Dear Doc: We battle “barber pole” in cylindrical-traverse grinding. Where does it come from? And how can we get rid of it?
The Doc replies: Barber pole, also called pitch lines, screw lines, lead lines, traverse lines, thread lines and many other names, is caused by a Z-axis deviation in wheel shape (or even wheel sharpness) being imparted into the workpiece. As the wheel traverses the workpiece, this deviation repeats itself every pitch distance, which is calculated by: pitch (in inches or mm) = traverse velocity (in inches/minute or mm/minute) ÷ workpiece RPM.
This deviation doesn’t have to be large. In fact, often it’s so small that it can’t be measured. But it can be seen with the naked eye.
The two most common causes are a worn wheel and a misalignment between the wheel Z-axis and the workpiece Z-axis.
Let’s start with wheel wear. The figure shows different wheel-wear profiles. In most situations where the overlap ratio is greater than 2, the wheel rounds up, either in the middle or on one side. The end result is that the imperfect wheel imparts itself into the workpiece – and repeats itself every pitch distance.
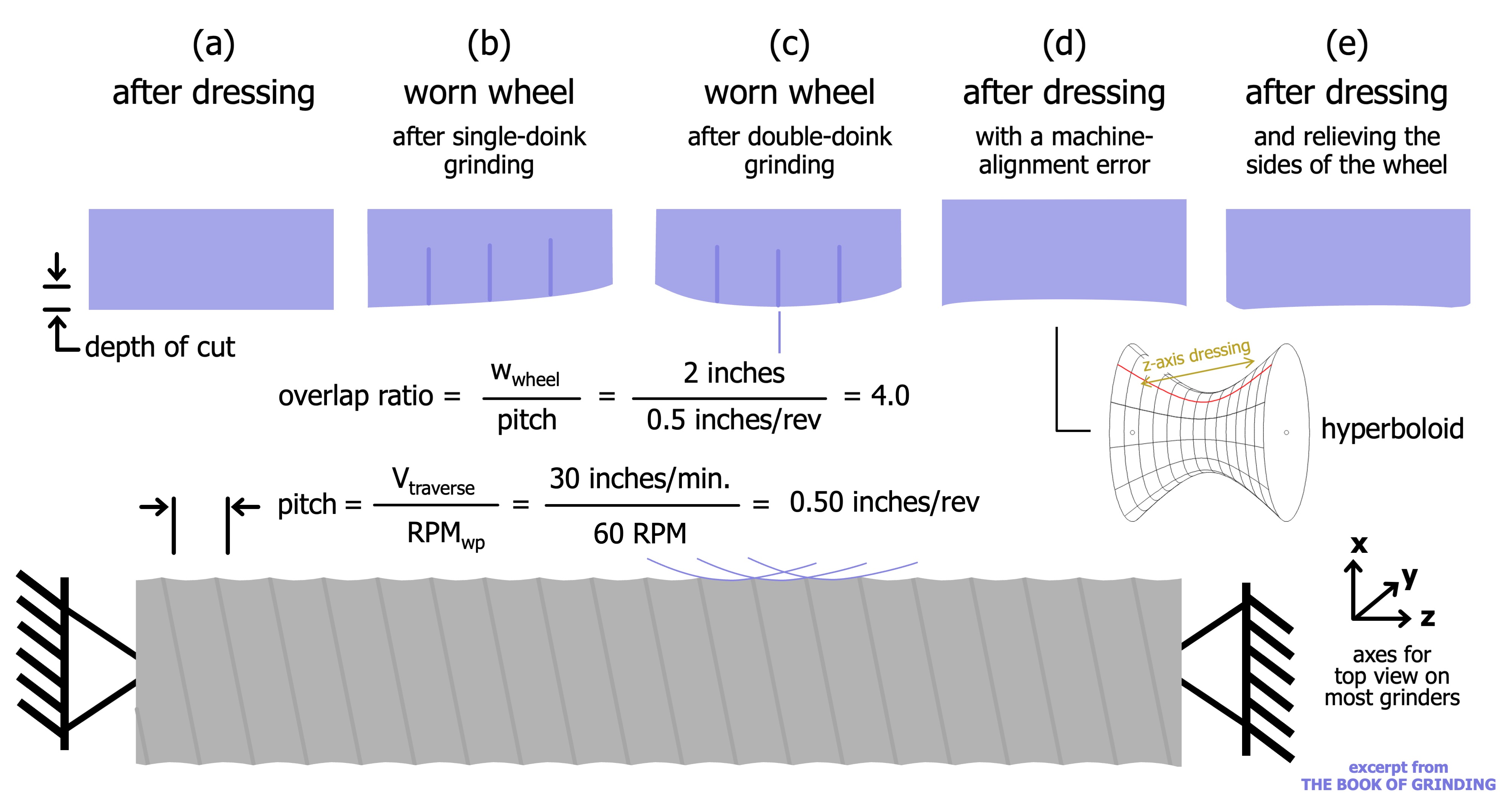
The solution? Dress, which turns your wheel back into a cylinder.
Another common cause is a Z-axis on the wheel surface that is not parallel to the Z-axis on the workpiece. There can be several reasons for this.
Let’s say that last month on the nightshift, Joe the Grinder crashed the wheel. Joe didn’t notice anything bad and didn’t tell anybody. But when Joe crashed it, the spindle-assembly shifted ever so slightly around the x-axis.
Now, when the dressing diamond traverses the slightly skewed wheel (in the Z-axis), it doesn’t dress a cylinder into the wheel. It dresses a hyperboloid. (The shape you get on a regulating wheel in cylindrical grinding.) The edges of that hyperboloid are sharp (see figure). When the wheel traverses the workpiece, those sharp edges dig in, creating pitch lines.
What’s the solution? Fix that misalignment in the spindle. But that takes time and costs money. There’s a quick and dirty solution for reducing the problem: trim away those sharp edges. You can do this with the dresser or with an aluminum-oxide or boron-carbide (Norbide) stick. It doesn’t fix the source of the problem, but it gets rid of the sharp edges, drastically reducing the appearance of the pitch lines.
Finally, during finish-grind and sparkout, decrease that pitch distance, either by decreasing the traverse speed or by increasing the workpiece RPM. This doesn’t deal with the root of the problem, but it makes the deviations smaller by putting them closer together.
There are other causes of barber pole:
- A diamond tool that heats up (and therefore expands) as it traverses the wheel.
- Large wheel deflection from large normal or coolant-hydroplaning forces.
- A wheel that is swiveled (say 30º) and is dressed at a point that is different than the point where grinding occurs (which creates a parabolic taper on the wheel that is not parallel to the workpiece).
- A Z-axis traverse on an overhead dresser that it not parallel to the Z-axis traverse of the workpiece.
Last week I was on a cylindrical grinder with moderate barber pole. We dressed the wheel. That reduced the visual appearance by 65%. Then we relieved the side of the wheel. That took it down another 35%. What about that last 5%? That can be difficult if not impossible to eliminate.
Related Glossary Terms
- cylindrical grinding
cylindrical grinding
Grinding operation in which the workpiece is rotated around a fixed axis while the grinding wheel is fed into the outside surface in controlled relation to the axis of rotation. The workpiece is usually cylindrical, but it may be tapered or curvilinear in profile. See centerless grinding; grinding.
- dressing
dressing
Removal of undesirable materials from “loaded” grinding wheels using a single- or multi-point diamond or other tool. The process also exposes unused, sharp abrasive points. See loading; truing.
- grinding
grinding
Machining operation in which material is removed from the workpiece by a powered abrasive wheel, stone, belt, paste, sheet, compound, slurry, etc. Takes various forms: surface grinding (creates flat and/or squared surfaces); cylindrical grinding (for external cylindrical and tapered shapes, fillets, undercuts, etc.); centerless grinding; chamfering; thread and form grinding; tool and cutter grinding; offhand grinding; lapping and polishing (grinding with extremely fine grits to create ultrasmooth surfaces); honing; and disc grinding.
- parallel
parallel
Strip or block of precision-ground stock used to elevate a workpiece, while keeping it parallel to the worktable, to prevent cutter/table contact.
- pitch
pitch
1. On a saw blade, the number of teeth per inch. 2. In threading, the number of threads per inch.