Contact Details
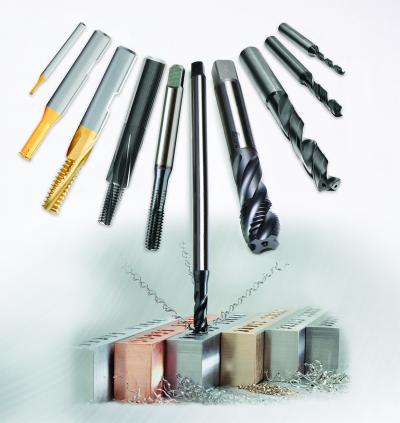
Today, EMUGE-FRANKEN USA, a leading manufacturer of high-performance taps, thread mills, drills, end mills and other rotary tools, has introduced its MultiTOOL program which includes versatile, affordable high-quality taps, thread mills and drills that are ideal for a wide range of materials in high-mix, low volume job shop applications.
“We are pleased to offer our customers a comprehensive theadmaking solution with our new MultiTOOL program,” said Marlon Blandon, Product Manager, Drills, Thread Milling. “As the innovator of the industry-leading MultiTAP, EMUGE-FRANKEN has expanded its successful multi-purpose tool concept to also include new thread mills and drills.”
The EMUGE MultiTOOL program includes the following products:
- MultiTAP™ tapping solution ranges from cut taps to form taps in different coatings, in addition to taps with extended lengths. Versatile MultiTAP features an innovative geometric design and a special base material and surface treatment, which allows it to cut a wide range of materials such as carbon steel, steel alloys, stainless steel, aluminum, cast iron, copper, brass and bronze. The taps are uniquely designed to produce threads within both 2B and 3B classes of fit, eliminating the guesswork required when calculating H-limits. MultiTAP significantly improves thread quality and boosts output, while reducing production costs.
- New MultiTHREAD™ MILL is an ideal general-purpose, cost-effective thread milling solution for job shops where part applications and materials frequently change. The new thread mills are designed to cut a wide range of standard materials very efficiently. MultiTHREAD features a proprietary TIN T21 coating developed by EMUGE, and is offered in a complete size and thread style range in either Full Form or Single Plane types. Only one tool is required for both through and blind holes, as well as for right or left-hand threads. The thread mills enable shops to boost their production and save on costs, due to reducing the number of tools needed.
- New MultiDRILL™ features affordable, high-quality solid carbide 3XD and 5XD drills for manufacturers that have limited quantity production runs or operate in a job shop environment with many materials. MultiDRILL is made of a unique sub-micro grain carbide grade that is harder than conventional carbide grades for drilling, yet it retains the ability to withstand shock and chipping. The new drills feature advanced TIALN-T63 coating utilizing nano-layer technology with surface hardness exceeding standard TIALN-based coatings, for reduced friction at high temperatures. The double margin designed drills are self-centering and feature concave cutting edges for higher chip shearing ability, providing longer tool life and productivity.
Related Glossary Terms
- alloys
alloys
Substances having metallic properties and being composed of two or more chemical elements of which at least one is a metal.
- gang cutting ( milling)
gang cutting ( milling)
Machining with several cutters mounted on a single arbor, generally for simultaneous cutting.
- hardness
hardness
Hardness is a measure of the resistance of a material to surface indentation or abrasion. There is no absolute scale for hardness. In order to express hardness quantitatively, each type of test has its own scale, which defines hardness. Indentation hardness obtained through static methods is measured by Brinell, Rockwell, Vickers and Knoop tests. Hardness without indentation is measured by a dynamic method, known as the Scleroscope test.
- milling
milling
Machining operation in which metal or other material is removed by applying power to a rotating cutter. In vertical milling, the cutting tool is mounted vertically on the spindle. In horizontal milling, the cutting tool is mounted horizontally, either directly on the spindle or on an arbor. Horizontal milling is further broken down into conventional milling, where the cutter rotates opposite the direction of feed, or “up” into the workpiece; and climb milling, where the cutter rotates in the direction of feed, or “down” into the workpiece. Milling operations include plane or surface milling, endmilling, facemilling, angle milling, form milling and profiling.
- milling machine ( mill)
milling machine ( mill)
Runs endmills and arbor-mounted milling cutters. Features include a head with a spindle that drives the cutters; a column, knee and table that provide motion in the three Cartesian axes; and a base that supports the components and houses the cutting-fluid pump and reservoir. The work is mounted on the table and fed into the rotating cutter or endmill to accomplish the milling steps; vertical milling machines also feed endmills into the work by means of a spindle-mounted quill. Models range from small manual machines to big bed-type and duplex mills. All take one of three basic forms: vertical, horizontal or convertible horizontal/vertical. Vertical machines may be knee-type (the table is mounted on a knee that can be elevated) or bed-type (the table is securely supported and only moves horizontally). In general, horizontal machines are bigger and more powerful, while vertical machines are lighter but more versatile and easier to set up and operate.
- tapping
tapping
Machining operation in which a tap, with teeth on its periphery, cuts internal threads in a predrilled hole having a smaller diameter than the tap diameter. Threads are formed by a combined rotary and axial-relative motion between tap and workpiece. See tap.
- titanium nitride ( TiN)
titanium nitride ( TiN)
Added to titanium-carbide tooling to permit machining of hard metals at high speeds. Also used as a tool coating. See coated tools.