Contact Details
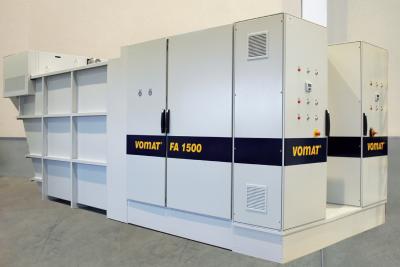
The larger the tool grinding batches and the more grinding machines are involved in the filtration process, the more necessary are high-performance large-scale and special filter systems for cleaning contaminated grinding oils. With the KFA 1500 Compact Filter System, the machine manufacturer Vomat from Treuen (Germany) provides tool manufacturers and regrinders with a high-performance, low-maintenance ultra-fine filtration system for grinding high-speed steels (HSS) and carbide materials, which promises optimum quality with high purity of NAS 7/8 or 3-5 µm even for very large batches.
Demanding grinding applications require a high-performance filter system that positively supports and influences the process flow. Ultra-fine filtration allows grinding oils to remain in the system significantly longer. Cleanly filtered, they help to increase the dimensional accuracy and surface quality of the products. Additionally, the right filter system also reduces energy consumption and disposal costs.
Vomat's product portfolio includes solutions for stand-alone systems, modular systems, central systems and individual customized specialty systems with central and decentralized functions. One example is the KFA 1500, a special ultra-fine filtration system that promises tool manufacturers and regrinders optimum economic quality even for large batches of different materials.
The KFA 1500 (260” x 100” x 103” h) has a tank volume of 10,000 liters and a filter capacity of 1,500 liters/minute. The medium is filtered by high-efficiency precoat filters in full flow at a filter fineness of 3-5 μm. Filtration takes place on demand and in an energy-efficient manner via a frequency-controlled system pump. The special drying unit is optimally designed for large batch sizes.
The cooling performance in the cold water circuit of the KFA 1500 is 200 kW in continuous operation. The temperature accuracy in the tolerance range of up to +/- 0.2 °C contributes to the optimum quality of the product.
Due to the precoat principle, there is no contamination of the swarf by filter aids. The residual moisture of the swarf is between five and ten percent, and the recyclable material is processed directly into a suitable transport container for recycling companies. The control technology can also be monitored and operated remotely.
As an option, VOMAT offers a compression cooler with external condenser and high control accuracy, as well as a material-dependent pre-separation system.
Related Glossary Terms
- grinding
grinding
Machining operation in which material is removed from the workpiece by a powered abrasive wheel, stone, belt, paste, sheet, compound, slurry, etc. Takes various forms: surface grinding (creates flat and/or squared surfaces); cylindrical grinding (for external cylindrical and tapered shapes, fillets, undercuts, etc.); centerless grinding; chamfering; thread and form grinding; tool and cutter grinding; offhand grinding; lapping and polishing (grinding with extremely fine grits to create ultrasmooth surfaces); honing; and disc grinding.
- high-speed steels ( HSS)
high-speed steels ( HSS)
Available in two major types: tungsten high-speed steels (designated by letter T having tungsten as the principal alloying element) and molybdenum high-speed steels (designated by letter M having molybdenum as the principal alloying element). The type T high-speed steels containing cobalt have higher wear resistance and greater red (hot) hardness, withstanding cutting temperature up to 1,100º F (590º C). The type T steels are used to fabricate metalcutting tools (milling cutters, drills, reamers and taps), woodworking tools, various types of punches and dies, ball and roller bearings. The type M steels are used for cutting tools and various types of dies.
- swarf
swarf
Metal fines and grinding wheel particles generated during grinding.
- tolerance
tolerance
Minimum and maximum amount a workpiece dimension is allowed to vary from a set standard and still be acceptable.