At its best, reaming can be a grand finale, leaving high-precision holes with excellent surface finish. But the final act of the holemaking process might be spoiled by bad actors playing roles that result in scrapped parts and broken tools.
To prevent horror shows like this, as well as lesser disappointments, during reaming, machine shops and their toolmakers can take a variety of steps to help ensure that the process doesn’t deliver an unpleasant surprise ending.
According to experts, one of the main culprits for reaming gone wrong is runout. And it doesn’t take much runout to throw a reaming process off-track, said Patrick Cline, national product manager for holemaking at Iscar USA, a cutting tool supplier in Arlington, Texas.
“After 0.0003",” he said, “especially in high-speed reaming, you’re going to see problems start to show up.”
Cline explained that runout-related troubles, such as chatter and rough surface finish, are caused by unbalanced cutting forces that make tools oscillate.
And reaming, he said, “is a very high-force process because there’s a lot of friction (caused by) a lot of contact between the reamer and the part. That’s why it’s important to have the same amount of cutting pressure all the way around.”
A key to preventing problems resulting from runout is the choice of toolholders. Instead of standard collets, shops engaged in reaming should opt for holders that minimize runout, said Robert Tennant, engineering manager for round tools at Star Cutter Co. in Farmington Hills, Michigan.
Cline said almost all cutting tool companies sell toolholders that can be adjusted to reduce runout. As an example, he pointed to Iscar’s Finefit product, which is adjustable both radially and axially.
Another adjustable offering from Iscar is its Bayo T-Ream high-speed reaming system. He explained that Bayo T-Ream features three adjustment screws that can be tightened in turn to move the reamer enough to eliminate runout.
“It’s a simple solution and very cost-effective as opposed to buying a specific adjustable holder like Finefit,” Cline said.
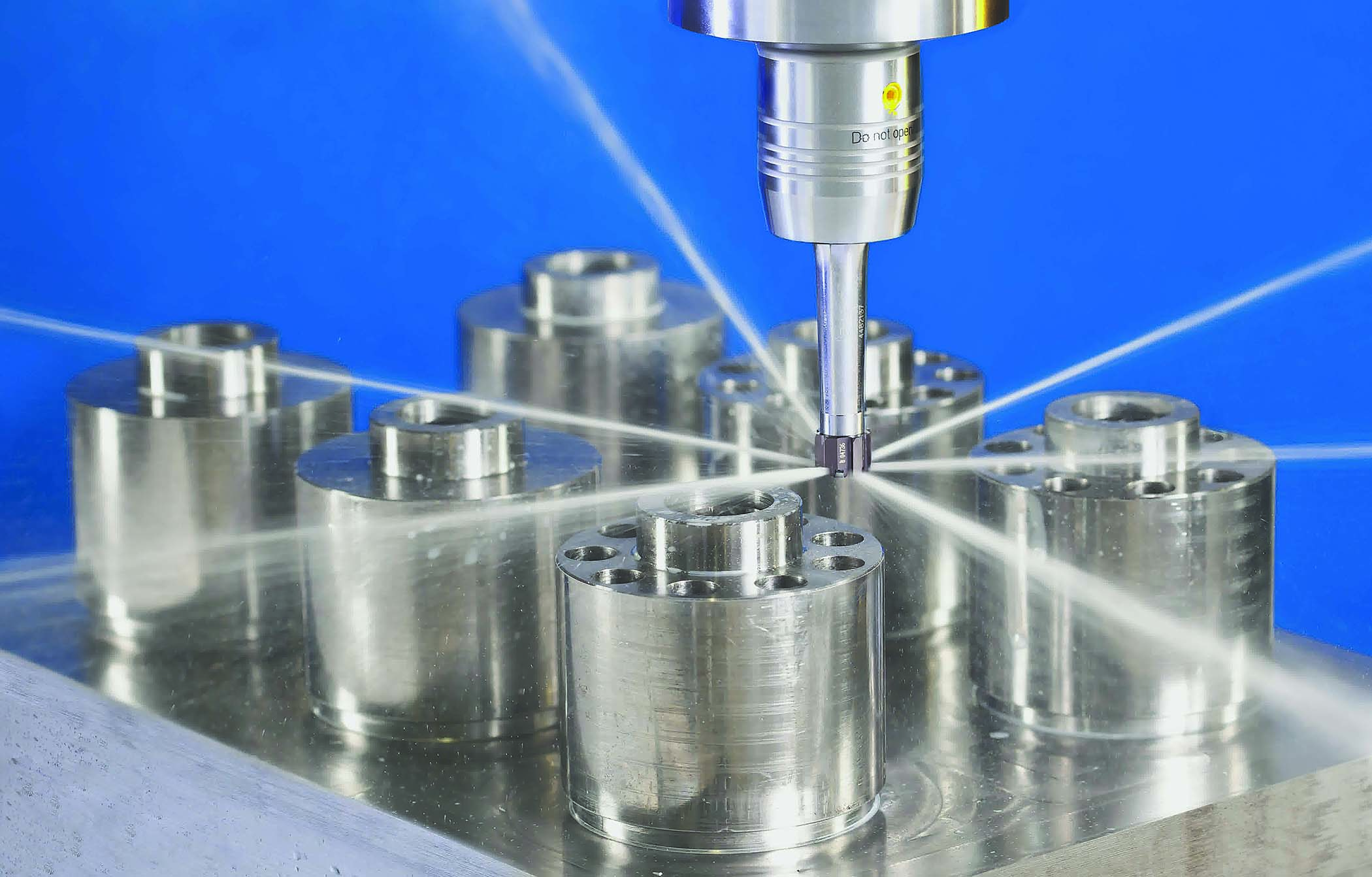
In addition to runout, chatter during reaming can be caused by the feed rate, said Steve Pilger, North American product manager for holemaking at YG-1 Tool (USA) Co., a cutting tool supplier in Vernon Hills, Illinois.
“Typically,” he said, “I found that increasing the feed rate slowly and finding a sweet spot will eliminate that chatter. We call it feeding past the chatter.”
Taking Stock
Chatter is just one of the problems that can be caused by the stock left for the reamer to remove. The right amount of stock for a particular application depends on the tool and the material being machined.
Chatter and poor surface finish might be the result if too little stock is left for reaming, said Cline, who ties the problems to how a tool removes material in these cases.
“You want to cut that material as opposed to rubbing it off,” he said. “Every cutting edge has a certain amount of edge prep that you need to get past. And if you don’t leave enough material, then you’re never really cutting. You’re just rubbing, which (produces) a lot of pressure and heat.”
On the other hand, excessive amounts of stock also can cause reaming troubles.
“If there’s more stock than what’s recommended, we have to make sure the tool is sharpened on the end to clear that amount,” said Jamie Dunneback, Star’s sales manager for round tools. “Let’s say somebody’s leaving 2 mm a side to ream and my tool’s not sharpened to machine 2 mm. That tool’s going to hit where it’s not sharpened, and you’re going to chip it or break it.”
He pointed out that the suggested stock removal amounts for different materials don’t vary much. A general rule, he said, is to leave about half a millimeter per side for a reaming operation.
Cline said recommended stock amounts range from 0.002" to 0.008" per side, depending on the material hardness and the size of the reamer. He added that reducing unneeded stock by relatively small amounts can give a big boost to tool life.
Longer Life
Dunneback said tool life during reaming also can be extended by running at the feeds and speeds recommended for the material being machined and the number of cutting teeth on the tool.
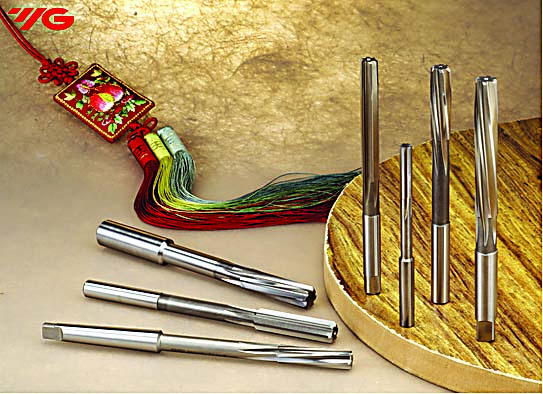
In addition, reamer life depends in part on the job done by the roughing tool before reaming.
“If you’re trying to ream a hole that wasn’t roughed out (properly), you could be trying to remove too much material on one side and not enough on the other side,” Dunneback said. “That will create side pressure on the reamer as it’s coming in, which can break it by deflection.”
The choice of coolant also can have a major impact on the life of a reamer.
“Since reaming is such a high-pressure, high-friction application,” Cline said, “shops are going to need a good brand of coolant and a high coolant concentration if they’re going to do a lot of reaming.”
He said if a shop is reaming a small number of holes, coolant concentrations in the 5% to 7% range might be acceptable.
“But if they’re going to ream a bunch of holes day in and day out, it would really benefit them to enrich their coolant so that the concentration was more like 12% to 13%,” Cline said. “That will increase the life of the reamer head because you have more lubricity and more oil within the emulsion mixture to help remove some of the heat and provide a reduction in friction.”
As for brands, he recommends coolants with high-heat, high-pressure additives, which he said yield better tool life than more economical brands that lack these additives.
Cline also pointed out that “coolant-through” options like Bayo T-Ream extend tool life by delivering coolant right to the cutting edges. In addition, he said, these options allow reaming at much higher feed rates and are better when it comes to evacuating chips. The latter, he said, translates into better surface finishes because chips aren’t staying around to rub against part surfaces.
Finer Finish
Another way of improving surface finish is to add more cutting teeth to a reamer.
“If I take a four-flute reamer and make it an eight-flute reamer, I’ve got more cutting blades removing the same amount of material,” Dunneback said. “So I’m going to burnish a lot more, and I’m going to get a better finish.”
He added that more cutting teeth also improve the roundness of reamed holes.
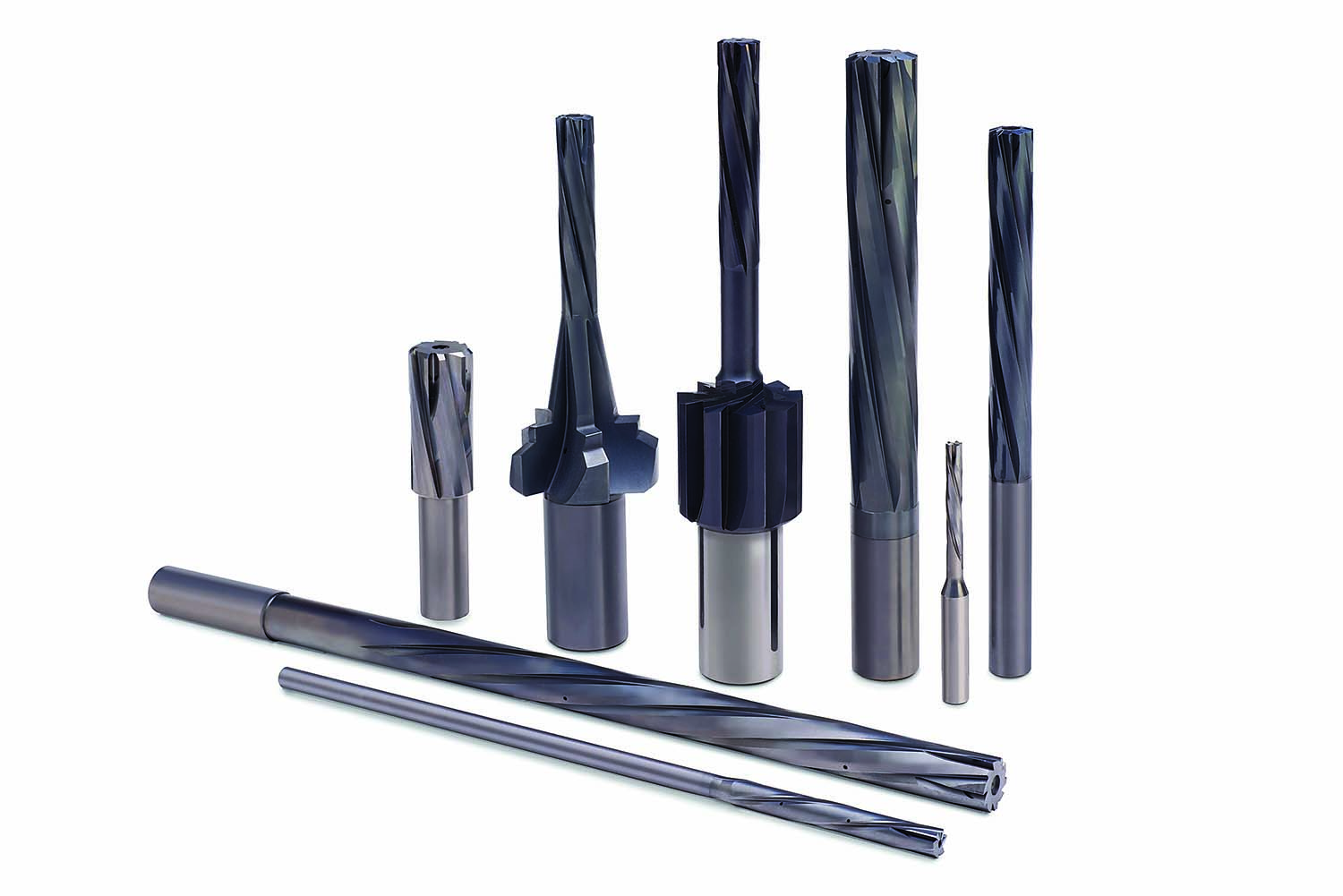
Of course, there’s a limit to how many cutting teeth can be added to a reamer of a certain diameter.
“If it’s a 1" diameter, we can get all kinds of cutting blades in there,” Dunneback said. “But if it’s 0.25", you’re probably only going to get four blades in there.”
One way of getting better surface finish from a reamer of any diameter is to opt for helical flutes. He said they provide more cutting surface area than straight flutes, which produces more burnishing action. As an added benefit, helical flutes help with chip evacuation, he noted.
Getting It Straight
Star offers a patented product for reaming applications called Super Round Tool, which includes both helical and straight flutes. Dunneback pointed out that SRT’s straight flutes help guarantee that a straight hole is being cut.
But there’s more to cutting a straight hole than anything the reamer does.
“The old saying was, ‘With a reamer, if you start with a banana, you get a banana,’” Pilger said. “So if you don’t use a high-quality drill and the proper speeds and feeds, the drill will wander and the reamer will just follow whatever hole you’ve put in.”
In some applications where hole straightness requirements are on the print, he said reaming will be preceded by single-point boring. While a reamer has multiple teeth, a single-point boring bar has only one cutting edge, he noted.
“A single-point boring bar will straighten out a hole,” Pilger said, “and then you can go to your high-speed reaming.”
On the downside, he added, the penetration rate of single-point boring bars probably won’t exceed 3 ipm. By contrast, he said, diamond reamers with multiple teeth can achieve penetration rates as high as 60 ipm.
In addition to straightness, shops must take steps to ensure the positional accuracy of holes. Dunneback said one simple thing that helps in this regard is using the same machine for roughing and reaming. That way, he said, there’s no chance of positional discrepancies caused by moving parts from one machine to another for different operations in the holemaking process.
Taken together, all this expert input should reassure shops that — with the right tools and tactics — they can avert reaming tragedies and instead produce happy holemaking endings for themselves and customers.
Contact Details
Contact Details
Contact Details
Related Glossary Terms
- boring
boring
Enlarging a hole that already has been drilled or cored. Generally, it is an operation of truing the previously drilled hole with a single-point, lathe-type tool. Boring is essentially internal turning, in that usually a single-point cutting tool forms the internal shape. Some tools are available with two cutting edges to balance cutting forces.
- boring bar
boring bar
Essentially a cantilever beam that holds one or more cutting tools in position during a boring operation. Can be held stationary and moved axially while the workpiece revolves around it, or revolved and moved axially while the workpiece is held stationary, or a combination of these actions. Installed on milling, drilling and boring machines, as well as lathes and machining centers.
- burnishing
burnishing
Finishing method by means of compressing or cold-working the workpiece surface with carbide rollers called burnishing rolls or burnishers.
- chatter
chatter
Condition of vibration involving the machine, workpiece and cutting tool. Once this condition arises, it is often self-sustaining until the problem is corrected. Chatter can be identified when lines or grooves appear at regular intervals in the workpiece. These lines or grooves are caused by the teeth of the cutter as they vibrate in and out of the workpiece and their spacing depends on the frequency of vibration.
- coolant
coolant
Fluid that reduces temperature buildup at the tool/workpiece interface during machining. Normally takes the form of a liquid such as soluble or chemical mixtures (semisynthetic, synthetic) but can be pressurized air or other gas. Because of water’s ability to absorb great quantities of heat, it is widely used as a coolant and vehicle for various cutting compounds, with the water-to-compound ratio varying with the machining task. See cutting fluid; semisynthetic cutting fluid; soluble-oil cutting fluid; synthetic cutting fluid.
- emulsion
emulsion
Suspension of one liquid in another, such as oil in water.
- feed
feed
Rate of change of position of the tool as a whole, relative to the workpiece while cutting.
- flutes
flutes
Grooves and spaces in the body of a tool that permit chip removal from, and cutting-fluid application to, the point of cut.
- hardness
hardness
Hardness is a measure of the resistance of a material to surface indentation or abrasion. There is no absolute scale for hardness. In order to express hardness quantitatively, each type of test has its own scale, which defines hardness. Indentation hardness obtained through static methods is measured by Brinell, Rockwell, Vickers and Knoop tests. Hardness without indentation is measured by a dynamic method, known as the Scleroscope test.
- inches per minute ( ipm)
inches per minute ( ipm)
Value that refers to how far the workpiece or cutter advances linearly in 1 minute, defined as: ipm = ipt 5 number of effective teeth 5 rpm. Also known as the table feed or machine feed.
- lubricity
lubricity
Measure of the relative efficiency with which a cutting fluid or lubricant reduces friction between surfaces.
- reamer
reamer
Rotating cutting tool used to enlarge a drilled hole to size. Normally removes only a small amount of stock. The workpiece supports the multiple-edge cutting tool. Also for contouring an existing hole.
Contributors
Iscar USA
888-472-2788
www.iscarmetals.com
Star Cutter Co.
248-474-8200
www.starcutter.com
YG-1 Tool (USA) Co.
800-765-8665
www.yg1usa.com