Here is another fixturing trick. The problem is to make 100 1.5"-long-by-0.375"-wide square keys with radiused ends. I get this job every year or two, so I don’t want to spend a lot of time making a dedicated fixture. This is a simple part that deserves a simple fixture, but I want the parts to come out nicely in a reasonable amount of time, so this is what I do.
I have a job shop, and like most job shops, I have sets of gauge blocks and parallels in my tooling inventory. I also have a milling machine that usually has a 6" vise on it. So with the vise, some gauge blocks and a couple of parallels, I do a setup for this job that’s quick and effective, with no out-of-pocket costs.
Pieces of 0.375" square 12L14 are cut 1.625" long five at a time on a bandsaw. Then the mill cuts the 0.187" radius on one end two parts at a time.
Figure 1 shows all the pieces in the vise to set the position of the key blanks. Figure 2 on Page 9 shows the parts in the vise ready for machining. When the vise is clamped, the Z position will be maintained by the vise through the milling operation. If the parallels are left in, they can cause trouble, so get them out of there. I cut one end of 100 parts so they are 0.04" long, then I re-index zero and finish the parts.

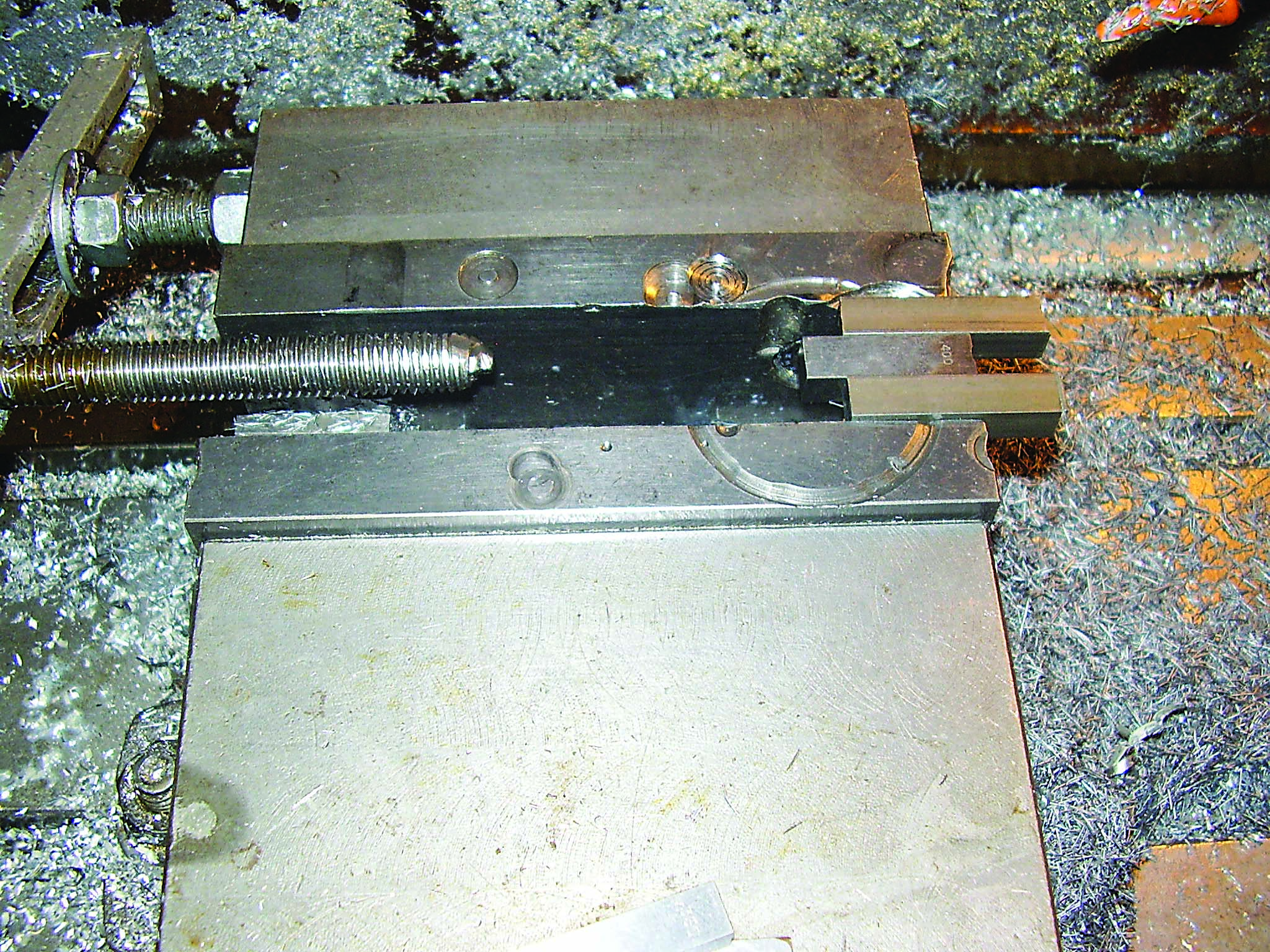
Figure 3 on Page 9 shows the different gauge blocks with the key blanks out of the vise, along with a couple of finished keys. The parts are cut with a 0.375" endmill, so a 0.4" block is put between two parts for clearance. These gauge blocks have a 0.35" thickness, so I made a groove on one end of the 0.4" block to ensure that it is put in correctly. I find that doing details like this saves aggravation with repetitive
operations.
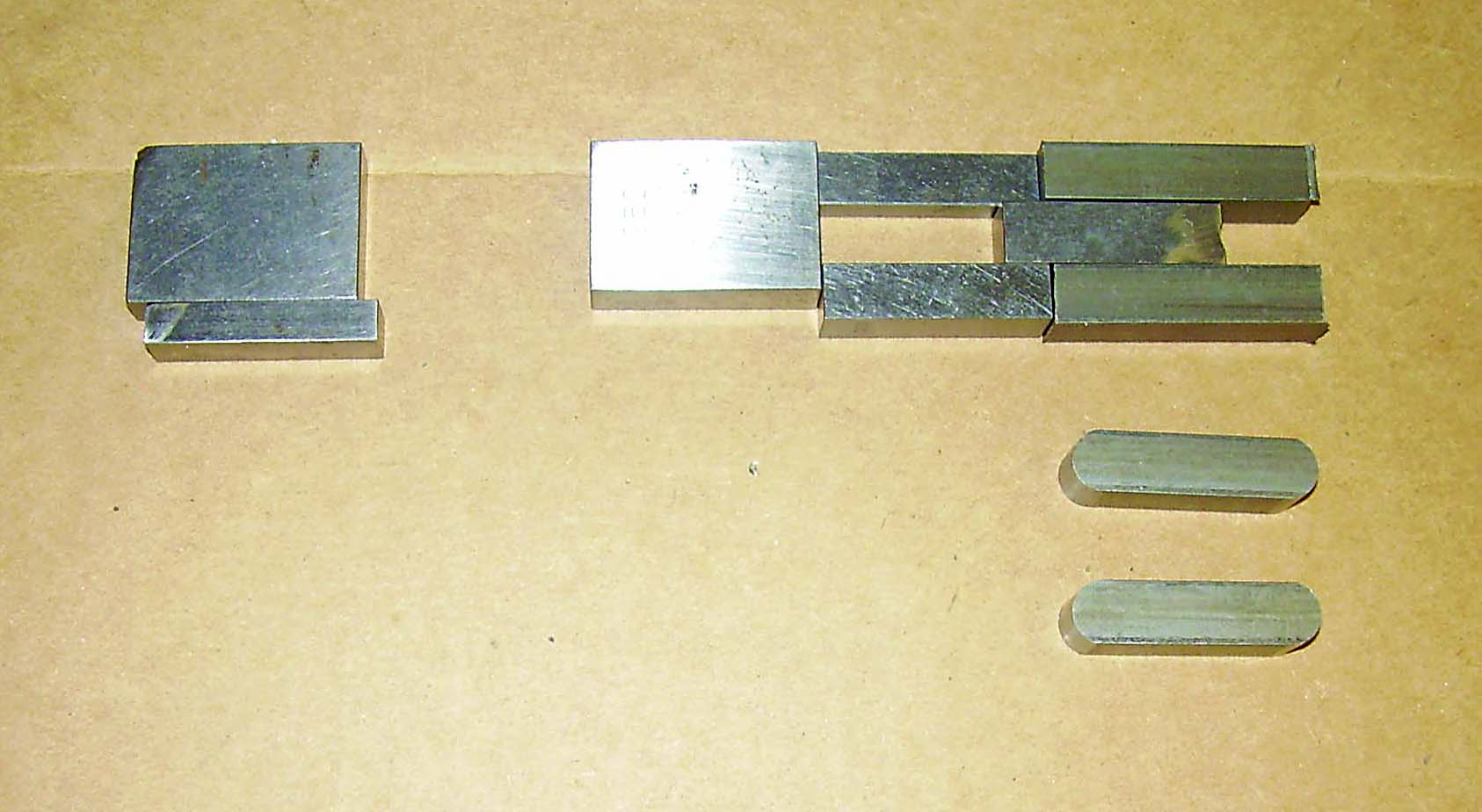
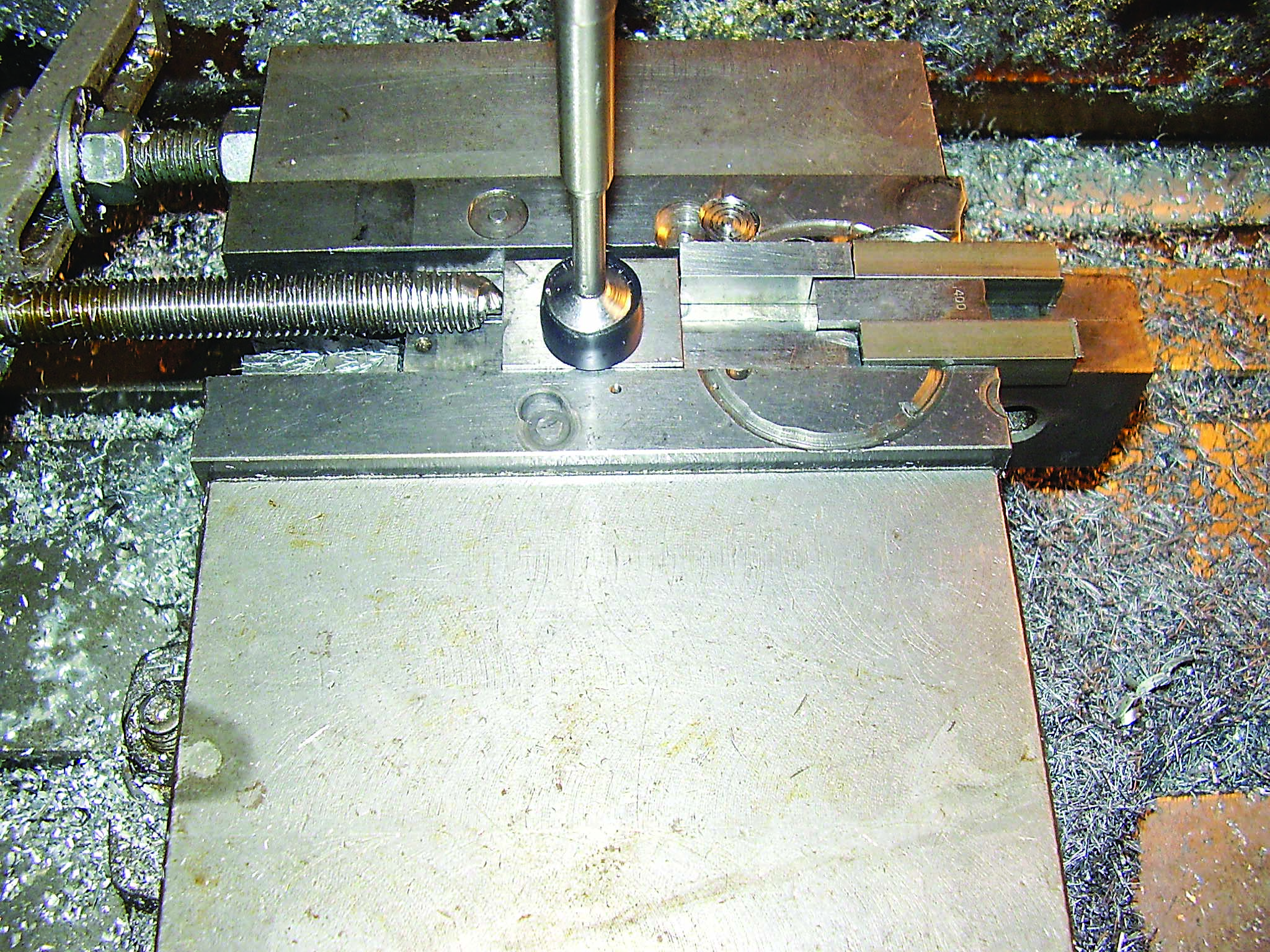
On the right side of the vise, there are 1.15" between the vice jaws. Note in Figure 4 on Page 10 that there are two blocks on the left. They add to the 1.15" and are placed between the left ends of the jaws against the bed. They ensure that the jaw faces stay parallel when clamped and securely clamp the parts. Don’t leave them out.
A vise stop is used to set the X dimension, and a pair of 0.5"-thick parallels are placed in the vise to set the Z dimension. The six pieces on the right in Figure 4 are placed on the parallels, and everything is squared up with slack removed. Then the vise is clamped.
The gauge blocks are made of 400 series stainless, so they can be heat-treated. That stuff is nicely magnetic, which means that you can use a magnet on a stick (see Figure 4) to pluck the three unclamped blocks out of the setup before the parallels are removed. If the unclamped blocks aren’t removed when the parallels come out, the blocks annoyingly will fall into the vise cavity. Then push the run button, and away you go.
Related Glossary Terms
- bandsaw
bandsaw
Machine that utilizes an endless band, normally with serrated teeth, for cutoff or contour sawing. See saw, sawing machine.
- clearance
clearance
Space provided behind a tool’s land or relief to prevent rubbing and subsequent premature deterioration of the tool. See land; relief.
- endmill
endmill
Milling cutter held by its shank that cuts on its periphery and, if so configured, on its free end. Takes a variety of shapes (single- and double-end, roughing, ballnose and cup-end) and sizes (stub, medium, long and extra-long). Also comes with differing numbers of flutes.
- fixture
fixture
Device, often made in-house, that holds a specific workpiece. See jig; modular fixturing.
- gang cutting ( milling)
gang cutting ( milling)
Machining with several cutters mounted on a single arbor, generally for simultaneous cutting.
- milling
milling
Machining operation in which metal or other material is removed by applying power to a rotating cutter. In vertical milling, the cutting tool is mounted vertically on the spindle. In horizontal milling, the cutting tool is mounted horizontally, either directly on the spindle or on an arbor. Horizontal milling is further broken down into conventional milling, where the cutter rotates opposite the direction of feed, or “up” into the workpiece; and climb milling, where the cutter rotates in the direction of feed, or “down” into the workpiece. Milling operations include plane or surface milling, endmilling, facemilling, angle milling, form milling and profiling.
- milling machine ( mill)
milling machine ( mill)
Runs endmills and arbor-mounted milling cutters. Features include a head with a spindle that drives the cutters; a column, knee and table that provide motion in the three Cartesian axes; and a base that supports the components and houses the cutting-fluid pump and reservoir. The work is mounted on the table and fed into the rotating cutter or endmill to accomplish the milling steps; vertical milling machines also feed endmills into the work by means of a spindle-mounted quill. Models range from small manual machines to big bed-type and duplex mills. All take one of three basic forms: vertical, horizontal or convertible horizontal/vertical. Vertical machines may be knee-type (the table is mounted on a knee that can be elevated) or bed-type (the table is securely supported and only moves horizontally). In general, horizontal machines are bigger and more powerful, while vertical machines are lighter but more versatile and easier to set up and operate.
- milling machine ( mill)2
milling machine ( mill)
Runs endmills and arbor-mounted milling cutters. Features include a head with a spindle that drives the cutters; a column, knee and table that provide motion in the three Cartesian axes; and a base that supports the components and houses the cutting-fluid pump and reservoir. The work is mounted on the table and fed into the rotating cutter or endmill to accomplish the milling steps; vertical milling machines also feed endmills into the work by means of a spindle-mounted quill. Models range from small manual machines to big bed-type and duplex mills. All take one of three basic forms: vertical, horizontal or convertible horizontal/vertical. Vertical machines may be knee-type (the table is mounted on a knee that can be elevated) or bed-type (the table is securely supported and only moves horizontally). In general, horizontal machines are bigger and more powerful, while vertical machines are lighter but more versatile and easier to set up and operate.
- parallel
parallel
Strip or block of precision-ground stock used to elevate a workpiece, while keeping it parallel to the worktable, to prevent cutter/table contact.