Industry News
07/01/2025
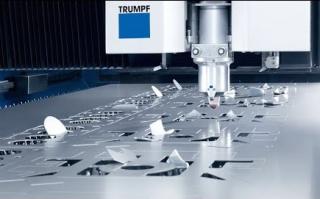
Southern States Machinery to represent Trumpf’s sheet metal fabricating products and services in Georgia. Maintecx becomes Trumpf’s new sales representative in Alabama, Tennessee and Mississippi.
06/26/2025
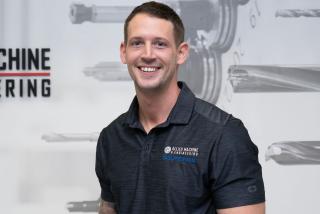
Allied Machine and Engineering, a leading manufacturer of holemaking and finishing cutting tools for the metal-cutting industry, has promoted Bill Ruegsegger III to Western regional manager.
06/26/2025
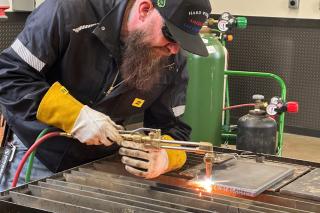
Victor, an ESAB brand, now offers qualifying industrial companies a free safety audit of their gas flow control systems and oxyfuel cutting and heating operations.
06/24/2025
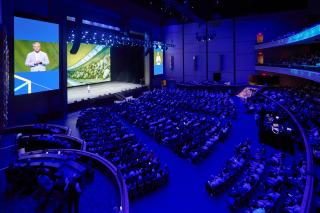
The Hexagon Live Global conference returned to Las Vegas June 16–19, this time at the Fontainebleau resort and casino. This year marks a quarter century of measurement technology development for Stockholm, Sweden-headquartered Hexagon AB, following its 2001 acquisition of metrology tool manufacturer Brown & Sharpe, said Ola Rollén, chairman of the board.
06/23/2025
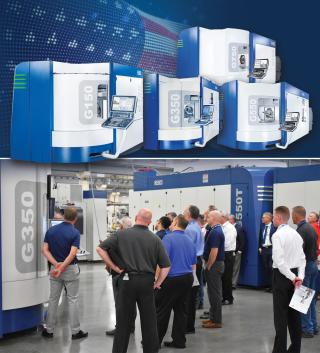
GROB Systems, Inc., a developer of manufacturing systems and machine tools, is hosting a 5-AXIS LIVE! technology event featuring “The Future of Manufacturing - Made in the USA,” together with twenty-one of its industry partners, at GROB’s North America headquarters and production facility in Bluffton, Ohio, on August 5, 2025, from 9:00 a.m. through 4:00 p.m.
06/20/2025
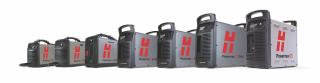
Hypertherm Associates, a U.S. based leading manufacturer of industrial cutting systems and software, has doubled the warranty period for the company’s Powermax plasma cutters from three years to six years. All customers who received delivery of a Powermax plasma or gouging system on or after January 1, 2025, are now retroactively eligible for the extended coverage.
06/18/2025
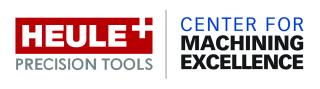
Heule Precision Tool, a leader in cross-hole finishing technology, has partnered with the Center for Machining Excellence (CME) in Whitestown, Indiana, and has become the CME's latest addition to the Cutting Tool Partners.
06/12/2025
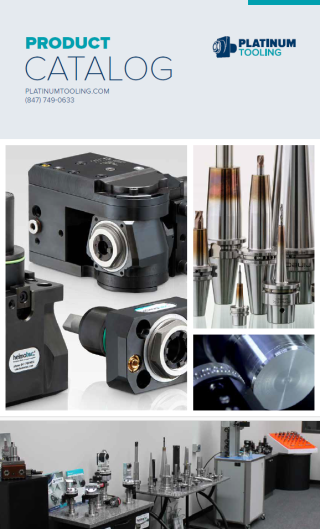
Platinum Tooling, the importer and master distributor of live tools, angle heads, Swiss machine products, knurling and marking tools manufactured by various international suppliers, just announced the release of their new product catalog.
06/11/2025
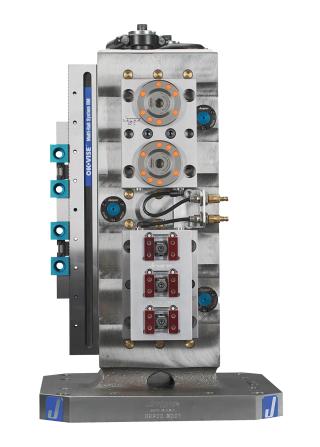
Jergens Custom Design and Build workholding solutions are engineered around part configurations using standard products and a six-step process to reduce cost and lead time for customers.
06/09/2025
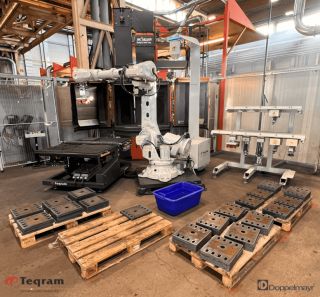
The Doppelmayr Group, a manufacturer of ropeway technology, which is used to transport people and goods by cable, is streamlining the grinding and blasting of plasma and flame cut parts with the introduction of Teqram's EasyGrinder autonomous robot.
06/06/2025
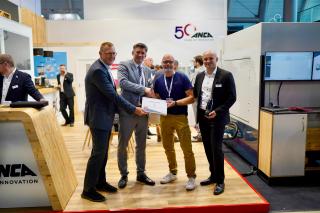
#ANCATooloftheYear2025 awards is a prestigious competition that invites toolmakers from around the world to showcase their outstanding designs, precision, and craftsmanship.
06/03/2025
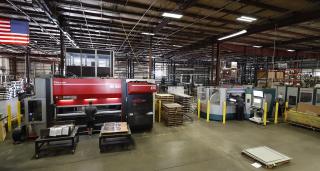
Estes Design and Manufacturing of Indianapolis has received its AS9100D certification for its quality management system governing the design, manufacture and assembly of fabricated sheet metal products.
06/03/2025
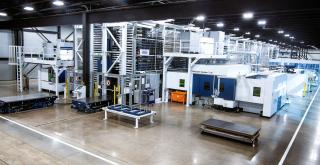
Ribbon-cutting ceremony in Farmington, Connecticut marks the official opening of the Smart Factory // TRUMPF announces new initiatives to increase local manufacturing, expand training facility, and grosw apprenticeship program.
06/02/2025
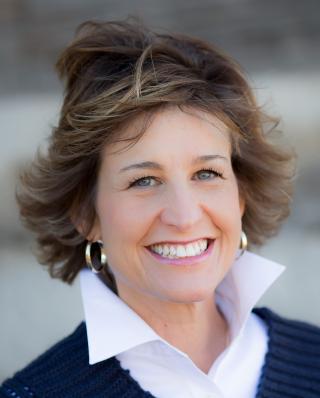
E-Z LOK, a manufacturer of threaded inserts for metal, plastic and wood, has hired a new sales representative firm in the Southwest area. Located in Scottsdale, Arizona, Desert Distribution covers Arizona, California, Colorado, New Mexico, Nevada and Utah.
06/01/2025
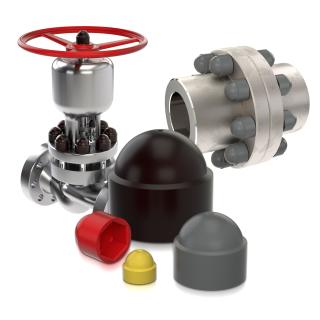
MOCAP has added a new protective solution to its product catalog: its BNCD Series of Domed Bolt and Nut Caps. Designed to provide both protection and a finished appearance, the company says these caps are "ideal for covering exposed bolt and nut heads in a variety of industrial, commercial, and consumer applications."
05/30/2025
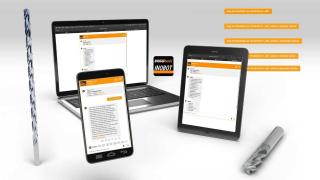
The tool manufacturer Inovatools from Kinding-Haunstetten, Germany, is setting new standards in the industry, and is the first provider to launch its own AI bot for topics related to machining: INOBOT.
05/29/2025
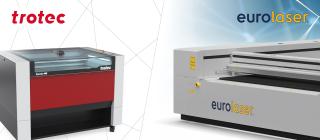
Two of the leading manufacturers in laser technology are combining their strengths: Trotec Laser and eurolaser are now entering a sales partnership. This cooperation aims to offer customers even more targeted advice and provide optimally tailored system solutions based on the long-standing market experience of both companies.
05/28/2025
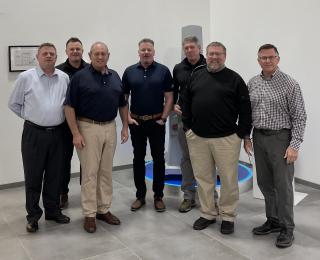
United Grinding North America Inc., a subsidiary of the United Grinding Group, has renewed a partnership with Dynamic Machine, a Detroit-area CNC equipment dealership.
05/28/2025
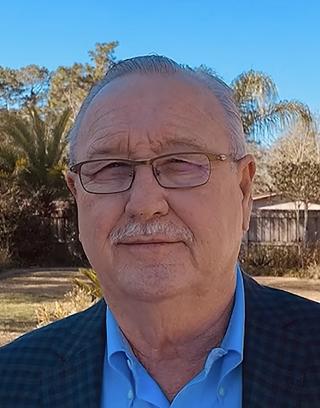
E-Z LOK, a manufacturer and master distributor of threaded inserts for metal, plastic and wood, has hired a new sales representative firm.
05/23/2025

Tsugami America, the exclusive North American importer of Precision Tsugami machine tools, has appointed Derek Briggs as its director of engineering.