pressure additives ( EP)
Cutting-fluid additives (chlorine, sulfur or phosphorus compounds) that chemically react with the workpiece material to minimize chipwelding. Good for high-speed machining. See cutting fluid.
- feed
feed
Rate of change of position of the tool as a whole, relative to the workpiece while cutting.
- fluting
fluting
Cutting straight or spiral grooves in drills, endmills, reamers and taps to improve cutting action and remove chips.
- grinding
grinding
Machining operation in which material is removed from the workpiece by a powered abrasive wheel, stone, belt, paste, sheet, compound, slurry, etc. Takes various forms: surface grinding (creates flat and/or squared surfaces); cylindrical grinding (for external cylindrical and tapered shapes, fillets, undercuts, etc.); centerless grinding; chamfering; thread and form grinding; tool and cutter grinding; offhand grinding; lapping and polishing (grinding with extremely fine grits to create ultrasmooth surfaces); honing; and disc grinding.
- grinding machine
grinding machine
Powers a grinding wheel or other abrasive tool for the purpose of removing metal and finishing workpieces to close tolerances. Provides smooth, square, parallel and accurate workpiece surfaces. When ultrasmooth surfaces and finishes on the order of microns are required, lapping and honing machines (precision grinders that run abrasives with extremely fine, uniform grits) are used. In its “finishing” role, the grinder is perhaps the most widely used machine tool. Various styles are available: bench and pedestal grinders for sharpening lathe bits and drills; surface grinders for producing square, parallel, smooth and accurate parts; cylindrical and centerless grinders; center-hole grinders; form grinders; facemill and endmill grinders; gear-cutting grinders; jig grinders; abrasive belt (backstand, swing-frame, belt-roll) grinders; tool and cutter grinders for sharpening and resharpening cutting tools; carbide grinders; hand-held die grinders; and abrasive cutoff saws.
- inches per minute ( ipm)
inches per minute ( ipm)
Value that refers to how far the workpiece or cutter advances linearly in 1 minute, defined as: ipm = ipt 5 number of effective teeth 5 rpm. Also known as the table feed or machine feed.
- lubricity
lubricity
Measure of the relative efficiency with which a cutting fluid or lubricant reduces friction between surfaces.
- metalworking
metalworking
Any manufacturing process in which metal is processed or machined such that the workpiece is given a new shape. Broadly defined, the term includes processes such as design and layout, heat-treating, material handling and inspection.