One of the last critical processes when manufacturing parts, threading a hole necessitates careful tool selection and the right machining setup to prevent reworking and possibly scrapping a part. Manufacturers increasingly need to machine challenging, costly materials such as nickel-based alloys, heat-resistant super alloys and exotic materials that make the stakes even higher. These demanding materials have unique properties and application requirements that need to be factored in when selecting a tool.
Whether working with more common steels or newer, difficult-to-machine materials, manufacturers have a range of threading tool options that include application-specific and multi-purpose taps and thread mills. Traditionally used by shops as their threading go-to choice, taps can produce threaded holes with short cycle times and uniform quality while providing long tool life. Gaining popularity for good reason, thread milling maximizes process security and is flexible in terms of feed rates, thread size, programming approaches and, especially, the ability to control fit. The machinist can adjust thread size using different cutting strategies, which is advantageous on tight-tolerance threads.
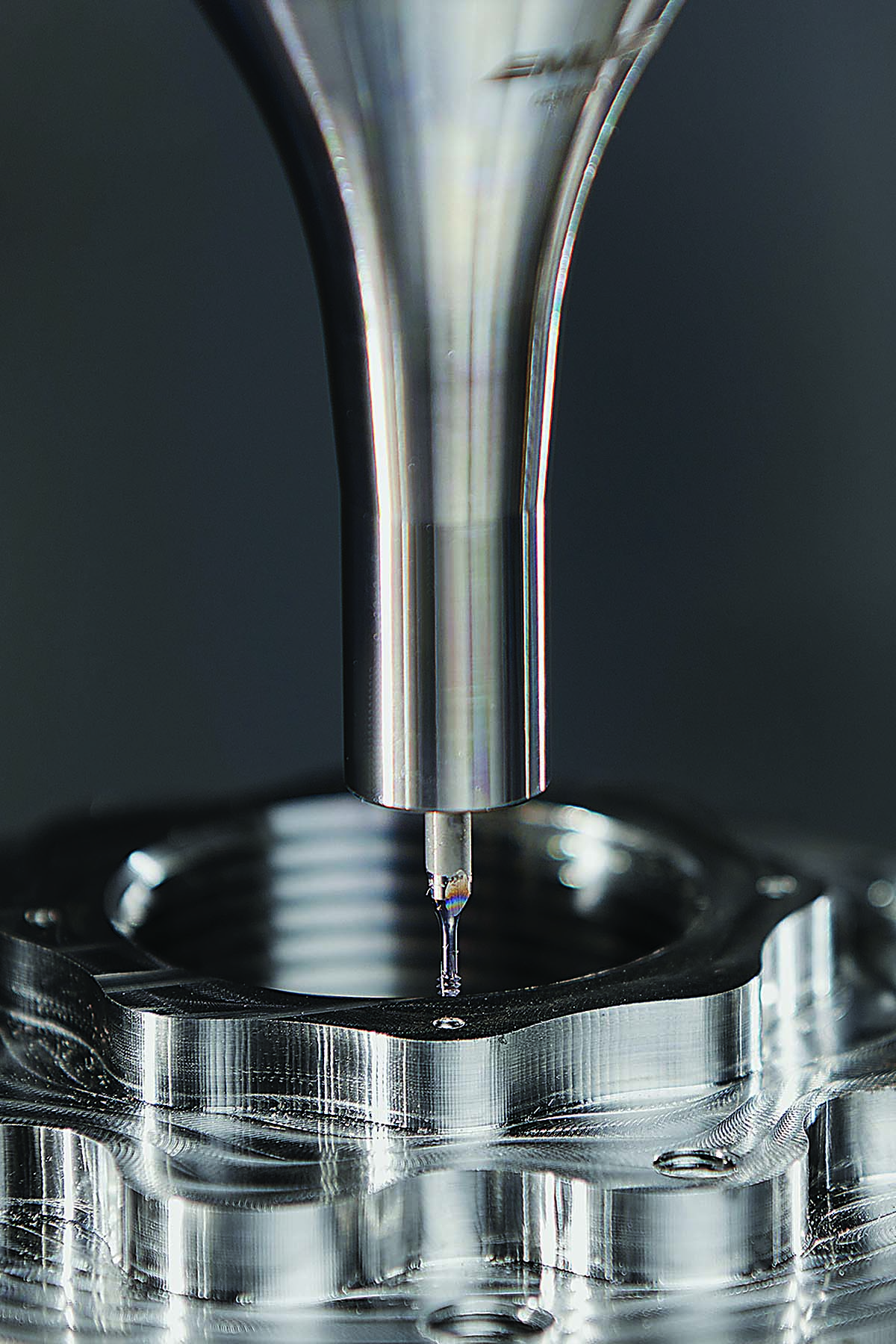
The benefit of working closely with the cutting tool supplier or manufacturer for application advice cannot be overstated. In addition to selecting the best tool for the threading requirements, cutting tool experts can help dial into the optimal machining speeds and feeds. Advice on emulsions, toolholding and workholding are all critical for maximizing tool life and part quality. It is also important to work with a cutting tool manufacturer or supplier that offers in-field product application specialists or services that allow an end user to send actual part or sample material for test cuts and programming support. Guidance such as this should include detailed reports on operating parameters and results.
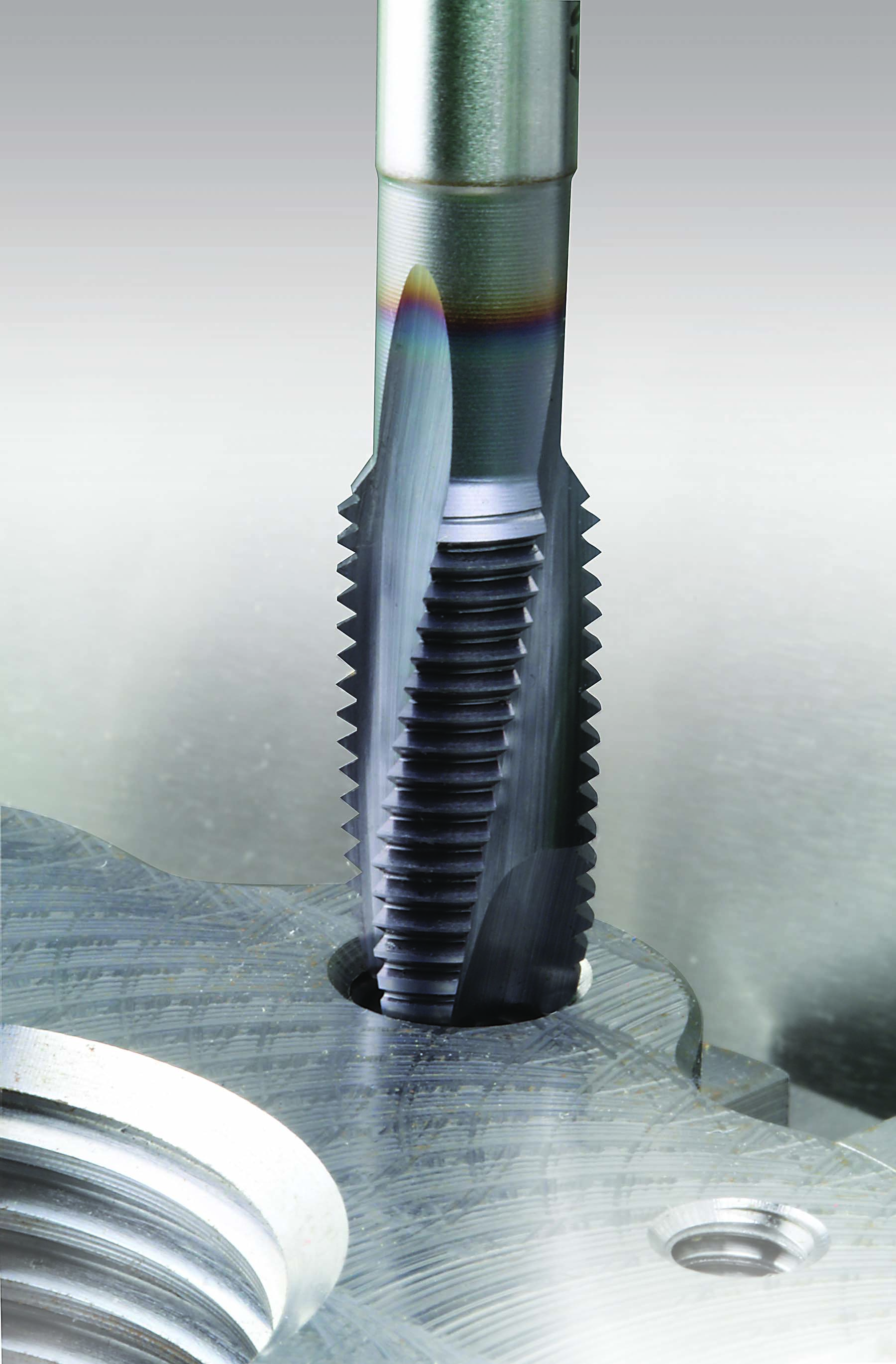
Here are just a few examples where knowledgeable application advice proved beneficial for increasing thread making productivity.
- For the longest tap life, establishing the proper tapping speeds for various materials is key. For example, a tapping speed of 3-16 sfm is recommended for both entering a hole and exiting the tapped hole when cutting nickel alloys.
- Also, when tapping nickel alloys, the highest level of lubricity is required to achieve the longest and most consistent tool life. Tapping lubricants in the form of an oil or paste are recommended and are ideally suited for maximizing tool performance. When tapping, emulsion coolants often lack sufficient oil concentration to achieve the best tap life in nickel alloys. If emulsion coolant is the only lubrication option available, then thread milling would be the preferred process for optimal tool performance.
- When it comes to thread milling, EMUGE recommends that manufacturers ask questions early on about programming the feed rate if the threading operation does not seem right. For example, a customer had been breaking thread mills, and a programming review revealed that the tool was being significantly overfed. A hole that should have taken close to a minute to thread was being done in just a few seconds. This was due to the feed rate being calculated on the centerline of the programmed arc instead of on the actual tool diameter, which is much larger.
- Application advice also helps when determining whether a single-plane or full milling section thread mill is the optimal choice. Because a single-plane thread mill can cut multiple pitch threads, shops don’t have to stock as many tools. However, a full milling section tool is much faster, and instead of making a couple dozen passes with a single-plane tool, a tool with the complete thread profile can produce any thread in two passes or less — geometry and material permitting. Note that single-plane thread mills certainly have their place and offer a versatile, dependable solution for producing full bottoming threads to within one pitch in a range of materials.
Shops Efficiently Thread Up
Incorporating the right threading tool and following application advice from knowledgeable cutting tool experts has proven to be instrumental in terms of quality, productivity and cost savings in the following real-world cases:
An aerospace job shop serving the defense and extrusion industries was encountering a high cycle time, poor tool life and an unstable process when threading Inconel 718. The shop was using a single-plane carbide thread mill that was taking over 30 minutes per hole to thread. Each workpiece required 10 passes per hole, and the tool was delivering poor thread quality. To solve the threading issues, the shop consulted with EMUGE and used the toolmaker’s THREADS-ALL/AERO thread mill with optimized feeds and speeds. Doing so allowed the shop to thread the same number of holes with only three passes per hole. The result was a cost savings of 76% per part with an annual savings of over $90,000.
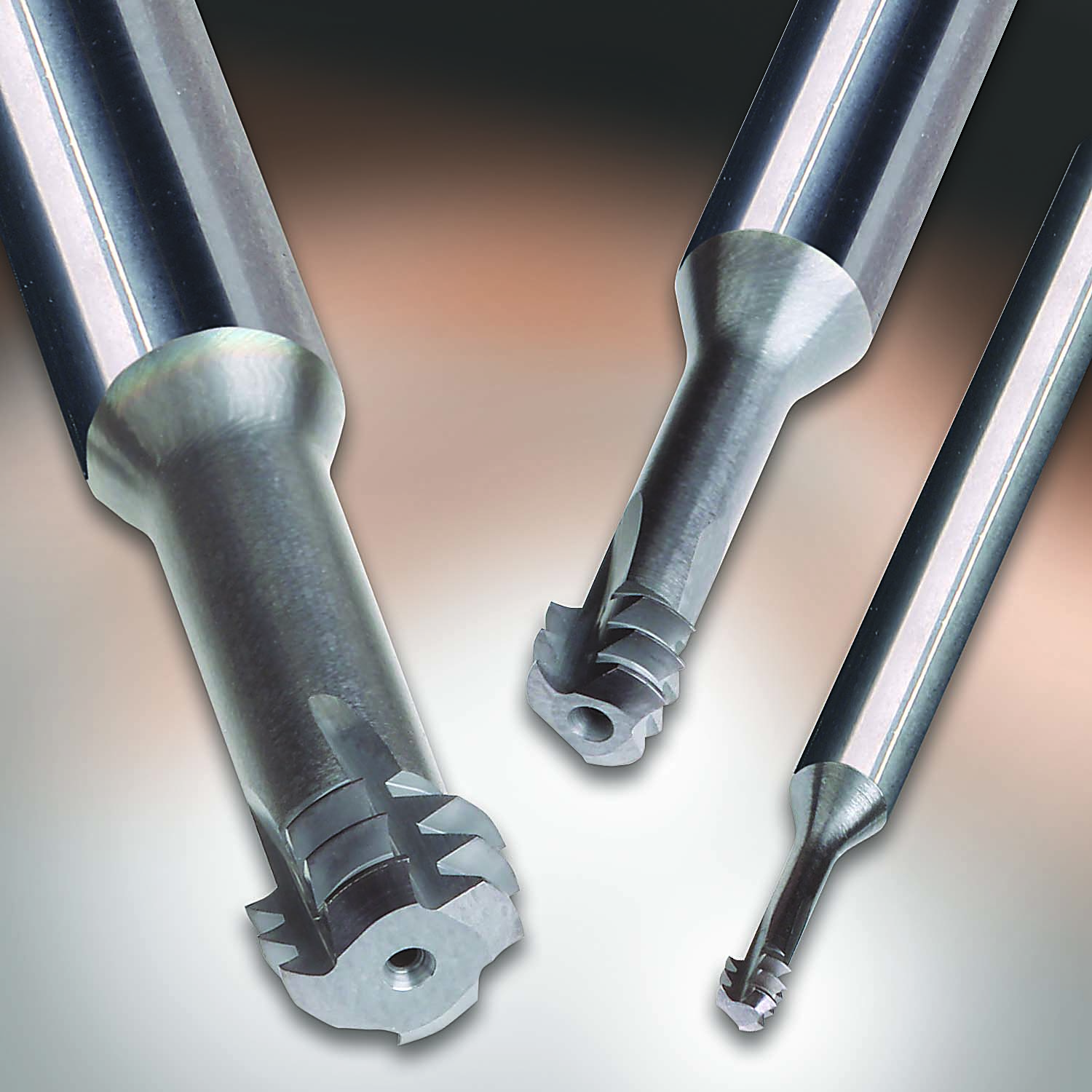
THREADS-ALL/AERO has a unique design that enables three tooth pitches to simultaneously rough and finish threads, reducing cycle times and dramatically increasing tool life up to 10 times longer than conventional tools. A left-hand helix flute design with left-hand spindle rotation greatly enhances stability and performance. The first tooth acts as a rougher, while the second and third teeth finish the full thread. The TIALN-T46 coating on the thread mills resists heat and wear, extending tool life. With this one tool, manufacturers can make STI threads for both through and blind holes.
A manufacturer of steel valves had been using a conventional tap to thread some 800 holes before the tool failed. Seeking a more productive solution, the manufacturer decided to investigate EMUGE taps. The first step was to conduct a trial to see which tap performed the best in the valve application. Ultimately, an EMUGE Z Tap threaded about 7,000 holes, which increased the number of holes per tap by approximately 90% compared with the previous tap.
EMUGE Z-Taps have an advanced chamfer geometry and rake/flute form in addition to the GLT-1 multi-layered coating, which produces a consistent, controllable chip formation that is released smoothly for fast and efficient chip removal. GLT-1 is uniquely structured with advanced heat resistance characteristics, along with an outer anti-friction layer. These elements synergistically combine to produce exceptional wear resistance and sliding properties that result in improved tool life, reduced torque, optimized chip evacuation and a superior thread finish.
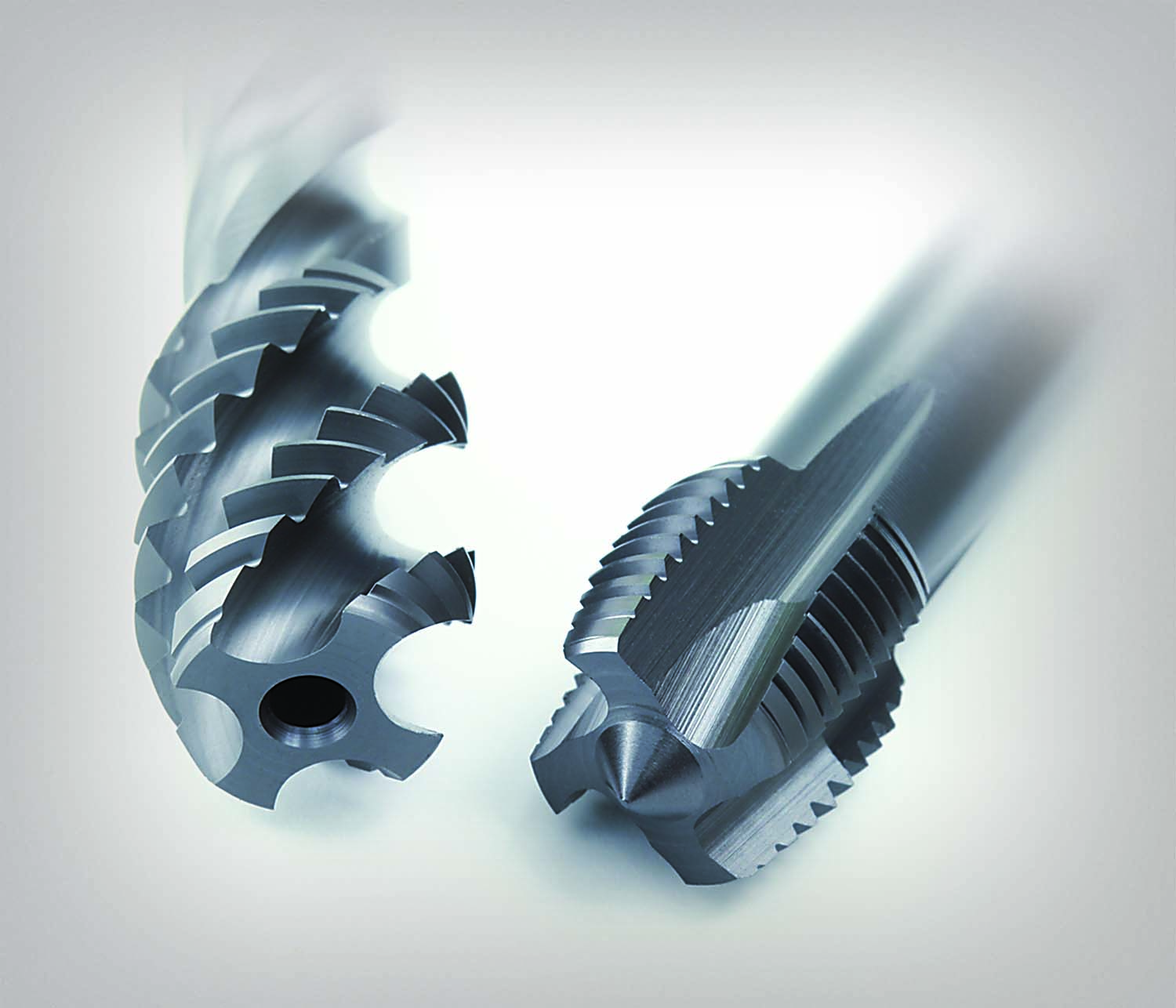
EMUGE Z-Taps also feature a large number of flutes and a short thread section to reduce friction, and a low cutting torque to reduce the occurrence of tap breakage and enable higher cutting speeds.
Using the right tool also helped a custom fabrication shop for engineering, welding, machining and testing related to manufacturing pressure vessels, vacuum chambers and cryogenic systems. The shop, which has many applications with part features that require threading, had been using application-specific EMUGE taps in materials such as titanium, Inconel and super alloys. When threading more common steel and aluminum alloys with taps from other toolmakers, taps frequently broke, so they tried the EMUGE MultiTAP high-performance, multi-purpose tap that eliminated the breakage issue. Now the shop is replacing all of its taps with EMUGE MultiTAPs.
The MultiTAP line ranges from cut taps to form taps with different coatings, in addition to taps with extended lengths, and NPT/NPTF pipe taps. The versatile MultiTAP features an innovative geometric design and a special base material and surface treatment that allows it to cut a wide range of materials such as carbon steel, steel, stainless steel, aluminum, cast iron, copper, brass and bronze. The taps are uniquely designed to produce threads within both 2B and 3B classes of fit, eliminating the guesswork required when calculating H-limits.
A manufacturer of balers, shredders and shears for the recycling industry uses abrasion-resistant materials that are hardened to build long lasting, reliable products. The materials are challenging to machine and are in the 35-46 HRC hardness range, requiring holes with strong threads. Taps that are long lasting and produce consistent results are vital, but when the manufacturer used budget-priced taps, breakage was a constant challenge that required frequent tool changes and part repairs.
The company consulted EMUGE, a test was performed and a single EMUGE 3/4” – 10 3BX C-Ti-style tap now enables the manufacturer to thread 300 to 400 holes or more on huge wear plates made of Hardox 450 steel (45 HRC) that are used as liners in the interior of cardboard balers. Prior to the EMUGE tap, the manufacturer was only able to thread 67 holes at most, without the tap failing.
Productivity increased over 20%, saving the manufacturer 50% of the cost per job. Though the EMUGE tap costs $50 more than the incumbent tap, it lasts much longer, such that only 17 EMUGE taps are needed for annual production of the liners as compared with 75 of the previous taps.
C-Ti taps feature a left-hand helical flute form and chamfer geometry that combines to optimize chip evacuation in the forward direction and add strength to the cutting teeth for enhanced tool life and process security. Advanced high-relief geometry (HRG) increases space between the friction surfaces for enhanced lubrication and reduced torque load in both forward and reverse directions. For example, HRG counteracts the high compressive forces produced by the extreme elastic memory of titanium. A TICN multi-layer PVD coating is applied to the tap for additional wear resistance. The taps produce a 3BX class of fit for internal UNJ threading applications.
Related Glossary Terms
- alloys
alloys
Substances having metallic properties and being composed of two or more chemical elements of which at least one is a metal.
- aluminum alloys
aluminum alloys
Aluminum containing specified quantities of alloying elements added to obtain the necessary mechanical and physical properties. Aluminum alloys are divided into two categories: wrought compositions and casting compositions. Some compositions may contain up to 10 alloying elements, but only one or two are the main alloying elements, such as copper, manganese, silicon, magnesium, zinc or tin.
- coolant
coolant
Fluid that reduces temperature buildup at the tool/workpiece interface during machining. Normally takes the form of a liquid such as soluble or chemical mixtures (semisynthetic, synthetic) but can be pressurized air or other gas. Because of water’s ability to absorb great quantities of heat, it is widely used as a coolant and vehicle for various cutting compounds, with the water-to-compound ratio varying with the machining task. See cutting fluid; semisynthetic cutting fluid; soluble-oil cutting fluid; synthetic cutting fluid.
- emulsion
emulsion
Suspension of one liquid in another, such as oil in water.
- extrusion
extrusion
Conversion of an ingot or billet into lengths of uniform cross section by forcing metal to flow plastically through a die orifice.
- feed
feed
Rate of change of position of the tool as a whole, relative to the workpiece while cutting.
- flutes
flutes
Grooves and spaces in the body of a tool that permit chip removal from, and cutting-fluid application to, the point of cut.
- gang cutting ( milling)
gang cutting ( milling)
Machining with several cutters mounted on a single arbor, generally for simultaneous cutting.
- hardness
hardness
Hardness is a measure of the resistance of a material to surface indentation or abrasion. There is no absolute scale for hardness. In order to express hardness quantitatively, each type of test has its own scale, which defines hardness. Indentation hardness obtained through static methods is measured by Brinell, Rockwell, Vickers and Knoop tests. Hardness without indentation is measured by a dynamic method, known as the Scleroscope test.
- lubricity
lubricity
Measure of the relative efficiency with which a cutting fluid or lubricant reduces friction between surfaces.
- milling
milling
Machining operation in which metal or other material is removed by applying power to a rotating cutter. In vertical milling, the cutting tool is mounted vertically on the spindle. In horizontal milling, the cutting tool is mounted horizontally, either directly on the spindle or on an arbor. Horizontal milling is further broken down into conventional milling, where the cutter rotates opposite the direction of feed, or “up” into the workpiece; and climb milling, where the cutter rotates in the direction of feed, or “down” into the workpiece. Milling operations include plane or surface milling, endmilling, facemilling, angle milling, form milling and profiling.
- milling machine ( mill)
milling machine ( mill)
Runs endmills and arbor-mounted milling cutters. Features include a head with a spindle that drives the cutters; a column, knee and table that provide motion in the three Cartesian axes; and a base that supports the components and houses the cutting-fluid pump and reservoir. The work is mounted on the table and fed into the rotating cutter or endmill to accomplish the milling steps; vertical milling machines also feed endmills into the work by means of a spindle-mounted quill. Models range from small manual machines to big bed-type and duplex mills. All take one of three basic forms: vertical, horizontal or convertible horizontal/vertical. Vertical machines may be knee-type (the table is mounted on a knee that can be elevated) or bed-type (the table is securely supported and only moves horizontally). In general, horizontal machines are bigger and more powerful, while vertical machines are lighter but more versatile and easier to set up and operate.
- physical vapor deposition ( PVD)
physical vapor deposition ( PVD)
Tool-coating process performed at low temperature (500° C), compared to chemical vapor deposition (1,000° C). Employs electric field to generate necessary heat for depositing coating on a tool’s surface. See CVD, chemical vapor deposition.
- pitch
pitch
1. On a saw blade, the number of teeth per inch. 2. In threading, the number of threads per inch.
- tap
tap
Cylindrical tool that cuts internal threads and has flutes to remove chips and carry tapping fluid to the point of cut. Normally used on a drill press or tapping machine but also may be operated manually. See tapping.
- tapping
tapping
Machining operation in which a tap, with teeth on its periphery, cuts internal threads in a predrilled hole having a smaller diameter than the tap diameter. Threads are formed by a combined rotary and axial-relative motion between tap and workpiece. See tap.
- threading
threading
Process of both external (e.g., thread milling) and internal (e.g., tapping, thread milling) cutting, turning and rolling of threads into particular material. Standardized specifications are available to determine the desired results of the threading process. Numerous thread-series designations are written for specific applications. Threading often is performed on a lathe. Specifications such as thread height are critical in determining the strength of the threads. The material used is taken into consideration in determining the expected results of any particular application for that threaded piece. In external threading, a calculated depth is required as well as a particular angle to the cut. To perform internal threading, the exact diameter to bore the hole is critical before threading. The threads are distinguished from one another by the amount of tolerance and/or allowance that is specified. See turning.
- titanium carbonitride ( TiCN)
titanium carbonitride ( TiCN)
Often used as a tool coating. See coated tools.
- wear resistance
wear resistance
Ability of the tool to withstand stresses that cause it to wear during cutting; an attribute linked to alloy composition, base material, thermal conditions, type of tooling and operation and other variables.