Contact Details
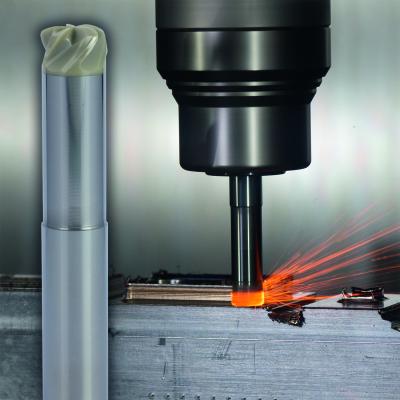
Today, EMUGE-FRANKEN USA, a leading manufacturer of high-performance taps, thread mills, end mills, drills, and other rotary tools, has announced the introduction of its Cera-Cut end mills featuring a high-hardness cutting ceramic head brazed to a carbide shank for optimal vibration dampening and longer tool life compared to one-piece ceramic tools. Featuring a high-feed duplex cutting edge geometry, Cera-Cut produces high metal removal rates in challenging nickel-based alloys, resulting in machining parts 200 to 400% faster than conventional carbide end mills. Also, the tool life of Cera-Cut is up to five times higher than regular carbide end mills.
“With the growing use of heat resistant super alloys, we are pleased to offer our customers new, long-lasting five-flute ceramic end mills for roughing and milling in these challenging applications,” said Mr. Dan Doiron, Manager, Milling Products, EMUGE-FRANKEN USA. “For example, Cera-Cut excels in the machining of complex aerospace parts.”
EMUGE-FRANKEN Cera-Cut End Mills are designed for the consistent cutting of high-temperature resistant materials such as Inconel, Hastelloy, and Nimonic as well as the machining of hardened tool steels. Cera-Cut is also suitable for making interrupted cuts, and offers a tight cutting diameter tolerance ranging from -0.0008" to -0.0016" (-20 to -40 microns), depending on the tool diameter.
Cera-Cut end mills can be used for roughing or pre-finishing, and can produce 2D or 3D contours, and are suitable for face milling, slot milling, helical milling, contour milling, and pocket milling. EMUGE-FRANKEN Cera-Cut End Mills are offered in different diameters from .24 to .79 inches (6 to 20 mm). Corner radius, modular and special designs are also available.
Related Glossary Terms
- alloys
alloys
Substances having metallic properties and being composed of two or more chemical elements of which at least one is a metal.
- gang cutting ( milling)
gang cutting ( milling)
Machining with several cutters mounted on a single arbor, generally for simultaneous cutting.
- milling
milling
Machining operation in which metal or other material is removed by applying power to a rotating cutter. In vertical milling, the cutting tool is mounted vertically on the spindle. In horizontal milling, the cutting tool is mounted horizontally, either directly on the spindle or on an arbor. Horizontal milling is further broken down into conventional milling, where the cutter rotates opposite the direction of feed, or “up” into the workpiece; and climb milling, where the cutter rotates in the direction of feed, or “down” into the workpiece. Milling operations include plane or surface milling, endmilling, facemilling, angle milling, form milling and profiling.
- shank
shank
Main body of a tool; the portion of a drill or similar end-held tool that fits into a collet, chuck or similar mounting device.
- tolerance
tolerance
Minimum and maximum amount a workpiece dimension is allowed to vary from a set standard and still be acceptable.
- tool steels
tool steels
Group of alloy steels which, after proper heat treatment, provide the combination of properties required for cutting tool and die applications. The American Iron and Steel Institute divides tool steels into six major categories: water hardening, shock resisting, cold work, hot work, special purpose and high speed.