Contact Details
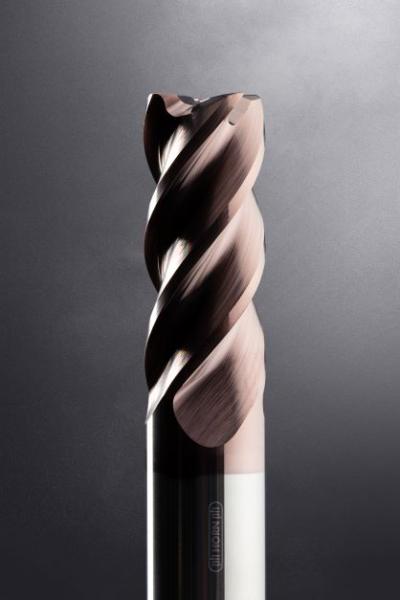
Horn has developed a new, solid carbide milling cutter range especially for machining stainless steels. The tools are for milling stainless materials in the food, chemical and pharmaceutical industries as well as the precision engineering and watchmaking industries.
In addition, due to their geometry and good chip breaking, the milling tools are suitable for machining numerous other materials. Due to the precise combination of the substrate, the macro and micro geometry as well as the IG3 coating, the milling system exhibits high performance and long tool life. The coating in particular offers high temperature resistance for machining steels alloyed with chromium, nickel and molybdenum.
Horn offers the solid carbide milling tools from stock in two types. The DSHPR variant is suitable as both a finishing and a roughing tool. The geometry is also adapted for trochoidal machining and plunging. The DSR type, with its very sharp cutting edge geometry and short design, is suitable for very small parts and unstable clamping conditions, such as in the medical and watchmaking industries. In the DSHPR line, all tools are available with four teeth and in diameters from 2 mm (0.079") to 20 mm (0.787"). Horn offers the DSR variant with three teeth in diameters from 1 mm (0.039") to 10 mm (0.394").
Related Glossary Terms
- gang cutting ( milling)
gang cutting ( milling)
Machining with several cutters mounted on a single arbor, generally for simultaneous cutting.
- milling
milling
Machining operation in which metal or other material is removed by applying power to a rotating cutter. In vertical milling, the cutting tool is mounted vertically on the spindle. In horizontal milling, the cutting tool is mounted horizontally, either directly on the spindle or on an arbor. Horizontal milling is further broken down into conventional milling, where the cutter rotates opposite the direction of feed, or “up” into the workpiece; and climb milling, where the cutter rotates in the direction of feed, or “down” into the workpiece. Milling operations include plane or surface milling, endmilling, facemilling, angle milling, form milling and profiling.
- milling cutter
milling cutter
Loosely, any milling tool. Horizontal cutters take the form of plain milling cutters, plain spiral-tooth cutters, helical cutters, side-milling cutters, staggered-tooth side-milling cutters, facemilling cutters, angular cutters, double-angle cutters, convex and concave form-milling cutters, straddle-sprocket cutters, spur-gear cutters, corner-rounding cutters and slitting saws. Vertical cutters use shank-mounted cutting tools, including endmills, T-slot cutters, Woodruff keyseat cutters and dovetail cutters; these may also be used on horizontal mills. See milling.
- stainless steels
stainless steels
Stainless steels possess high strength, heat resistance, excellent workability and erosion resistance. Four general classes have been developed to cover a range of mechanical and physical properties for particular applications. The four classes are: the austenitic types of the chromium-nickel-manganese 200 series and the chromium-nickel 300 series; the martensitic types of the chromium, hardenable 400 series; the chromium, nonhardenable 400-series ferritic types; and the precipitation-hardening type of chromium-nickel alloys with additional elements that are hardenable by solution treating and aging.