Contact Details
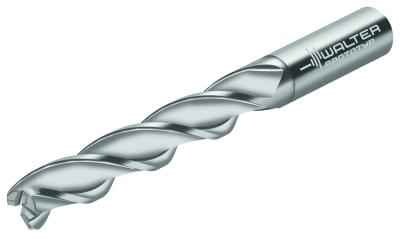
Walter unveiled its new MC166 Advance solid carbide milling cutter, which was developed for the aerospace industry and is suitable for all industrial sectors that machine aluminum, copper, brass, bronze and magnesium-based alloys (ISO N workpiece group).
The cutting tool was specifically designed for finishing and dynamic roughing of deep pockets and cavities. Dynamic milling involves machining at a low radial depth of cut (ae), a high axial depth of cut (ap) and with a large cutting-edge length (Lc), which is three times the cutting-edge diameter (Dc) for the MC166 Advance.
The MC166 Advance solid carbide milling cutter with increased core stability compared to a conventional tool core ensures a consistently reliable machining process even in unattended operations. A differential pitch provides optimum operational smoothness and significantly extends tool life.
The special micro-geometry makes the cutter an ideal choice for finishing high wall part features. The tool provides a high level of productivity and reduces cycle times because of its ability to mill at an optimal metal removal rate. The tool also features a 35° helix and a DIN 6535 HA (round cylindrical) shank. The uncoated WJ30UU-grade cutter is available in diameters from 12 to 20 mm.
The Walter lineup of products consists of three categories of tools. Advance tools (such as the MC166) indicate products efficiently balanced between price and performance, Supreme tools indicate the highest level of technology and performance available and Perform tools are products that provide an economical solution with focused importance on price.
Related Glossary Terms
- alloys
alloys
Substances having metallic properties and being composed of two or more chemical elements of which at least one is a metal.
- depth of cut
depth of cut
Distance between the bottom of the cut and the uncut surface of the workpiece, measured in a direction at right angles to the machined surface of the workpiece.
- gang cutting ( milling)
gang cutting ( milling)
Machining with several cutters mounted on a single arbor, generally for simultaneous cutting.
- milling
milling
Machining operation in which metal or other material is removed by applying power to a rotating cutter. In vertical milling, the cutting tool is mounted vertically on the spindle. In horizontal milling, the cutting tool is mounted horizontally, either directly on the spindle or on an arbor. Horizontal milling is further broken down into conventional milling, where the cutter rotates opposite the direction of feed, or “up” into the workpiece; and climb milling, where the cutter rotates in the direction of feed, or “down” into the workpiece. Milling operations include plane or surface milling, endmilling, facemilling, angle milling, form milling and profiling.
- milling cutter
milling cutter
Loosely, any milling tool. Horizontal cutters take the form of plain milling cutters, plain spiral-tooth cutters, helical cutters, side-milling cutters, staggered-tooth side-milling cutters, facemilling cutters, angular cutters, double-angle cutters, convex and concave form-milling cutters, straddle-sprocket cutters, spur-gear cutters, corner-rounding cutters and slitting saws. Vertical cutters use shank-mounted cutting tools, including endmills, T-slot cutters, Woodruff keyseat cutters and dovetail cutters; these may also be used on horizontal mills. See milling.
- milling machine ( mill)
milling machine ( mill)
Runs endmills and arbor-mounted milling cutters. Features include a head with a spindle that drives the cutters; a column, knee and table that provide motion in the three Cartesian axes; and a base that supports the components and houses the cutting-fluid pump and reservoir. The work is mounted on the table and fed into the rotating cutter or endmill to accomplish the milling steps; vertical milling machines also feed endmills into the work by means of a spindle-mounted quill. Models range from small manual machines to big bed-type and duplex mills. All take one of three basic forms: vertical, horizontal or convertible horizontal/vertical. Vertical machines may be knee-type (the table is mounted on a knee that can be elevated) or bed-type (the table is securely supported and only moves horizontally). In general, horizontal machines are bigger and more powerful, while vertical machines are lighter but more versatile and easier to set up and operate.
- pitch
pitch
1. On a saw blade, the number of teeth per inch. 2. In threading, the number of threads per inch.
- shank
shank
Main body of a tool; the portion of a drill or similar end-held tool that fits into a collet, chuck or similar mounting device.