Contact Details
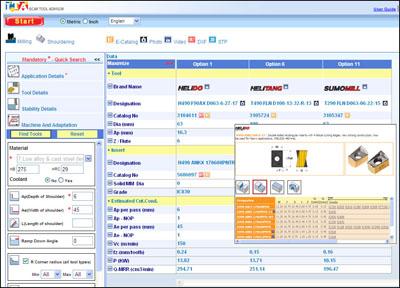
Profitability from machining a part is dependent on the machine type, cutting tool, cutting conditions and the interaction between them. ITA (ISCAR Tool Advisor) is a user-friendly, web-based tool selection software that is constructed upon a unique mathematical algorithm. The importance of tool selection is paramount in maximizing productivity and thus should be based scientifically on objective and empirical technical data rather than any conventional intuitive method. The ITA application provides an effective process of narrowing down all possible tooling scenarios, taking into account cutting conditions, machine power, metal removal rate and cutting time. Even for a simple application, such as milling a 90 degree shoulder of low alloy steel, 10mm height and 10mm width, tools selected by ITA delivered more productivity compared to manual tool selection done by industry experts, according to the company. ITA delivers profitability. Users can enter only a few mandatory fields (2 to 6) for quick results or complete more detailed fields specifying machine parameters, tool diameters, tool type, grade etc. The application provides the 3 best tooling options but can display up to 25 tool recommendations per application search. Results include tool details, insert details, cutting conditions, power, metal removal rate and cutting time. Each search has a printable recommendation report valuable to the user. ITA supports both inch and metric platforms and supports 25 different languages. Users can link to the ISCAR electronic catalogue, 2D and 3D tool drawings, product videos and pictures. ITA can send users via e-mail a pdf file that includes the input and output for each application search. The ITA software is available free of charge, 24 hours a day, 7 days a week with a direct connection to an ITA support team.. Immediate access can be obtained at www.iscarmetals.com or by going directly to www.iscarmetals.com/ITA. The application can also be uploaded and used on any iPhone or iPod Touch, making all of ISCAR's technical information available and accessible to any user via the internet, Wi-Fi or mobile connection. As the ITA application gains users, ISCAR is developing new sub-applications to meet the diversity of their needs. Iscar is currently launching three new sub-applications in the Groove-Turn main application: Internal grooving, Internal turning and Internal face grooving (applies to boring bars.
Related Glossary Terms
- boring
boring
Enlarging a hole that already has been drilled or cored. Generally, it is an operation of truing the previously drilled hole with a single-point, lathe-type tool. Boring is essentially internal turning, in that usually a single-point cutting tool forms the internal shape. Some tools are available with two cutting edges to balance cutting forces.
- gang cutting ( milling)
gang cutting ( milling)
Machining with several cutters mounted on a single arbor, generally for simultaneous cutting.
- grooving
grooving
Machining grooves and shallow channels. Example: grooving ball-bearing raceways. Typically performed by tools that are capable of light cuts at high feed rates. Imparts high-quality finish.
- milling
milling
Machining operation in which metal or other material is removed by applying power to a rotating cutter. In vertical milling, the cutting tool is mounted vertically on the spindle. In horizontal milling, the cutting tool is mounted horizontally, either directly on the spindle or on an arbor. Horizontal milling is further broken down into conventional milling, where the cutter rotates opposite the direction of feed, or “up” into the workpiece; and climb milling, where the cutter rotates in the direction of feed, or “down” into the workpiece. Milling operations include plane or surface milling, endmilling, facemilling, angle milling, form milling and profiling.
- turning
turning
Workpiece is held in a chuck, mounted on a face plate or secured between centers and rotated while a cutting tool, normally a single-point tool, is fed into it along its periphery or across its end or face. Takes the form of straight turning (cutting along the periphery of the workpiece); taper turning (creating a taper); step turning (turning different-size diameters on the same work); chamfering (beveling an edge or shoulder); facing (cutting on an end); turning threads (usually external but can be internal); roughing (high-volume metal removal); and finishing (final light cuts). Performed on lathes, turning centers, chucking machines, automatic screw machines and similar machines.